The evolution of the spiral wound gasket, and its standards, is indicative of the ever-advancing potential for increased efficiency and asset reliability in the industrial sector. After a long history of innovation, spiral wound gaskets have proven to be essential, not only from a total cost of ownership perspective but also for the ongoing endeavor to minimize emissions in the pursuit of a net zero economy. Ensuring that these assets are applied correctly can take the industry one step closer to achieving a safer and greener tomorrow.
Need for Efficiency
In 1867, George Babcock and Steven Wilcox patented the first steam-generating boiler. As boiler technology advanced, it became apparent that the key to increasing efficiency and productivity was developing effective seals to minimize energy loss and maximize steam generation. The idea of gaskets and seals was not novel, but the need for more effective gaskets led to the development of new and better materials.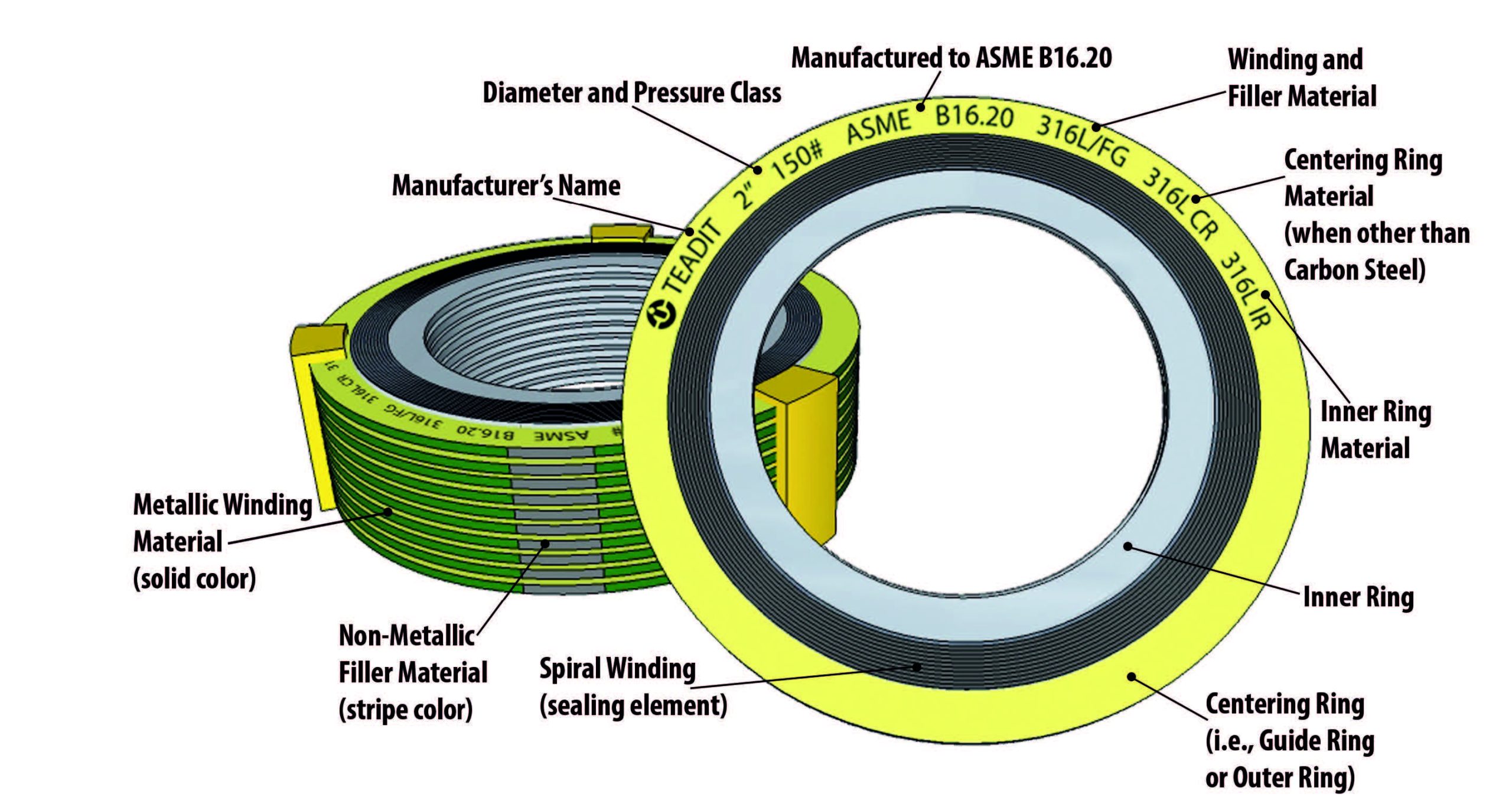
In 1912, the spiral wound gasket was developed by alternating plies of metal with fiber filler to meet increasing pressure resistance demands. While conceptually similar, early spiral wound gaskets were quite different from the ones in use today.
Progressive History
In the first two decades after their introduction, the structure of spiral wound gaskets had already begun to change significantly. In 1930, patents for reinforcing both the inside and outside diameters of the gasket with additional metal wraps, and early designs for guide rings, appeared. These designs evolved to the creation of the conventional metal outer guide ring we see today.In 1941, designs for the use of ‘soft metal’ fillers were introduced for high-pressure applications, and 1942 saw early designs for an inner ring to reinforce the gasket against radial buckling. Then, in the 1960s, new materials such as PTFE and exfoliated graphite were introduced as alternative filler materials.
It was not, however, just spiral wound gasket technology that was evolving. As boiler technology advanced in the early 19th century, the need for oversight and standardization also grew. Catastrophic pressure vessel failures were common, which posed a serious risk to workers and public safety. Many aspects of modern standards such as ASME B16.5 and B16.47 (pipe flanges), ASME B31.3 (process piping), and ASME Boiler and Pressure Vessel Code Section VIII (design and construction of pressure vessels) were first developed and codified at this time.
The Rise of Standards
As standards developed for boilers and pressure vessels, additional considerations were made for the gaskets that were so integral to their efficient and effective operation. In the late 1930s and through the 1940s, the American Standards Association (ASA) worked to incorporate the existing American Petroleum Institute (API) benchmarks into their standards, culminating in the approval of a new standard, ASA B16.20.By its final edition in 1988, the API standard had expanded to include spiral wound and jacketed gaskets, along with ring joints. In January 1993, the new ASME B16.20 Metallic Gaskets for Pipe Flanges standard was first introduced and in 1998, it was approved by ANSI as a national standard. Since then, the standard has continued to evolve.
Research-based Evolution
The earliest version of the B16.20 standard was a dimensional standard and gave little to no direction on how the gaskets were to be constructed. This meant that individual manufacturers were on their own to determine how the winding element (the primary seal of a spiral wound gasket) was to be made to effectively seal. This led to vast differences in winding performance across the industry.For most of its history, a compressibility requirement was the only ‘performance’ consideration within the B16.20 standard. However, the standard’s wording and methodology essentially ensured that the gasket sealing element would compress to the outer guide ring when subject to a prescribed load based on the gasket size and pressure class.
In 2017, Jose Veiga, former Global Technical Director of Teadit, and David Reeves, the former S.M.E. of bolting and sealing for Chevron, presented their research paper titled “ASME B16.20 Spiral Wound Gaskets Performance Testing” (PVP2017-65371) at the ASME PVP Conference. Their research showed that by carefully controlling the winding density (the ratio of metal to filler) across all sizes and pressure classes, spiral wound gaskets could achieve and maintain a tight and reliable seal. Producing a high-density winding stood in contrast to much of the day’s winding methodology that produced ‘soft windings’ which allowed for over-compression, effectively eliminating the winding element as the primary seal, and transferring the sealing load to the outer guide ring (a non-sealing element).
A more Technical Look
As Figure 1 demonstrates, the default components include a wound sealing element consisting of alternating plies of a metal and a soft filler, a metal outer ring (sometimes referred to as a guide ring or a centering ring), and a metal inner ring. The nominal sealing element thickness is 0.175” while both the inner and outer ring are 0.125” thick. For general service applications, the winding is typically stainless steel, with flexible graphite filler.
The winding density is a fundamental parameter for spiral wound gaskets. Low winding density correlates to reduced sealing performance, as compared to higher-density windings.
While the compression test remains in ASME B16.20, it has been altered such that the ‘finished gasket will compress to a thickness no less than 3.43 mm (0.135 in)’ when subjected to a uniform gasket stress.
The addition of the performance testing section in ASME B16.20-2017 has made a significant difference in how manufacturers design and produce spiral wound gaskets. This test has a leakage limit based on the circumferential length of the gasket’s outer diameter and requires multiple readings after a specified test pressure has been held for a minimum of four hours.
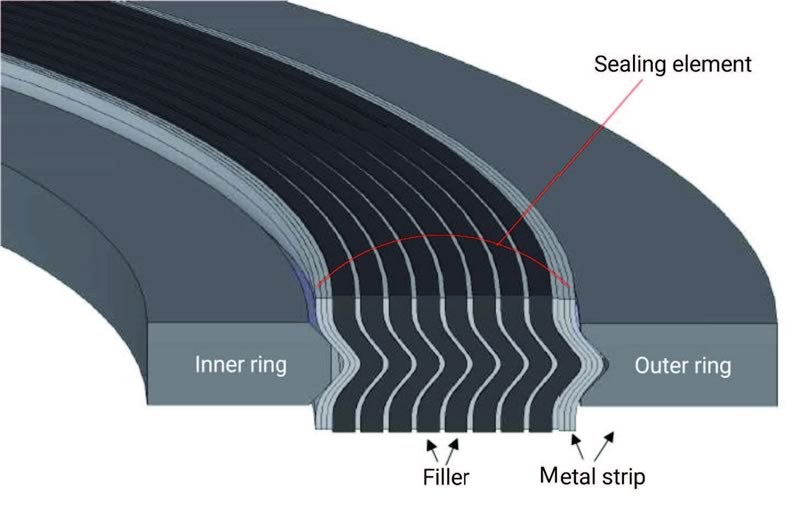
Today’s Standards
As a result of the research presented, a significant performance test was adopted into the 2017 edition of the ASME B16.20 standard; it was the first time for any gasket technology, that a performance requirement was incorporated within the standard.This performance standard was derived based on industry fugitive emissions requirements; standard ASME B16.20 spiral wounds, regardless of size or pressure classification by the standard, are designed to function as low-leak technology. Spiral wound gasket users can therefore request test data from manufacturers to prove their facilities are capable of meeting compliance thresholds for flange connectors with ASME B16.20 spiral wounds.
Looking Forward
As industry regulations push for a ‘net-zero’ carbon footprint, low-leak technologies that provide consistent emissions compliance benefits will inevitably see increased adoption among end users and will commonly be required as a part of EPA consent decrees.