Flexible graphite, a derivative of natural graphite, is often recognized as a material of choice for various industrial applications due to its exceptional properties. Its significance lies in its unique characteristics, which surpass many other materials in terms of temperature resistance, chemical compatibility, and sealing efficiency.
As effective sealing solutions are critical to reduce fugitive emissions, it is important to recognize the scope of the material’s capabilities, how it can be used, and the advantages of using it in critical sealing applications. By gaining a comprehensive understanding, industries can significantly enhance environmental compliance, improve operational efficiency, and increase safety.
What is Flexible Graphite?
Flexible graphite, also referred to as graphite foil, or expanded graphite, is produced from expandable flake graphite. The manufacturing process, known as exfoliation, begins by immersing flake graphite in acid, which weakens the interlayer bonds, making the graphite expandable. The expandable graphite is then subjected to intense heat, causing it to expand and curl, with an outer surface that tends to cling to other expanded graphite particles. Finally, it is pressed into the desired form to create flexible graphite.The material’s performance is closely linked to its carbon content, which ranges from 95% to 99%. Higher purity levels enhance the material’s thermal and chemical resistance and increase its strength. The typical density of flexible graphite products is roughly 1.0 g/cm³, providing a balance between flexibility and structural integrity.
Due to its structural properties, the material often performs optimally in critical applications and plays a key role in sealing effectiveness.
Key Properties
Flexible graphite’s popularity in sealing applications stems from four core characteristics: thermal stability, compressibility, chemical compatibility, and sealability.Thermal Stability
With a high tolerance for extreme temperatures (ranging from -200°C to 3,000°C in a non-oxidizing atmosphere), flexible graphite maintains its structural integrity and sealing performance under varied thermal conditions. This makes it ideal for applications involving prolonged exposure to high heat.Compressibility
Flexible graphite exhibits excellent compressibility, allowing it to conform to surface irregularities and create effective seals. This property is crucial for maintaining seal integrity under varying thermal conditions and mechanical stresses. It can also recover its shape after compression, which is crucial for maintaining long-term sealing performance under fluctuating pressures.Chemical Compatibility
The material resists a wide range of chemicals, further broadening its applicability in different industrial processes.Sealability
The non-porous nature of graphite ensures an excellent seal. Its sealing performance is often compared to that of PTFE (Polytetrafluoroethylene), with some scenarios favoring graphite for its slightly better performance. The dense structure of the material simultaneously provides excellent impermeability, effectively preventing gas leaks.These four characteristics make flexible graphite an increasingly common solution over alternative sealing products such as elastomers, PTFE, and metallic seals.
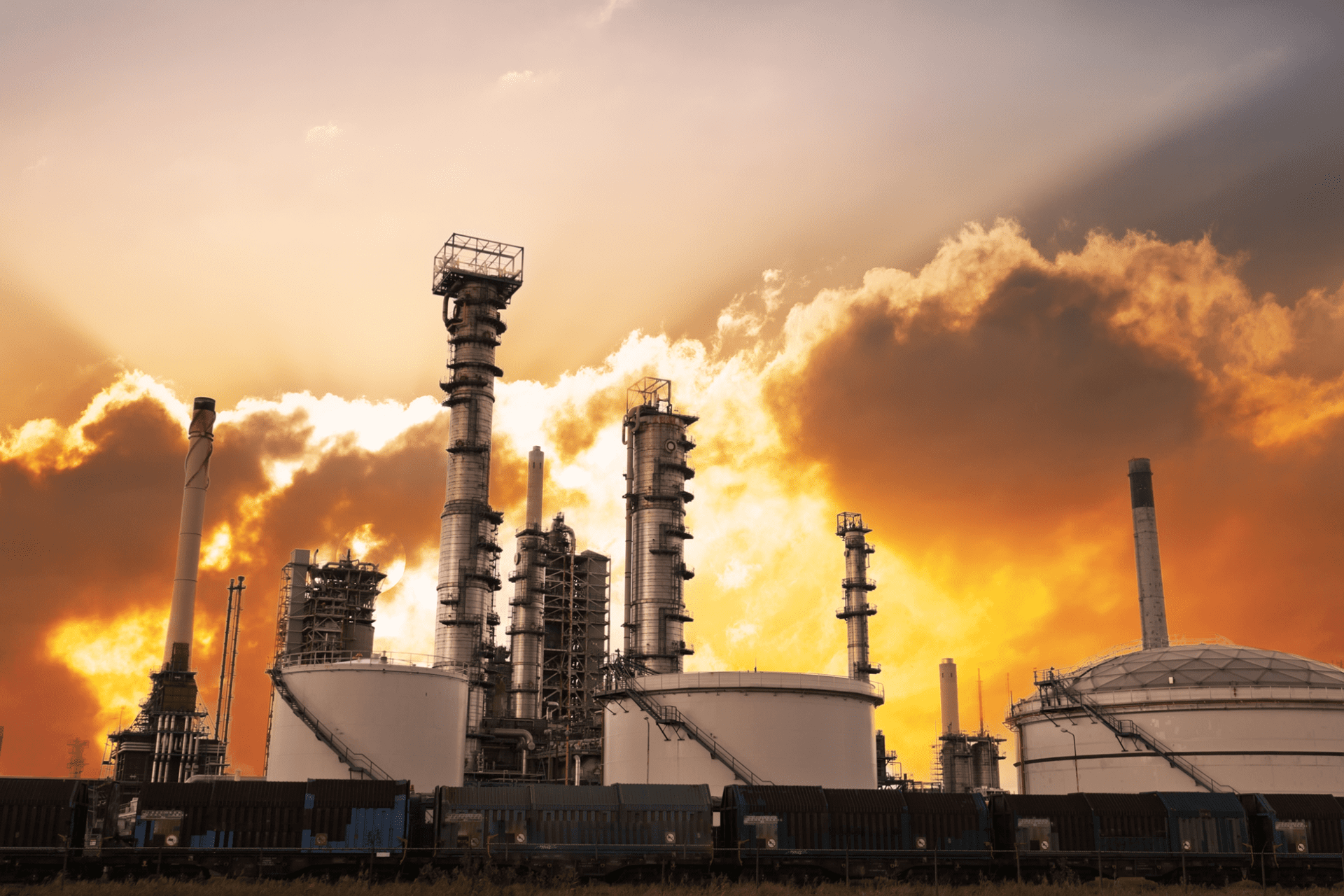
Examination of Sealing Materials
To best understand when flexible graphite is a highly versatile sealing material sealing material, it is beneficial to be aware of the applications and limitations of the primary sealing alternatives.Elastomers, such as EPDM, Nitrile, and Viton, are widely used in sealing applications but have notable limitations. They are highly sensitive to temperature, often degrading beyond 400°F (204°C), compromising their sealing integrity. Additionally, elastomers are vulnerable to chemical attacks that cause swelling, hardening, or cracking. Their permeability to gases and fluids is higher than that of flexible graphite, which increases fugitive emissions over time.
Thermoplastics, including PTFE (Teflon), are also used for seals and gaskets. While PTFE offers excellent chemical resistance, it deforms and degrades at temperatures above 500°F (260°C), compromising the seal. PTFE exhibits higher creep and stress relaxation under sustained load compared to flexible graphite, leading to seal failure. Moreover, PTFE has higher gas permeability compared to flexible graphite.
Metallic seals from stainless steel and other alloys provide high temperature and chemical resistance but have significant drawbacks. They lack the flexibility to conform to surface irregularities, often necessitating precise machining of flanges. Installation and maintenance of metallic seals can be challenging, as they may not effectively accommodate flange movement or thermal cycling. Additionally, metallic seals can be significantly more expensive due to higher material costs and the need for high precision in maintenance.
While each of these materials performs optimally in several scenarios, they experience limitations that flexible graphite can often overcome. The performance of flexible graphite does, however, vary slightly depending on its form.
Applications of Flexible Graphite
Flexible graphite products are typically categorized into three main types based on construction: homogeneous, graphite with metal inserts, and as a facing, or filler, for metallic gaskets such as spiral wound gaskets or camprofiles.Homogeneous sheets offer high flexibility but are considered fragile. These are pure graphite sheets without any inserts and are commonly used in applications where maximum purity and flexibility are required.
Graphite with metal inserts provides enhanced durability, making it suitable for higher-pressure applications. These sheets have a metal substrate, usually stainless steel, embedded within the graphite. The metal provides structural support, enhancing the sheet’s durability, and is often used in applications requiring higher mechanical strength and stability.
Spiral wound gaskets, which combine graphite with metal windings, offer robust sealing performance in high-pressure and high-temperature environments; the graphite filler ensures excellent sealability, while the metal windings provide mechanical strength and resilience against thermal expansion and contraction.
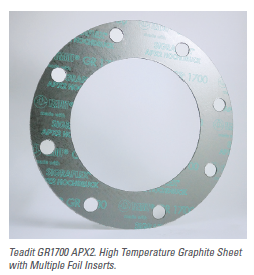
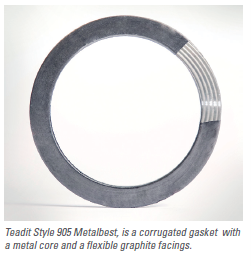
Benefits of Flexible Graphite
To illustrate the benefits of flexible graphite, it is best to examine the applications in which it is commonly used. For instance, in valve packing, especially for valves handling high-temperature and high-pressure fluids, flexible graphite packing prevents leaks through the valve stem by conforming to the stem and bonnet surfaces, ensuring a tight seal.In flange connections, flexible graphite gaskets provide an excellent seal between flanged surfaces, enduring harsh conditions without degrading and preventing leaks in critical piping system junctions.
Additionally, flexible graphite seals are crucial for withstanding high pressures and temperatures in pumps and compressors, ensuring no gases escape during the compression process. Finally, in heat exchangers, which operate under severe thermal and chemical conditions, flexible graphite gaskets provide reliable sealing, preventing leaks that could lead to fugitive emissions.
Final Thoughts
Flexible graphite’s resistance to extreme temperatures and chemical degradation ensures a durable seal under demanding conditions, significantly reducing the risk of fugitive emissions, and maintaining containment integrity over extended periods. Its versatility makes it suitable for a wide range of applications, from high-temperature environments in power plants to aggressive chemical processes in industrial settings, and its ability to adapt to different flange conditions and surface imperfections further enhances its utility.Despite a higher initial cost compared to some elastomers and its fragility, flexible graphite offers substantial long-term savings by reducing maintenance needs, downtime, and replacement frequency, leading to lower overall life-cycle costs.
The future of flexible graphite lies in improving its integration with other materials to enhance its mechanical properties and ease of installation. Innovations such as combining graphite with PTFE or other substrates could offer enhanced performance. Additionally, as environmental regulations tighten around materials like PTFE, the demand for graphite, with its minimal environmental impact, is likely to grow.