Applying the correct bolt torque in a bolted flange joint assembly procedure to achieve a leak-free connection can be a complex endeavor. There are a myriad of variables that need to considered and controlled to be successful.
Though experts largely feel extremely confident in the ability to control the specification of the proper materials and components, utilize the proper tools, and calculate the correct torque values; one critical and often overlooked variable still looms large. That wildcard is the technical expertise of the person, or persons, doing the actual flange bolt up. Even the most technologically advanced tools are of little value if not in capable hands.
Gasket manufacturers and suppliers, end-users, industry organizations like ASME, and others, have developed courses and training programs on flange assembly best practices. These courses provide information about the interaction between flanges, bolts, and gaskets, proper inspection and installation procedures, and applicable regulations. Many agree that the most effective aspects of any training program related to flange joint assembly involves the practical hands-on elements. Assembly demonstration rigs require a significant initial investment and, due to their bulky nature, are difficult and costly to transport for on-site training. Moreover, limitations on travel and in-person meetings related to the global pandemic have forced many companies to consider alternative virtual meeting/training methodologies. This is a legitimate obstacle for current bolted flange joint training. This brings the consideration of virtual flange assembly training programs.
A Revolutionary Training Tool
The Virtual Gasket Assembly (VGA) application has been developed to simulate the behavior of a gasketed flange joint in real-time. This instructional tool is designed to allow for the complete experience of assembling a flange joint utilizing a variety of different gasket types and employing different tools to provide comparative reference points for assemblers. The central idea behind this tool is to assist the trainee assembler with understanding the necessary procedure for achieving a reliable installation, while at the same time modelling how each tightening step affects the clamping force generated by the bolts, and in-turn the sealing stresses generated upon the gasket. As a bolt torque is applied, the program models the mechanical interactions, showing the resulting loads/stresses after tightening and the elastic interactions between the various components.Simultaneously, the gasket stress can be displayed graphically within the program showing the effect of every performed action on its distribution across the entirety of the sealing surface. This provides immediate feedback to the user allowing them to visually see how the mode of load application to the gasket itself effects overall sealability. For example, what happens if even one bolt is not loaded properly in an eight bolt flange? The program allows for users to investigate such scenarios.
How Does it Work?
Figure 1 shows an example of the user interface and some of the various features and customizations that are available. The gasket type, internal pressure, assembly pattern, fastener yield strength, lubrication nut factor, and applied torque can all be configured to model different real world assembly scenarios.As a training tool, the application also includes a testing function that allows for an evaluation of the assembler’s performance based on a 100 point scoring system, that compares the applied installation procedure execution to that of the ASME PCC-1 Guidelines for Pressure Boundary Bolted Flange Joint Assembly recommended best practices. In the evaluation mode, the training ends prematurely if the trainee fails to properly install the gasket by performing a faulty function such as crushing the gasket or yielding the bolts. This provides immediate feedback to the assembler to further accelerate the learning process.
The obvious question is, how does a virtual experience stack up against real world bolted joint assemblies? Such concerns are valid, as the goal of any practical training is to provide an environment that is as close as possible to its real-world counterpart. The VGA models and the calculations behind them are based on experimentally derived data and empirical equations, providing an experience strongly based on real gasket applications and for the most part identical to that of traditional hands-on flange joint assembly training rigs. Hence, it provides a safe environment for training while maintaining the fidelity of a real installation.
The simulator can accurately model a wide range of gasket types, including compressed fiber gaskets, spiral wound gaskets, camprofile gaskets, and expanded, restructured and skived PTFE gaskets. It has embedded within it material properties derived from well-established industry standard testing protocols such as, maximum assembly gasket stress (Sgmax), minimum gasket seating stress (Sgmin-s), and minimum gasket stress to seal in-service (Sgmin-o), allowing the user to simulate media pressurization like those experienced at system start-up and during operation.
The assembler can choose from four types of tightening tools to simulate the usual options available in the field. Additionally, by pairing the VGA with a torque measuring tool, a fully interactive training is possible. This allows the assembler to actually use a torque wrench to apply the desired load, as shown in Figure 2.
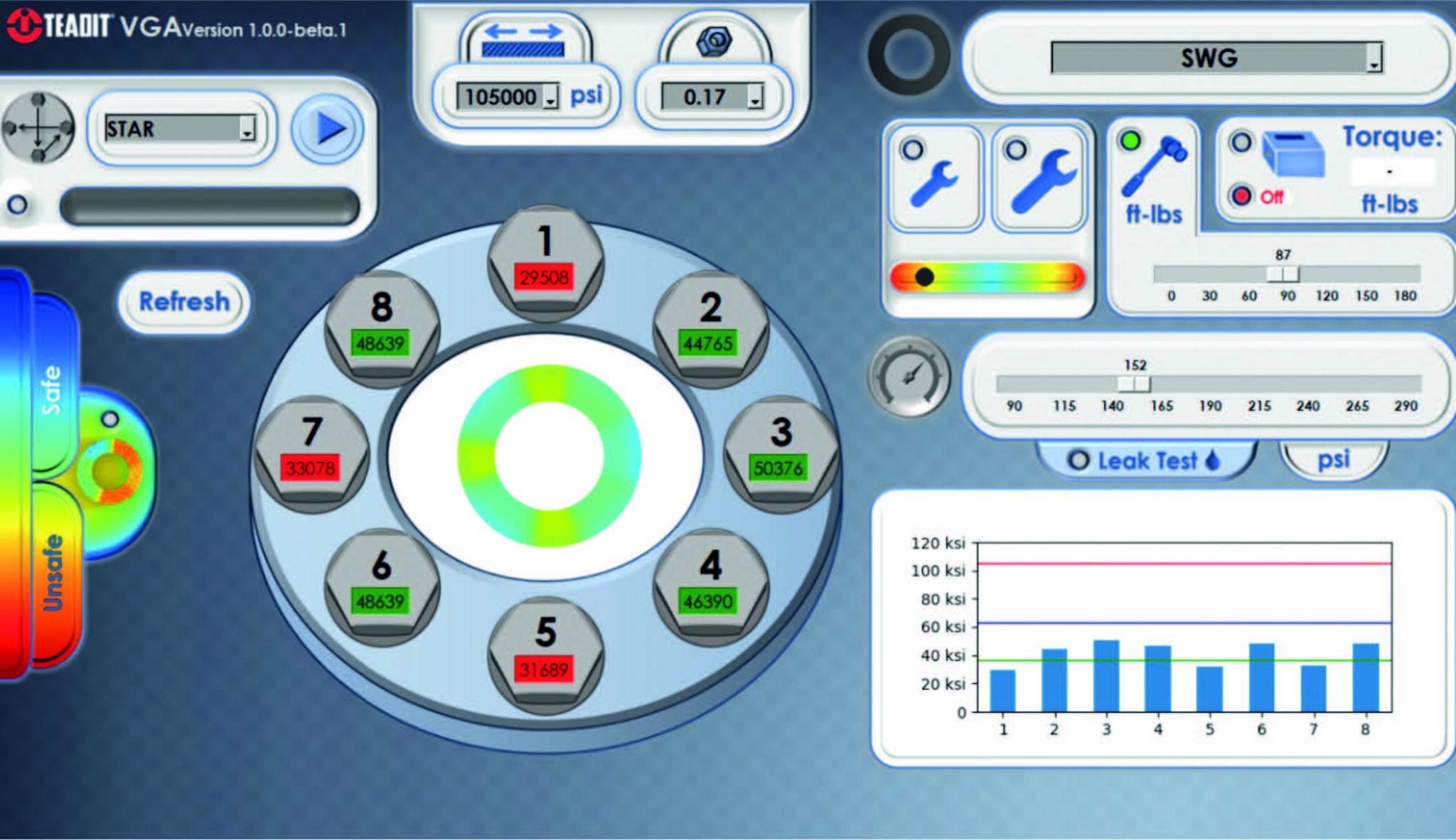
The Importance Of Flange Tightening
Proper piping system maintenance is essential to ensure the integrity of the process and its components, and is paramount for maintaining plant safety. Research has shown that the overwhelming majority of flange joint failures are related to poor or incorrect assembly practices. These failures lead to overall lost revenue in the form of downtime, maintenance expenses, and general system inefficiencies and waste. This, coupled with the inherent safety and environmental costs related to flange leaks makes prioritizing flange assembly training in everyone’s best interest.What we know most assuredly is that in real world sealing applications, flange joint integrity heavily relies on the harmonization of each component: gasket, bolts, and flanges. The entire joint is only as strong or reliable as its weakest link. Specifying the correct components for the application is in and of itself a daunting enough task. Yet, even if we are right on point with our specifications, poor installation practices can and will undermine all of that front-end work. The key to proper flange joint assembly is controlling the stress variations in the various components. This means that the flanges must be brought together slowly and evenly. The correct bolt tightening pattern and load play a crucial role.
Benefits Of VGA Training
The VGA addresses the guidelines for good installation procedures with targeted values, making it an ideal training tool for improving joint integrity. It allows for:• visualization of the various stresses in the joint, which is translated to an intuitive interface that facilitates learning;
• simulations of media pressurization and gasket blow-out;
• personnel to be trained in a safe environment with no safety risk and/or risk to equipment;
• and instruction to be given remotely without the need for on-site or in-person interaction.
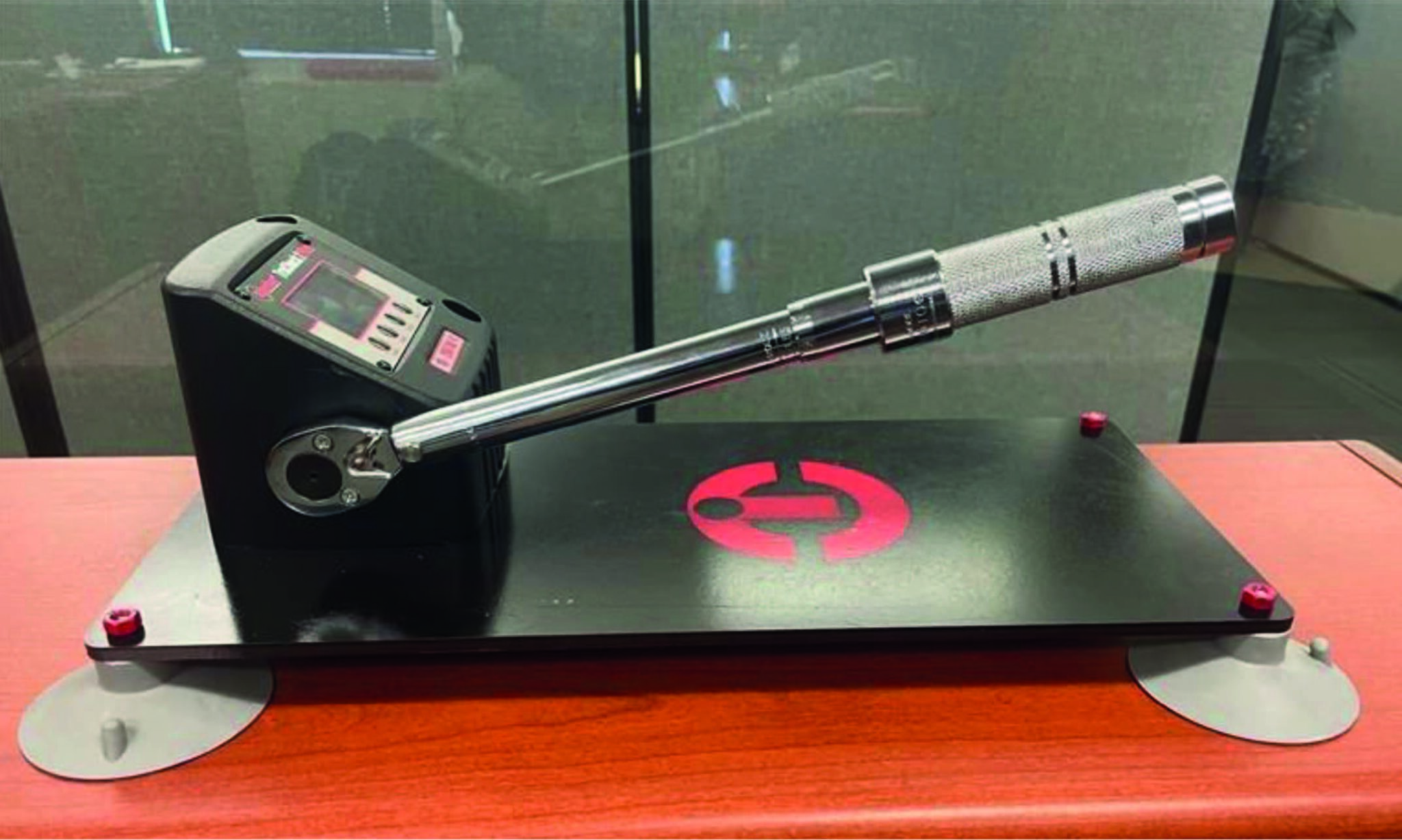
Looking to the Future
Information access is a vital part of modern life for most people. Smartphones, tablets, and other internet-enabled devices are always within arm’s reach. They provide access to, and the transmission of, information we rely on and have become necessary tools for everyday life.In teaching and training, applications have become a powerful tool for teachers and students alike. They can provide a tailored experience for each user, provide easy access to content, and enable asynchronous interactions between students and teachers; making learning easier than ever without concerns over schedules or proximity. Applications provide greater access to opportunities to learn and in many ways can be even more efficient than traditional learning environments due to their high level of customization.