Selecting the right bolt is an important aspect of any bolted flange connection. And, to ensure a reliable seal, selecting the correct coating option for bolts can be just as important. While there are many different coating options available, zinc, cadmium, and PTFE are three of the most popular.
When selecting a bolt for a flanged connection, there are three key properties to consider: 1) strength, 2) temperature range, and 3) corrosion resistance. ASME B16.5, the standard for “Pipe Flanges and Flanged Fittings” (1/2” to 24”), specifies the bolt diameter for each flange. However, the bolt material of construction and type/class must still be determined. Regarding strength, the bolts must be strong enough to compress the gasket sufficiently to create a seal without breaking or deforming. Table 1.1-2 in B16.5 lists some bolting materials and their specifications.
Once a bolt material/specification that meets the strength requirement of the flanged connection is designated, it is important to confirm that the bolt will not exceed its temperature limitations while in service. Because the bolts are located outside of the process stream, it is important to note that unless they are under insulation, they should be at least somewhat closer to ambient temperature than the process. In fact, ASME B31.3 states that uninsulated bolting can be assumed to be 80% of the fluid temperature.
Lastly, the corrosive risks should be reviewed. Severe bolt corrosion causes many concerns. For one, it makes the bolt disassembly extremely difficult, usually requiring a grinder or cutter to open the flange. Corrosion can also reduce the strength of the bolt through thinning or embrittlement. Weakened bolts are then susceptible to breaking or elongating, which greatly increases the potential for a leak. Zinc, cadmium, and PTFE are three of the most popular coatings to reduce bolt corrosion.
Table 1: Partial list of bolting specifications from ASME B16.5.
Another benefit of these coatings is that they can provide a smoother thread surface. With a smoother thread surface, there is less friction between the nut and bolt (lower nut or k-factor), which indicates more of the applied force (through torque) goes into compressing the gasket rather than overcoming friction. The use of lubrication will further lower the nut-factor and help to maintain more consistency, as slight variations in coating thickness can impact the nut-factor consistency from bolt-to-bolt.
Zinc and cadmium coatings work as a sacrificial barrier to prolong the life of the base metal. In a corrosive environment, the zinc/cadmium will degrade first before the base metal is attacked by corrosion. All three options are meant to protect from environmental and galvanic corrosion. Environmental (or atmospheric) corrosion occurs when the environment itself is corrosive to the bolt. This could be a marine environment, proximity to an open steam leak, cooling tower drift, or anywhere where oxygen and water can be present.
Galvanic corrosion occurs when two different metals are in contact with each other in the presence of an electrolyte. This could be as simple as using plain carbon steel bolts on a stainless-steel flange. The carbon steel components will preferentially corrode in this situation. Ideally, the bolts and coatings would also be compatible with the process. A small leak can quickly turn into a massive spill if the bolts essentially dissolve in the process.
Zinc coatings are more popular than cadmium, as cadmium is highly toxic and banned in many countries. Both coatings tend to be more durable than PTFE coatings as the PTFE coating can be removed or damaged more easily during the bolted flange assembly process. Zinc and cadmium are normally used to give cheaper bolting materials better corrosion resistance. Even after coating, these bolts are substantially less expensive than their stainless-steel counterparts. In fact, as cost savings, some prefer to use zinc or cadmium-coated fasteners on stainless steel flanges.
However, both zinc and cadmium, in the presence of an electrolyte, will preferentially corrode on stainless steel flanges, as stainless steel is more noble than both of these coating options. An example of this is shown in Figures 1 and 2. These are zinc-plated B7s, with zinc-coated 2H nuts, which are in contact with a 316 stainless steel flange. Notice how the nearest nut on the bottom side of the flange (Figure 1) shows no corrosion because rainwater cannot accumulate there.
When selecting a bolt for a flanged connection, there are three key properties to consider: 1) strength, 2) temperature range, and 3) corrosion resistance. ASME B16.5, the standard for “Pipe Flanges and Flanged Fittings” (1/2” to 24”), specifies the bolt diameter for each flange. However, the bolt material of construction and type/class must still be determined. Regarding strength, the bolts must be strong enough to compress the gasket sufficiently to create a seal without breaking or deforming. Table 1.1-2 in B16.5 lists some bolting materials and their specifications.
Once a bolt material/specification that meets the strength requirement of the flanged connection is designated, it is important to confirm that the bolt will not exceed its temperature limitations while in service. Because the bolts are located outside of the process stream, it is important to note that unless they are under insulation, they should be at least somewhat closer to ambient temperature than the process. In fact, ASME B31.3 states that uninsulated bolting can be assumed to be 80% of the fluid temperature.
Lastly, the corrosive risks should be reviewed. Severe bolt corrosion causes many concerns. For one, it makes the bolt disassembly extremely difficult, usually requiring a grinder or cutter to open the flange. Corrosion can also reduce the strength of the bolt through thinning or embrittlement. Weakened bolts are then susceptible to breaking or elongating, which greatly increases the potential for a leak. Zinc, cadmium, and PTFE are three of the most popular coatings to reduce bolt corrosion.
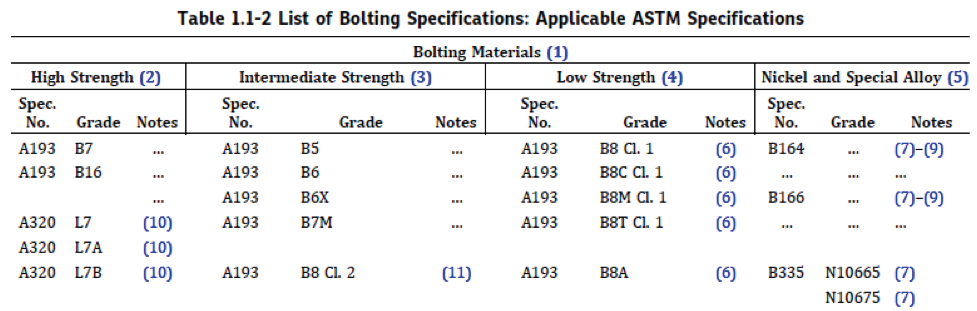
Another benefit of these coatings is that they can provide a smoother thread surface. With a smoother thread surface, there is less friction between the nut and bolt (lower nut or k-factor), which indicates more of the applied force (through torque) goes into compressing the gasket rather than overcoming friction. The use of lubrication will further lower the nut-factor and help to maintain more consistency, as slight variations in coating thickness can impact the nut-factor consistency from bolt-to-bolt.
Zinc and cadmium coatings work as a sacrificial barrier to prolong the life of the base metal. In a corrosive environment, the zinc/cadmium will degrade first before the base metal is attacked by corrosion. All three options are meant to protect from environmental and galvanic corrosion. Environmental (or atmospheric) corrosion occurs when the environment itself is corrosive to the bolt. This could be a marine environment, proximity to an open steam leak, cooling tower drift, or anywhere where oxygen and water can be present.
Galvanic corrosion occurs when two different metals are in contact with each other in the presence of an electrolyte. This could be as simple as using plain carbon steel bolts on a stainless-steel flange. The carbon steel components will preferentially corrode in this situation. Ideally, the bolts and coatings would also be compatible with the process. A small leak can quickly turn into a massive spill if the bolts essentially dissolve in the process.
Zinc coatings are more popular than cadmium, as cadmium is highly toxic and banned in many countries. Both coatings tend to be more durable than PTFE coatings as the PTFE coating can be removed or damaged more easily during the bolted flange assembly process. Zinc and cadmium are normally used to give cheaper bolting materials better corrosion resistance. Even after coating, these bolts are substantially less expensive than their stainless-steel counterparts. In fact, as cost savings, some prefer to use zinc or cadmium-coated fasteners on stainless steel flanges.
However, both zinc and cadmium, in the presence of an electrolyte, will preferentially corrode on stainless steel flanges, as stainless steel is more noble than both of these coating options. An example of this is shown in Figures 1 and 2. These are zinc-plated B7s, with zinc-coated 2H nuts, which are in contact with a 316 stainless steel flange. Notice how the nearest nut on the bottom side of the flange (Figure 1) shows no corrosion because rainwater cannot accumulate there.
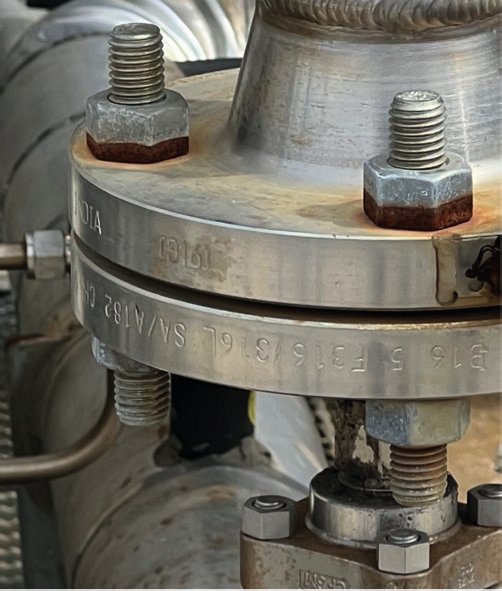
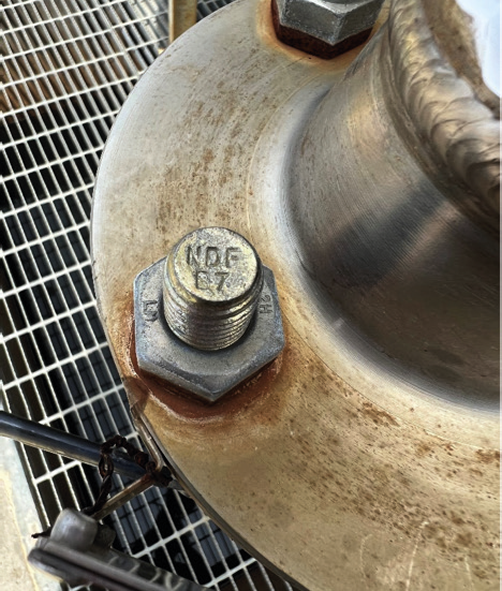
There are multiple ways to coat a fastener with zinc. The two most common ways are via plating and galvanizing. Plating leaves a nice, shiny finish and is accomplished through the electrodeposition or electroplating process. This process requires a clean fastener, free from rust and other impurities, which is submerged in a zinc bath. By sending a current through the bath, the bolt/component becomes plated with a thin layer of zinc. Stronger and harder steels are at higher risk for hydrogen embrittlement due to being more brittle. Hydrogen embrittlement occurs when tiny hydrogen atoms can permeate the steel and accumulate. This accumulation, in addition to stress, will cause cracking and has the potential for catastrophic failure while in service.
As both the cleaning process and electroplating itself are sources of hydrogen, it is important that plated high-strength (≥ 170 ksi) and high-hardness (≥ 39 HRC) fasteners undergo an additional baking process to allow the hydrogen to exit the close-knit, rigid molecular structure of the high-strength/high-hardness steel. ASTM B633 (Standard Specification for Electrodeposited Coatings of Zinc on Iron and Steel) and ASTM F1941 (Standard Specification for Electrodeposited Coatings on Mechanical Fasteners) are both fantastic resources that the end user should be familiar with prior to using or purchasing zinc-plated hardware.
F1941 lists several different common coating materials, including cadmium and zinc alloys, several thickness options, and conversion coating options.
As the zinc protects the base steel, the conversion coating protects the zinc and provides it with one of several colors. This conversion coating used to be made from hexavalent chromate. But, like cadmium, it is toxic, and its use is currently dwindling due to RoHS regulations. Trivalent chromium is now used in its place. The most popular colors are clear and yellow, however these colors are not indicative of the coating type. So, just because a bin of bolts/nuts is yellow does not mean it is either cadmium or zinc; it could be a mixture of both. The easiest way to differentiate them is through Positive Material Identification (PMI).
The other most common technique to apply a zinc coating is by hot dip galvanizing. Whereas electrodeposition leaves a shiny appearance with a zinc thickness of 3 – 12 μm (0.0001 – 0.0005”), zinc applied via hot dip galvanizing leaves a dull appearance with a thickness of approximately 50 μm (0.0020”). See Figures 3 and 4 for a side-by-side comparison. This thicker layer adds to the corrosion protection. The hot dip process requires clean steel fasteners to be dipped in molten zinc, typically around 850°F. Because of the thicker coating, over-tapping one of the components is required to get the bolt and nut to fit together properly.
ASTM A153, the “Standard Specification for Zinc Coating (Hot-Dip) on Iron and Steel Hardware”, prohibits the cutting and rolling of zinc-coated threads but allows for the tapping of nut threads or tapped holes after galvanizing. So, it is common to tap the nut after galvanizing in order to account for the bolt’s coating, with the expectation that the nut threads will be protected by the zinc-coated bolt threads. However, at least one manufacturer mentioned that it is common for the nuts to permanently bond to the bolt due to the buildup of corrosion products and that, because of some thickness variation, hot-dipped fasteners are at risk for varying nut factors leading to inconsistent forces generated from stud to stud even when targeting the same torque value. Hydrogen embrittlement of high-strength/high-hardness steels is also a cause for concern in the hot dip process. Alternative pre-dip cleaning methods should be employed to avoid this issue.
As previously mentioned, cadmium use is banned in several countries. Cadmium coatings, then, are mostly available from overseas manufacturers. The most popular way to coat bolts and fasteners with cadmium is by electrodeposition, following the same procedures described above. Cadmium generally has better corrosion resistance than zinc, especially in a salt atmosphere. However, a thicker coating of zinc can perform just as well or better. This is a reason why some prefer the hot-dipped galvanized option over electrode-position. Whereas zinc can have a buildup of protective corrosion products over time, making the disassembly of zinc-coated fasteners difficult, cadmium-coated fasteners do not have the same issue.
As both the cleaning process and electroplating itself are sources of hydrogen, it is important that plated high-strength (≥ 170 ksi) and high-hardness (≥ 39 HRC) fasteners undergo an additional baking process to allow the hydrogen to exit the close-knit, rigid molecular structure of the high-strength/high-hardness steel. ASTM B633 (Standard Specification for Electrodeposited Coatings of Zinc on Iron and Steel) and ASTM F1941 (Standard Specification for Electrodeposited Coatings on Mechanical Fasteners) are both fantastic resources that the end user should be familiar with prior to using or purchasing zinc-plated hardware.
F1941 lists several different common coating materials, including cadmium and zinc alloys, several thickness options, and conversion coating options.
As the zinc protects the base steel, the conversion coating protects the zinc and provides it with one of several colors. This conversion coating used to be made from hexavalent chromate. But, like cadmium, it is toxic, and its use is currently dwindling due to RoHS regulations. Trivalent chromium is now used in its place. The most popular colors are clear and yellow, however these colors are not indicative of the coating type. So, just because a bin of bolts/nuts is yellow does not mean it is either cadmium or zinc; it could be a mixture of both. The easiest way to differentiate them is through Positive Material Identification (PMI).
The other most common technique to apply a zinc coating is by hot dip galvanizing. Whereas electrodeposition leaves a shiny appearance with a zinc thickness of 3 – 12 μm (0.0001 – 0.0005”), zinc applied via hot dip galvanizing leaves a dull appearance with a thickness of approximately 50 μm (0.0020”). See Figures 3 and 4 for a side-by-side comparison. This thicker layer adds to the corrosion protection. The hot dip process requires clean steel fasteners to be dipped in molten zinc, typically around 850°F. Because of the thicker coating, over-tapping one of the components is required to get the bolt and nut to fit together properly.
ASTM A153, the “Standard Specification for Zinc Coating (Hot-Dip) on Iron and Steel Hardware”, prohibits the cutting and rolling of zinc-coated threads but allows for the tapping of nut threads or tapped holes after galvanizing. So, it is common to tap the nut after galvanizing in order to account for the bolt’s coating, with the expectation that the nut threads will be protected by the zinc-coated bolt threads. However, at least one manufacturer mentioned that it is common for the nuts to permanently bond to the bolt due to the buildup of corrosion products and that, because of some thickness variation, hot-dipped fasteners are at risk for varying nut factors leading to inconsistent forces generated from stud to stud even when targeting the same torque value. Hydrogen embrittlement of high-strength/high-hardness steels is also a cause for concern in the hot dip process. Alternative pre-dip cleaning methods should be employed to avoid this issue.
As previously mentioned, cadmium use is banned in several countries. Cadmium coatings, then, are mostly available from overseas manufacturers. The most popular way to coat bolts and fasteners with cadmium is by electrodeposition, following the same procedures described above. Cadmium generally has better corrosion resistance than zinc, especially in a salt atmosphere. However, a thicker coating of zinc can perform just as well or better. This is a reason why some prefer the hot-dipped galvanized option over electrode-position. Whereas zinc can have a buildup of protective corrosion products over time, making the disassembly of zinc-coated fasteners difficult, cadmium-coated fasteners do not have the same issue.
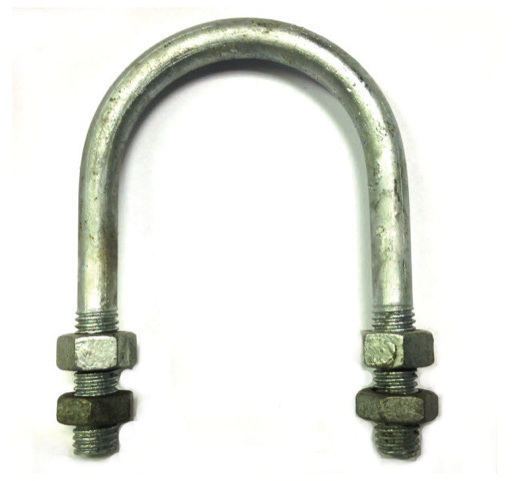
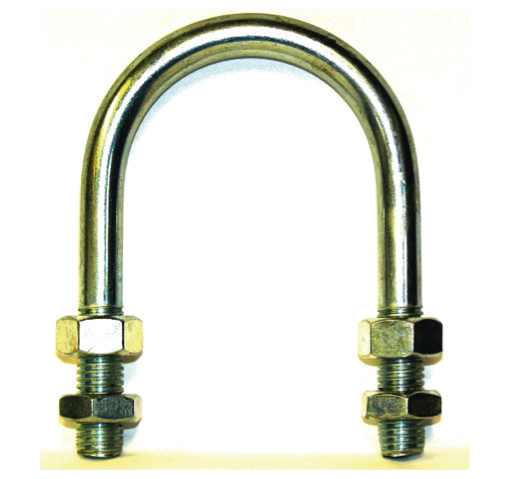
ASTM A193, the standard specification for Alloy-Steel and Stainless Steel Bolting for High Temperature or High Pressure Service, states that the maximum allowable temperature for a coated/plated bolt is half of the coating’s melting point because of the potential for liquid and solid metal embrittlement. The melting point for zinc is 780°F, and for cadmium is 600°F. Therefore, the temperature limits for zinc-coated and cadmium-coated bolts are 390°F and 300°F, respectively. As far as cost goes, cadmium-coated ASTM A193-B7 bolts are just slightly more expensive than plain B7 bolts (~10-20%).
Both versions of zinc coatings are about the same price, approximately 40-50% more expensive than cadmium coatings. PTFE coatings are about 110-120% of the cost of plain B7 bolts and about 30% more expensive than both zinc coatings. ASTM A193-B8M-CL2 bolts are 5-6 times the cost of a plain B7 and almost three times the cost of a zinc-coated B7. Lastly, zinc fumes are also toxic, so welding on or near zinc-coated components should be avoided. Electrodeposited coatings of cadmium are covered by ASTM B766 and ASTM F1941.
Even though they tend to be more expensive than zinc and cadmium coatings, PTFE-coated bolts are the most popular option for many chemical manufacturing facilities. PTFE is by far the most corrosion-resistant of the three coating options and has a temperature limit similar to (or slightly higher than) zinc coatings. There are several different types/manufacturers of PTFE coatings, such as Xylan and FluoroKote. There is no governing ASTM for the application of PTFE coatings; the coating procedure is provided by the manufacturer, and the quality of the coating is heavily dependent upon the skill and experience of the technician. Like both the hot dip and electrodeposition processes, the PTFE coating process starts with a clean bolt that has been grit blasted to a white metal finish.
After cleaning, the bolts/components are dipped into zinc phosphate or another proprietary liquid. While this part of the process offers some corrosion protection, its main function is to act as a primer for the application of the PTFE coating. The bolts are then warmed in an oven, removed, and sprayed with the first coat of PTFE. They are then put back into the oven and cured, then cooled, and a second coating is applied. After the second coating, the bolts are oven-cured again, removed, inspected, and ready for use. The coating thickness requirements vary by manufacturer and type of fluoropolymer coating but generally will be 0.0008” – 0.002” thick.
Due to the additional thickness, bolts and/or nuts should be over-tapped to ensure a good fit during use. Most PTFE-coated fasteners are blue, but they are available in several different colors. Some end-users prefer to differentiate their PTFE-coated bolts, either by manufacturer, type, or by location, with the available color options. Aside from their distinct anti-corrosion advantages, PTFE coatings provide extremely smooth and low-friction thread surfaces (low nut-factor), meaning that good gasket compression can be achieved with even lower torque values when compared with zinc and cadmium coatings. These friction properties, however, can be variable, depending on the thickness consistency and quality of application. Lubricating PTFE-coated bolts will help to lessen this variability. Also, PTFE coatings have been known to thin or scrape off during the bolting process, usually in higher torque applications, leaving behind areas of exposed base metal.
These are just three of the most popular fastener coating options. There are many more to consider as well, with each having their own distinct advantages and disadvantages. When considering fastener options for new processes or improving upon existing processes or bad actors, it is best to review the available options and consult with coating experts to find the best solution for the situation.
Both versions of zinc coatings are about the same price, approximately 40-50% more expensive than cadmium coatings. PTFE coatings are about 110-120% of the cost of plain B7 bolts and about 30% more expensive than both zinc coatings. ASTM A193-B8M-CL2 bolts are 5-6 times the cost of a plain B7 and almost three times the cost of a zinc-coated B7. Lastly, zinc fumes are also toxic, so welding on or near zinc-coated components should be avoided. Electrodeposited coatings of cadmium are covered by ASTM B766 and ASTM F1941.
Even though they tend to be more expensive than zinc and cadmium coatings, PTFE-coated bolts are the most popular option for many chemical manufacturing facilities. PTFE is by far the most corrosion-resistant of the three coating options and has a temperature limit similar to (or slightly higher than) zinc coatings. There are several different types/manufacturers of PTFE coatings, such as Xylan and FluoroKote. There is no governing ASTM for the application of PTFE coatings; the coating procedure is provided by the manufacturer, and the quality of the coating is heavily dependent upon the skill and experience of the technician. Like both the hot dip and electrodeposition processes, the PTFE coating process starts with a clean bolt that has been grit blasted to a white metal finish.
After cleaning, the bolts/components are dipped into zinc phosphate or another proprietary liquid. While this part of the process offers some corrosion protection, its main function is to act as a primer for the application of the PTFE coating. The bolts are then warmed in an oven, removed, and sprayed with the first coat of PTFE. They are then put back into the oven and cured, then cooled, and a second coating is applied. After the second coating, the bolts are oven-cured again, removed, inspected, and ready for use. The coating thickness requirements vary by manufacturer and type of fluoropolymer coating but generally will be 0.0008” – 0.002” thick.
Due to the additional thickness, bolts and/or nuts should be over-tapped to ensure a good fit during use. Most PTFE-coated fasteners are blue, but they are available in several different colors. Some end-users prefer to differentiate their PTFE-coated bolts, either by manufacturer, type, or by location, with the available color options. Aside from their distinct anti-corrosion advantages, PTFE coatings provide extremely smooth and low-friction thread surfaces (low nut-factor), meaning that good gasket compression can be achieved with even lower torque values when compared with zinc and cadmium coatings. These friction properties, however, can be variable, depending on the thickness consistency and quality of application. Lubricating PTFE-coated bolts will help to lessen this variability. Also, PTFE coatings have been known to thin or scrape off during the bolting process, usually in higher torque applications, leaving behind areas of exposed base metal.
These are just three of the most popular fastener coating options. There are many more to consider as well, with each having their own distinct advantages and disadvantages. When considering fastener options for new processes or improving upon existing processes or bad actors, it is best to review the available options and consult with coating experts to find the best solution for the situation.