While there have been great advancements regarding traceability and identification technology in numerous areas of life; when it comes to valve packing, the technology has not advanced to match the need.
Challenged by these market needs, Teadit 2848 packing was engineered and designed to address fugitive emission requirements while providing complete traceability. This is accomplished through the development of a new technology called Teadit® TAGS™, which was awarded the Vaaler Award in Fluid Flow for 2021! Fugitive Emissions Journal recently had the pleasure of speaking with the Teadit team to learn more about the advantages, and beneficial impact, of its new technology.
Fugitive emissions from valves are one of the biggest environmental challenges faced by refineries and petrochemical plants. The use of certified low emissions packings is one method used by many end users to mitigate that impact. However, when it comes to identifying and tracking the use of such products in the field, additional challenges emerge. Questions arise concerning how users can correctly identify a compression packing once installed, or even once it is out of the box. To address this issue Teadit has developed a progressive technology for its 2848 packing: Teadit® TAGS™.
Unique Design
Teadit 2848, named after the fugitive emission standard ISO 15848, is braided with a yarn that has oxidation inhibited flexible graphite as its base and is reinforced with an innovative high-strength PTFE thread structure in a knitted jacket configuration. This high-strength, low-friction PTFE structure is embedded with luminescent Teadit® TAGS™, which are microscopic particles that carry the solution to identify the packing, assuring its full traceability. Figure 1 reflects this exclusive design.Teadit® TAGS™ are traceable particles that may have different forms, compositions, sizes, and are able to be detected by distinct apparatus. This ground-breaking design ensures the traceability of the product before, or even after, it has been in service.
Examples of these particles include phosphors and microdots. Both can be excited with a specific wavelength to be identified using the right equipment. For example, phosphors can be illuminated with a portable laser pen or an ultraviolet flashlight, depending upon the selection of the phosphor.
These ‘tags’ can retain information on packing fabrication, creating a uniquely identifiable fingerprint for the warrantied product that is invisible to the naked eye. Figure 2 shows this innovative product (US 10,989,304 B1), and its unique fingerprint.
Inseparable from the packing, Teadit® TAGS™ offer a permanent and much more reliable identification method that cannot be misplaced, switched off, or removed. It can dramatically reduce complications from product misidentification and have no impact on the performance of the product itself.
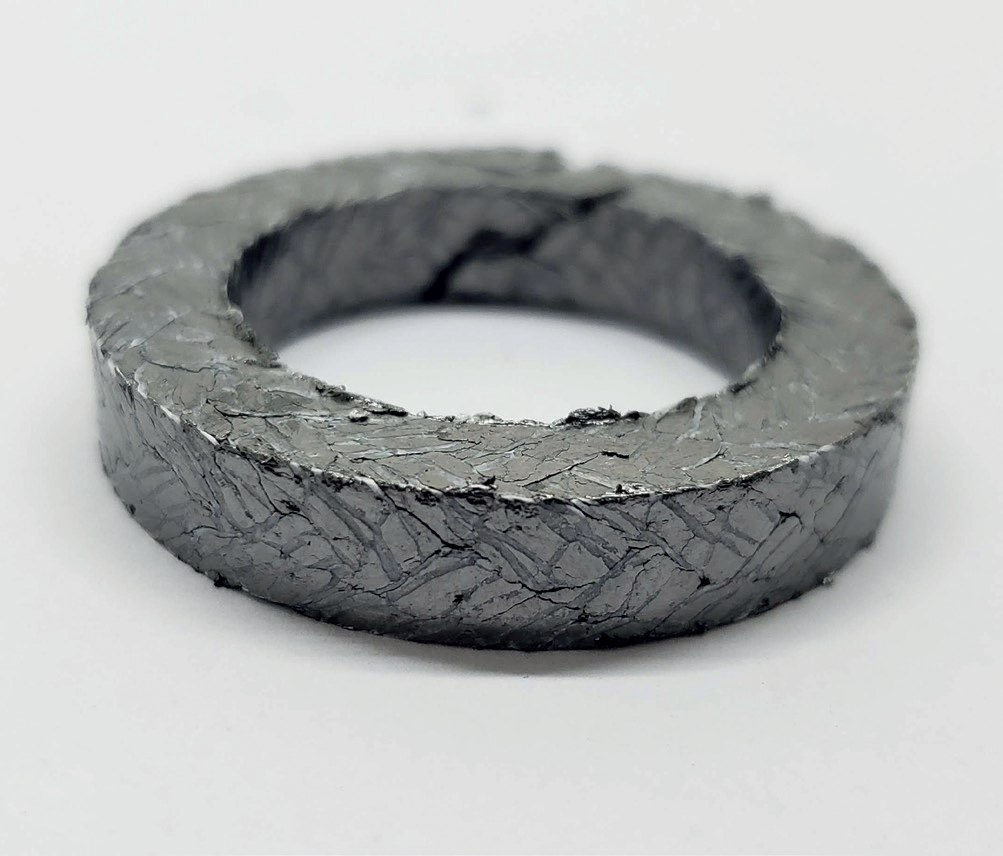
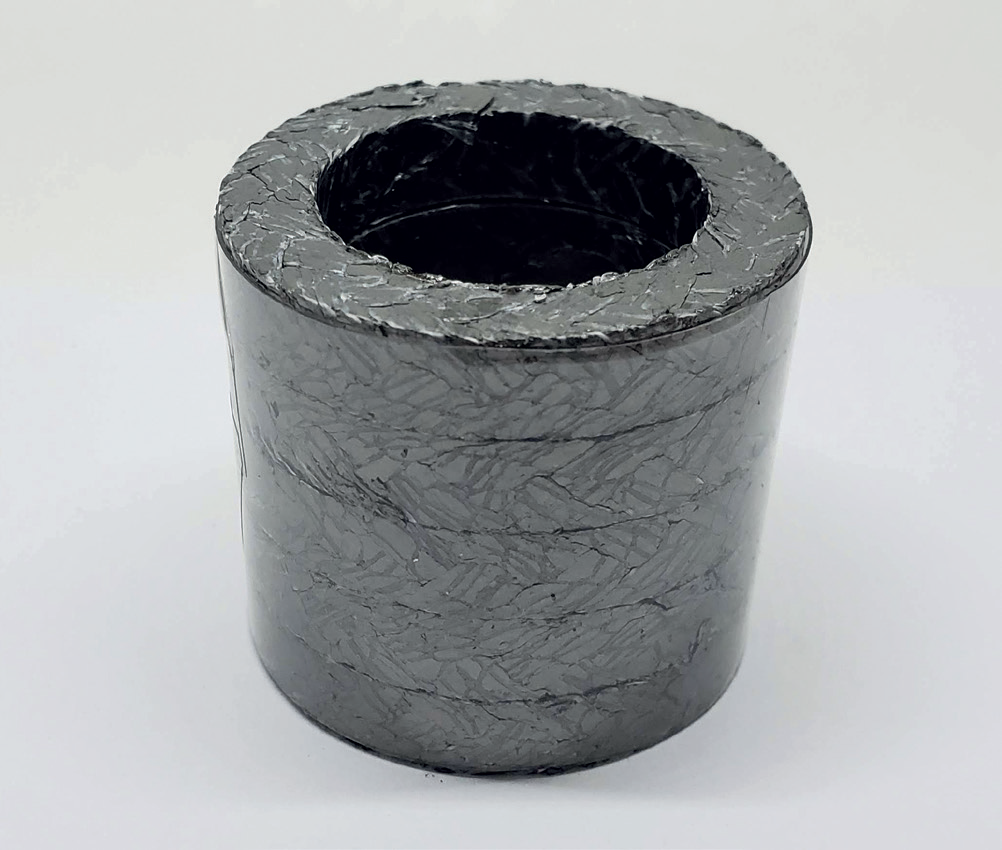
The use of a graphite with a high-strength PTFE jacket instead of the traditional Inconel jacket makes this novel compression packing a premium low emissions service product for valves that can resist high installation stresses. It is also ideal for sealing pump shafts, soot blowers, and similar pieces of equipment, especially in applications that require a low-friction, traceable, low emissions solution. “In addition to the use of PTFE knitting in lieu of the Inconel wire, the Patented Teadit Tags for identification of the product while in use are simply amazing,” said Rodney Roth, global valve SME. “Teadit 2848 will revolutionize sealing in Control Valves!”
With Teadit 2848 being self-lubricating and non-hardening, it is positioned as an ideal choice for any compression packing application requiring dimensional stability and high performance – including operational conditions with chemical services and high temperatures and pressures. Plants can benefit from having a single high-quality product that meets a variety of service requirements and reduce overall inventory.
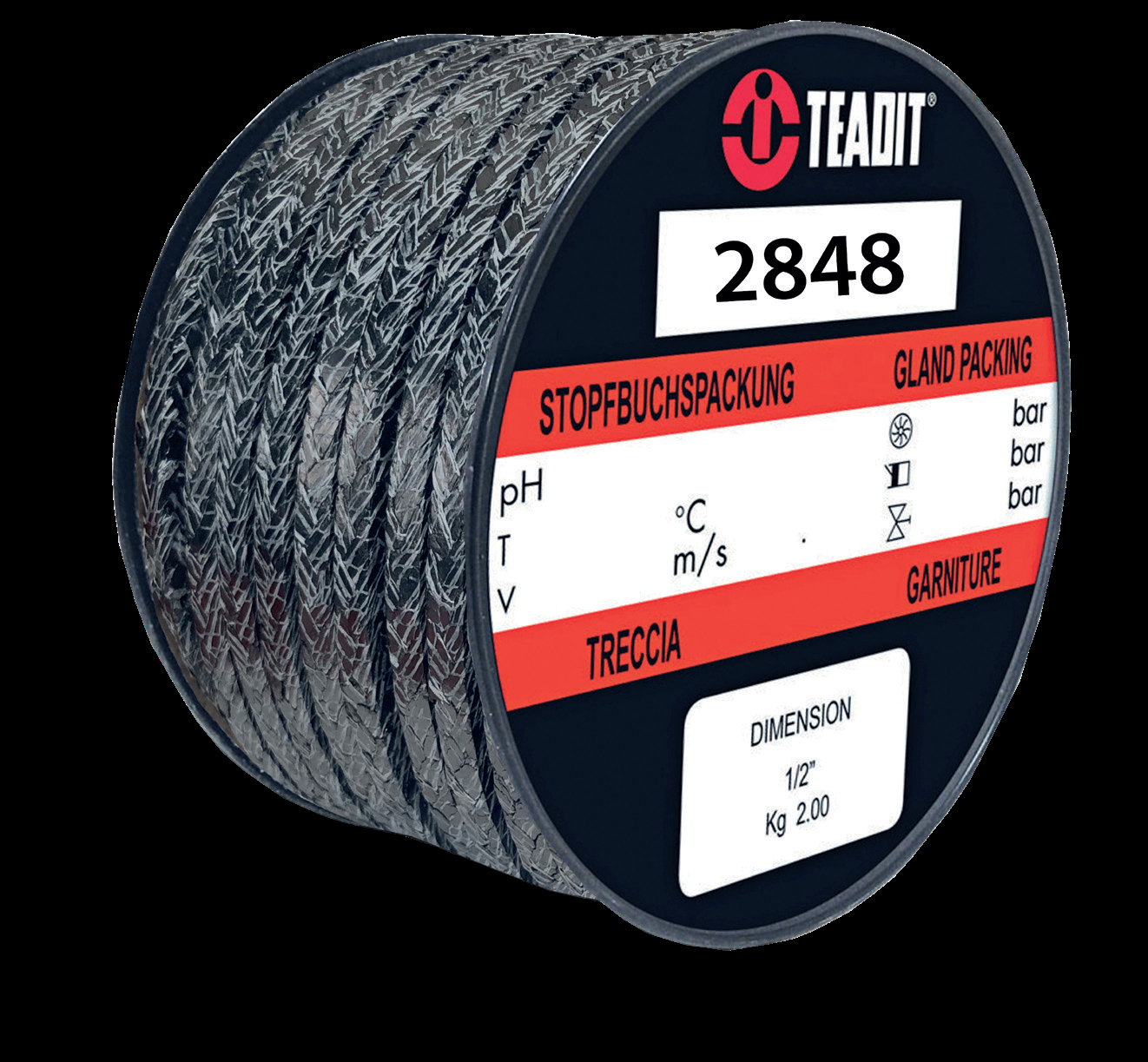
“TEADIT 2848 WILL REVOLUTIONIZE SEALING IN CONTROL VALVES!”
– RODNEY ROTH, GLOBAL VALVE SME.
Teadit: At a Glance
Teadit Group is recognized worldwide as a leader in the development and manufacturing of innovative products for critical fluid sealing processes. The wide variety of sealing solutions developed by Teadit have been important tools for many industries including the Oil & Gas, Chemical Processing, and Power Generation. Teadit has helped several industries achieve the goal of an emission-free environment within their facilities. Teadit is constantly investing in research and development to keep up with the evolution of the industry’s needs.Teadit North America is located in Houston, Texas with seven worldwide locations in South America, Europe, and Asia. The variety of sealing solutions developed by Teadit is fundamental to achieve the leakage-free goal in the many industries served. The quality and effectiveness of these solutions are based on management and innovation, which are the basis for all products manufactured at any Teadit plant. As a result of this continuous process of quality improvement, an ISO 9001 certification was obtained in Brazil, the United States, and Europe. The 64-year history of Teadit began in Rio de Janeiro and has led to more than twenty patents on products and process. Their corporate values of Integrity, Reliability, Safety, and being Customer Focused and all culminate in their vision statement: Sealing For A Safer And Greener Tomorrow.
Certified Low-Emission Packing
Controlling and reducing fugitive emissions has become an area of focus for many countries around the world in the last few years. The increase of stringent environmental regulations requires industry segments to carefully evaluate their equipment and services. This, in turn, has led to more and more demand for manufacturers to meet specifications. Doing so on block or shutoff valves is typically not a problem for packing manufacturers, as there are several brands of low emission packing on the market capable of providing this level of result. This performance is commonly achieved by using a braided packing with an Inconel jacket around the graphite yarn.But for control valves, a yarn with a metallic jacket is not ideal. Since control valves are typically continuously actuated, Teadit’s team of engineers set out determined to find an alternative to Inconel with the goal of greatly reducing the potential for stem drag, scoring, and elevated friction.
Teadit, one of the world’s only manufacturers of PTFE gasketing, ePTFE gasketing, and PTFE packing, immediately turned its attention to some of the research that they were doing with high strength PTFE fibers. PTFE fibers are more chemically resistant than other commonly used fibers like Nylon and Polyester and are stronger than materials like Aramid and Inconel. Outside of the sealing industry, PTFE fibers are used in a wide variety of applications including precision woven filters, high-performance ropes, industrial sowing threads, medical stitching, architectural fabrics, membrane reinforcement, and dental floss.
Using its high-strength PTFE fiber jacket, and after significant design work and internal testing, what Teadit developed is the packing with highest performance results yet seen on the low emission valve tests.
API 622 3rd edition is a common standard used to test packings for low emissions service. This test consists of sealing methane pressurized to 40 bar (580 psi). There are 1510 mechanical cycles and 5 thermal cycles, up to the specified temperature of 260°C (500°F). It is not uncommon for some low emission packings to pass this test with maximum leakage values of 10-20 ppm. Teadit 2848 was tested by a third-party lab and the results were staggering. The maximum leakage measured was only 1.0 ppm and averaged leakage recorded was a tiny 0.1 ppm!
ISO 15848-1 has several testing combinations, but the most stringent mechanical cycling test is Endurance Class CC3 with-out any adjustments. This test involves the evaluation of packing in 100,000 mechanical cycles and 4 thermal cycles, that is 66 times more cycles than the previously mentioned API 622 test. The Teadit 2848 was tested using 40 bar (580 psi) of methane in a 2-inch, Class 300 ASME B16.34 control valve cycling up to 260°C (500°F). Results of ISO 15848-1 are generally reported in terms of Tightness Class: with a Tightness Class of A ≤ 50 ppm, B ≤ 100 ppm, and C ≤ 500 ppm. It is acceptable to have a Tightness Class of B, but preferable to achieve Class A. The maximum leakage measured during the Teadit 2848 test was only 0.9 ppm and with an average leakage of 0.2 ppm, easily classifying for a Tightness Class A in the 100,000 cycle test.
Figure 3 shows the results.
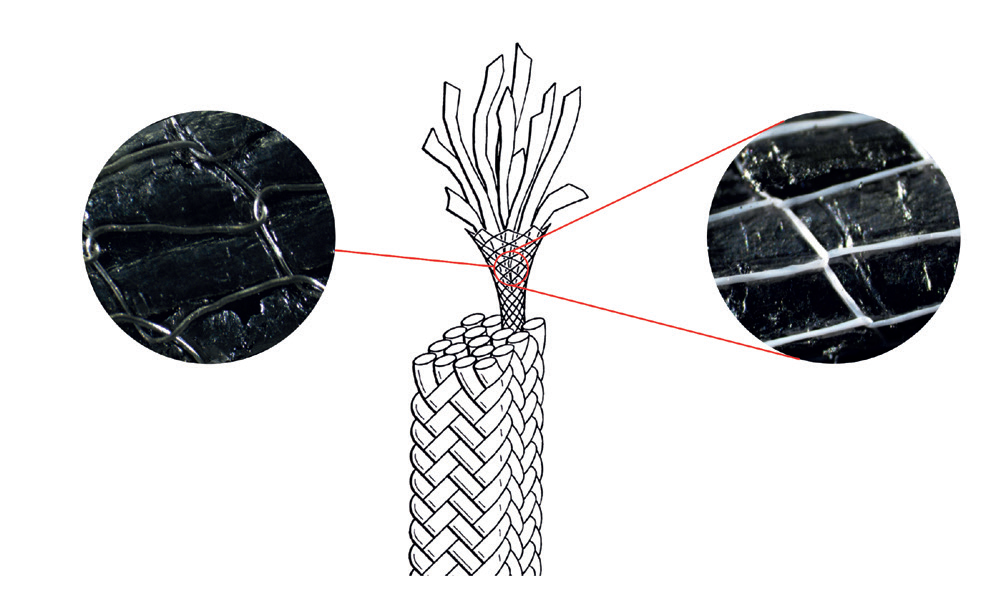
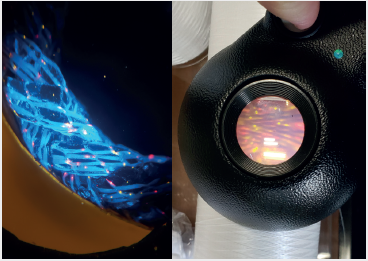
Now a Compliance Tool
As fugitive emission compliance requirements continue to evolve, one glaring concern is the lack of long-term traceability. The solution has typically relied on proper tagging of valves and maintenance of documentation. Never before has the solution been built right into the product.Manual tagging can be problematic for several reasons and leaves a large margin for human error. Moreover, in harsh industrial environments tags can become damaged and dislodged and lost. Lastly, the type, style, and manufacturer of an installed packing is not discernable simply by looking at the product. Teadit® TAGS™ offer a solution to all those concerns by embedding the identification tagging into the packing itself with this patented technology. “Teadit’s packing provides the ability to easily prove that a valve is compliant, and ensures low emission performance requirements,” said Bronson Pate, TRICORD Consulting, who has used these products first-hand.
Reduced emissions can be realized and declared by implementing an LDAR Program with best available Certified Low-Leak Technology (CLLT). Teadit’s product is proven to outperform the EPA’s sealing requirements. Going from pre- LDAR technology to today’s technology (100ppm) drastically reduces emissions and costs to any site. However, with 2848, this can be taken even further, with results of 2ppm, creating tons of GHGs saved per year and thousands of dollars in fees eliminated. Fees from the EPA have recently increased to $900 USD per ton, and will be increasing to $1,500 USD after two years.
Additionally, Teadit® TAGS™ can be traceable regardless of operational conditions. This is an outstanding innovation for environments with chemically aggressive fluids, abrasion, high pressures, and even elevated temperatures.
The products’ high chemical resistance was assessed in laboratory experiments consisting of two uniquely different environments for a period of three months each. In the first experiment, the packing was exposed to a 98% concentration solution of sulfuric acid (H2SO4). The second experiment was conducted in a 50% concentration solution of sodium hydroxide (NaOH). In both scenarios, the packings maintained their structure and were still identifiable.
Its great resistance to high temperatures was also verified in laboratory experiments. Samples were exposed to 650°C, for 4 hours and the identification Teadit® TAGS™ remained intact. Regardless of the operating environment, Teadit® TAGS™ can handle it.

TEADIT’S PACKING PROVIDES THE ABILITY TO EASILY PROVE THAT A VALVE IS COMPLIANT, AND ENSURES LOW EMISSION PERFORMANCE REQUIREMENTS.” – BRONSON PATE, TRICORD CONSULTING.
Very Flexible Solution
Unlike most low emissions packings, the lack of metallic reinforcement makes this innovative product a highly adaptable solution. Its soft exterior is not only suitable for control and isolating valves, but also makes it a good fit for pumps and other rotating equipment.The performance of Style 2848 was evaluated on a test rig based on EN 16752:2014. The test consisted of subjecting the packing to water pressurized at 6 bar for 100 hours with a shaft speed of 1750 rpm (6.4 m/s). The fluid leakage was collected and measured separately for the shaft side and the stuffing box side.
Looking to the Future
As shown, the leakage was stabilized over the test to a very low value. This result, along with the results of the previously mentioned test, highlights the potential of Style 2848 as a universal, high-quality packing that combines low-emission technology with the versatility required for the wide range of equipment and applications that currently rely on compression packing sealing in the industrial sector. Its traceability pathway likewise gives it a unique advantage for the user.