Spiral wound gaskets are one of the most respected and recognizable gaskets in the industry. Since its inception in 1912, it has become a staple in a variety of services, from nuclear powered aircraft carriers, to petrochemical plants. Many manufacturers currently fabricate their own spiral wound gaskets, with the majority specifying ASME B16.20 guidelines.
However, some have deviated from the standard to create a design that is marketed as a ‘low-stress’ alternative.
Background
Spiral wound gaskets are common commodities used in piping systems across several industries, and maintenance and reliability staff are constantly on the lookout for products offering the promise of better performance. The ‘low-stress’ spiral wound gaskets are marketed as an alternative to standard spiral wound gaskets, requiring less torque to seat the gasket.This makes for an enticing offering, since the most common cause of bolted joint failures is a lack of load. The problem with this terminology, is that it is a very loose designation for gaskets that can, and often do, have a range of differences, making it difficult to judge the gaskets objectively.
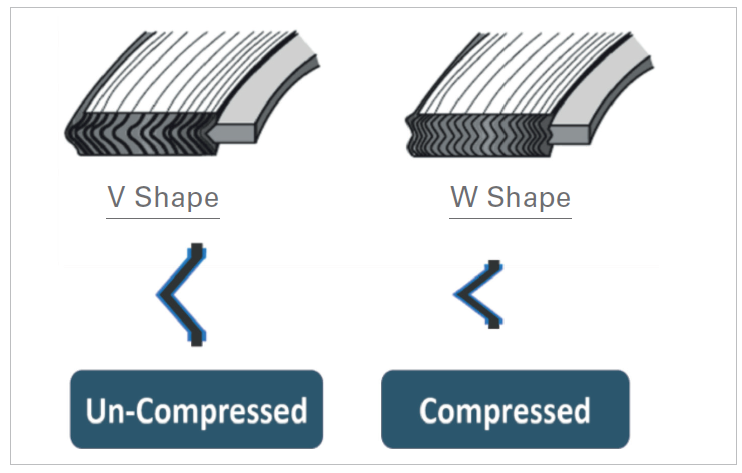
Many manufacturers of spiral wound gaskets have made subtle changes over the years to try to differentiate themselves, and the ‘low-stress’ technology has become a common theme throughout the market. Multiple types of plants use these designs in their piping systems in specialty applications, or even as replacements for ASME B16.20 standard spiral wound gaskets. In general, ‘low-stress’ spiral wound gaskets have various design elements, from additional graphite in the filler, to a stress relief anti-buckling design, which are all marketed as requiring less initial preload to seat. While no one can argue that it is possible to make spiral wound gaskets more compressible, questions remain about the proposed benefits of ‘low-stress’ technology and its effectiveness in providing a reliable seal. In other words, is a softer, more compressible sealing element a good thing for a spiral wound gasket?
Low-Stress Meaning
The designation of ‘low-stress’ spiral wound gaskets refers to those that have a lower density (i.e. softer) winding, which is created by utilizing a thicker filler strip, and less tension on the winding metal during manufacturing. This produces a softer, more loosely wound gasket with fewer metallic wraps, enabling the sealing element to compress under a lower load. Standard spiral wound gaskets should have a higher density, stiffer winding constructed with thinner strips of soft filler, and are wound tighter during the forming process. This ensures a gasket with higher filler density, and more metallic wraps, as shown in Figure 4. Testing has shown that a gasket without this higher density winding cannot meet the current compressibility and sealability requirements of ASME B16.20, hence the reason they cannot be stamped as being manufactured per the standard.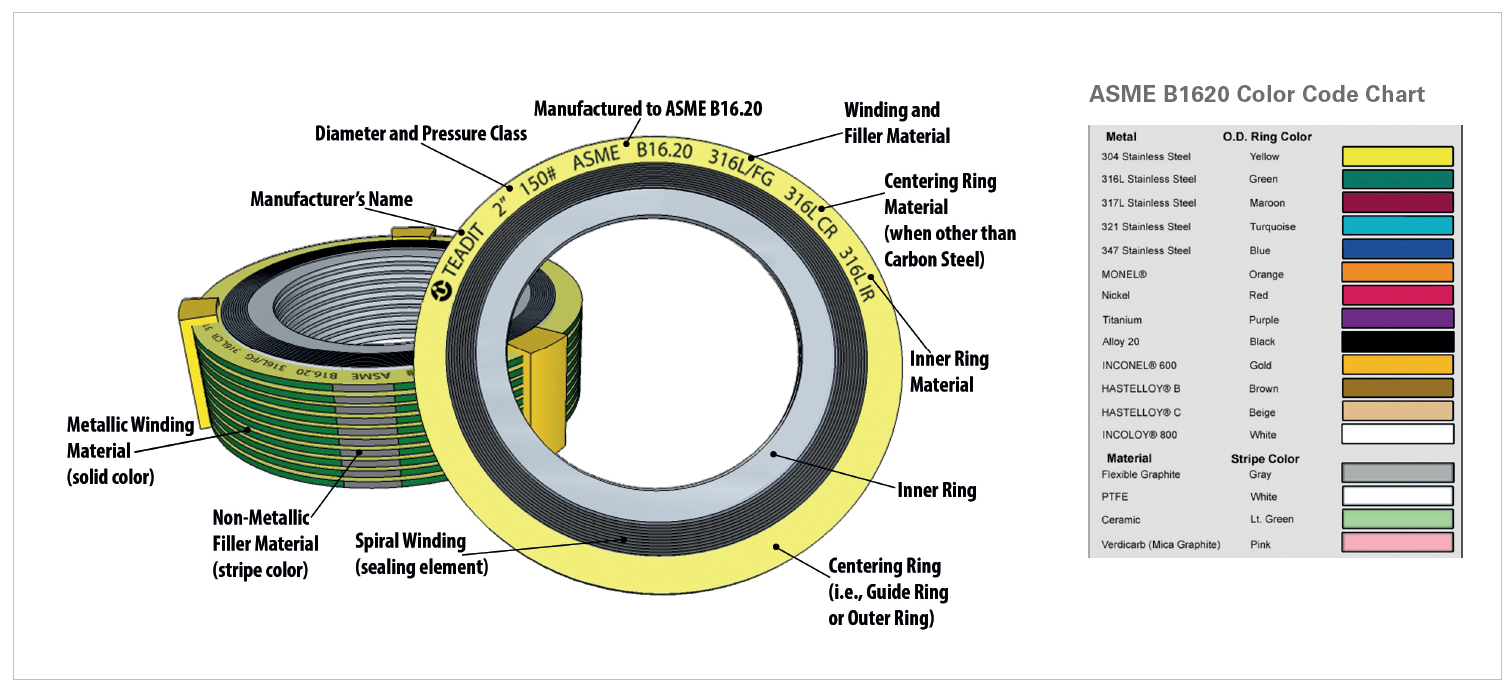
Spiral Wound Construction
For the most part, the spiral wound has undergone only subtle changes since its initial introduction over 100 years ago, with the overall concept remaining the same. This fact highlights the versatility and effectiveness of the gasket in general. It can withstand high temperatures and pressures, and can be used with a variety of chemicals: the manufacture can change the materials of construction to enhance compatibility with the process.A standard spiral wound gasket has three major components: a solid metal outer ring, a solid metal inner ring, and the wound sealing element. The sealing element is formed by using alternating plies of metal wire and a soft filler material, which are wound together on a mandrel into a gasket shape of the desired size. During the process, the flat winding metal strip is formed into a “V”, or chevron shape, as depicted in Figure 1. This allows the windings to flex like a spring under load. Common filler materials are flexible graphite and polytetrafluoroethylene (PTFE), though other options are readily available for specialty services. The materials and methods of construction will vary based on the operating conditions, such as temperature and pressure, of the service. These materials must also be chemically compatible with the process media. Additionally, the density of the winding is a key factor in determining how the gasket will respond and perform under load.
The outer ring serves as a centering ring, or guide ring, to ensure that the sealing element is properly located between the flanges; while the inner ring, a comparatively recent addition to the design, serves to prevent the winding’s natural proclivity to radially buckle at the inside diameter. However, neither of these elements are designed or intended to assist in the functional sealing of the gasket. That task falls solely on the winding element itself. ASME B16.20 also specifies the identification markings required to be printed on spiral wound gaskets.
It is important to recognize that only gas kets that meet all of the requirements of ASME B16.20 (construction, dimensional, compressibility, and sealability) should be stamped with this designation. Other designations, such as the manufacturer name, size, pressure class of the gasket, and materials of construction will commonly appear on all spiral wound gaskets. It is also important to know that prior to 2008, inner rings on spiral wound gaskets were not considered the standard. Industry feedback was consistent that buckling of the windings on spiral wound gaskets with only outer rings was a common issue. One solution was to machine relief ports into the outer ring to allow for outward expansion of the winding element. However, more commonly, inner rings were used. In May 2008, ASME B16.20 standardized the use of inner rings on spiral wound gaskets.
Additionally, the challenge with the ‘low-stress’ nomenclature is that it lacks a governing standard to ensure consistency across manufacturers. Some might choose to offer styles that have low-density windings, while others may offer styles that provide stress relief ports. In essence, ‘low-stress’ is generally very hard to define. What is the end user receiving? Is it referring to low bolt stress, or low gasket stress? How much is ‘low’? Is it an overall gasket stress value, such as 5,000 psi? Is it dependent on pressure class? How are the ‘low-stress’ gaskets constructed? What are the winding element dimensions? What variety can be expected between manufacturers? What are the manufacturing and design tolerances? And most importantly, how does a ‘low stress’ design impact the sealing performance and reliability?
One common criticism of low stress designs is that the flange will go metal-to-metal with the outer guide ring. This in turn results in an unloading effect on the intended sealing element of the gasket (the winding). Metal-to-metal sealing can be achieved in flange and gasket combinations that are designed for it. However, this is not the case for standard pipe flanges with spiral wounds, as they are not intended for metal to metal sealing. In fact, testing has shown that it is the paints and coatings on the outer guide rings that effects the seal (at least, temporarily). Why would one pay for a spiral wound gasket that ends up sealing on a painted metal outer ring when another option exists? It seems like a funny scenario, but in fact is a common occurrence. What inherent dangers lay dormant in plants just waiting for the right circumstances to let loose a significant event?
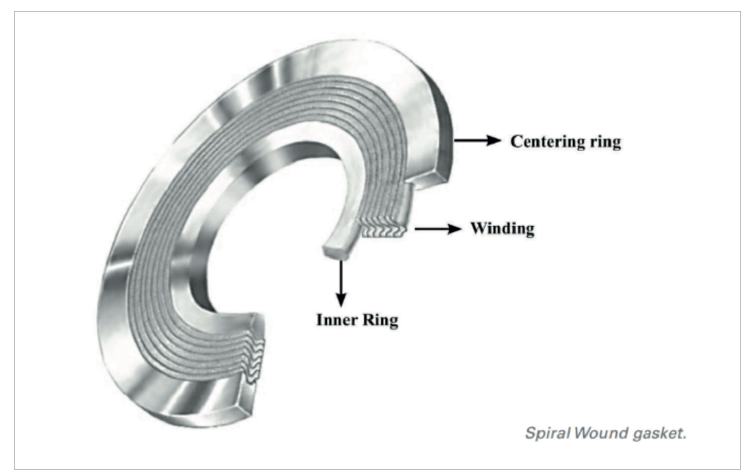
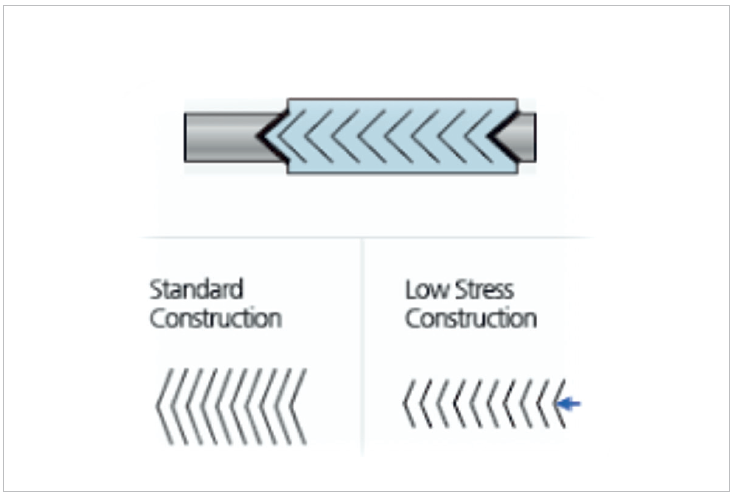
Specification Changes
The previous ASME B16.20, 2012 revision contained a provision on construction. This provision has since been updated, per the ASME B.16.20, 2017 revision to include a maximum compression requirement, as well as the gasket stress required per pressure class. Additionally, the 2017 revision removed the former 3.2.6 revision relating to gasket compression and replaced this with performance testing requirements.The ASME B16.20, 2017 revision’s removal of 3.2.6 has subsequently removed an overall benchmark of what can be defined as a ‘low-stress’ spiral wound gasket. Simply stating that a spiral wound gasket has a lower density winding does not set the standard of what a ‘low-stress’ spiral wound gasket is. Is it a spiral wound gasket that seals at 34 MPA (5,000 psi), 36 MPA (5,200 psi), or 41 MPA (6,000 psi)? In addition, ASME recommends spiral wound gaskets to come standard with inner rings. The low-stress characteristics of the spiral wound depends on several factors, which include the density of the winding, the filler material, and often the absence of an inner ring.
As the ASME B16 Committee G adopted and released the B16.20, 2017 revision the PIP (Process Industry Practices), this started the process of removing low-stress terminology from piping specifications. There was again uncertainty in what constituted ‘low-stress’ in these PIP piping specifications. When the ASME B16.20, 2017 revision incorporated a leakage test based on gasket stress, the PIP accepted the initiative to remove ‘low-stress’ from all piping specifications. As of 2021, this task has been completed and there is no further industry-standard reference to ‘low-stress’ spiral wound gaskets.
Some manufacturers defined their ‘low-stress’ gaskets as being able to seal at a lower stress value, however, finding objective proof of the gaskets’ sealability is difficult to prove, especially if some of the spiral wound components are not constructed to the ASME B16.20 standards. ASME B16.20 provides guidance on the maximum compressed thickness requirement, and this is no longer left up to interpretation. ASME B16.20 provides a performance testing requirement, in addition to the dimensional requirements, which provides further clarification on the parameters of a properly constructed and tested ASME B16.20 spiral wound gasket. If the ASME B16.20 standard for spiral wound gaskets has moved to a controlled density, more robust winding, that at minimum calls into question the validity and effectiveness of ‘low stress’ gaskets.
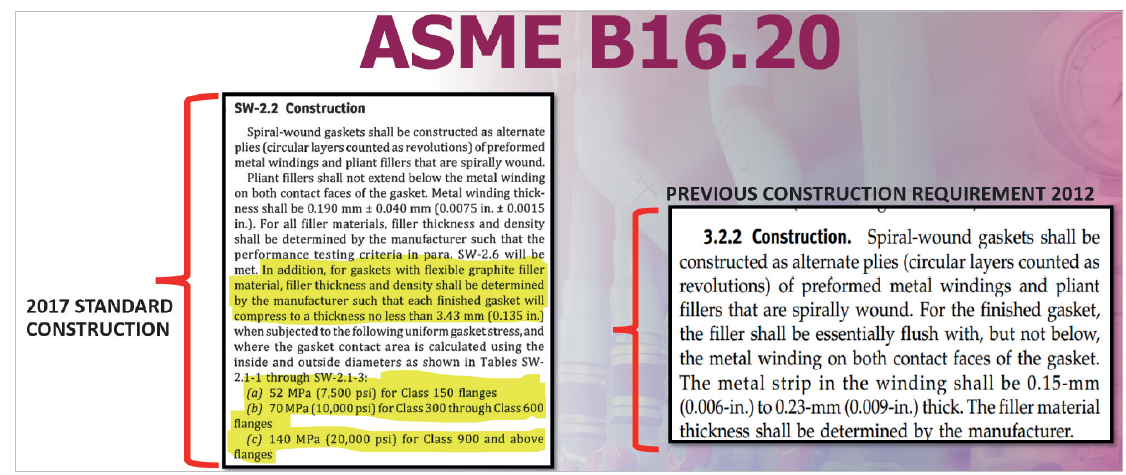
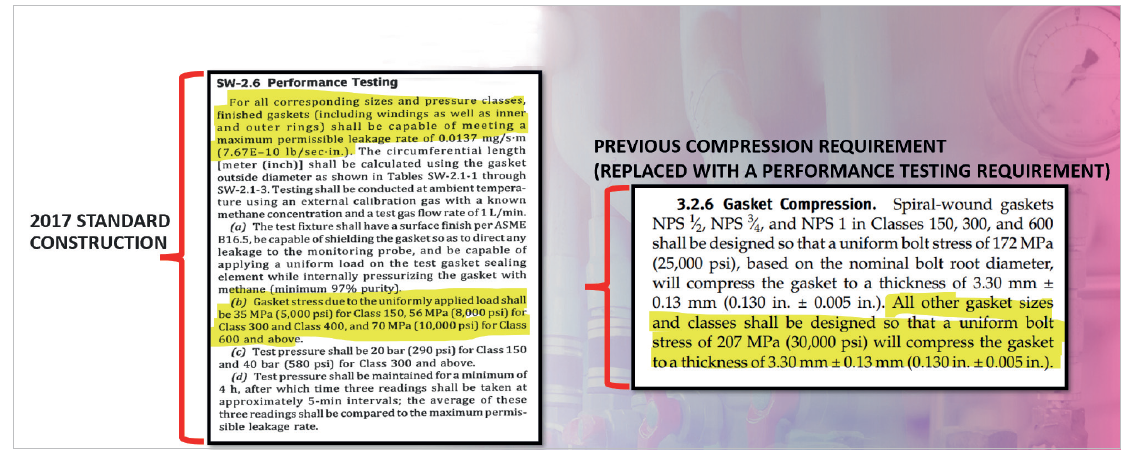
Conclusion
Low-stress spiral wound gaskets, and the terminology, prior to the ASME B16.20, 2017 revision, perhaps had a place because the specifications where not as stringent and left room for manufacturers to approach spiral wound gaskets from multiple angles. This resulted in a wide variety of spiral wound gaskets, ‘low-stress’ included, flooding the marketplace, and ultimately causing confusion among end users. Now that the ASME B16.20, 2017 revision exists, the industry has spoken about what constitutes an effective and desirable spiral wound gasket. This was intended to provided consistency in spiral wound gasket performance, regardless of manufacturer, making for safer and more reliable connections across the industry.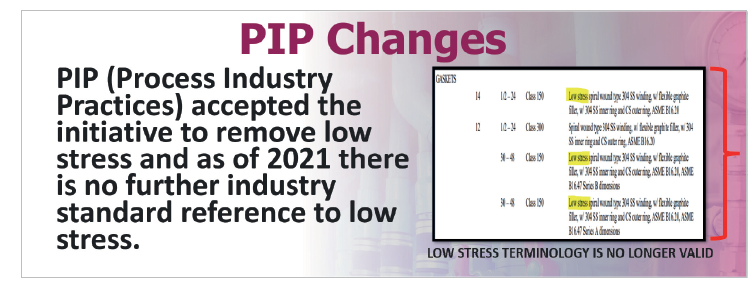