As regulatory standards evolve and industries shift towards low-emission technologies, many believe that the role of low-emission (LE) gaskets will become more substantial. Currently, no consent decrees reference LE gaskets, despite their crucial role in ensuring leak-free operations.
A precedent has already been set with low-leaking valves and packing technologies, both of which are referenced under the Environmental Protection Agency’s (EPA) stringent emission control requirements. As spiral wound gaskets are well positioned to follow suit, companies such as Teadit are offering high-performance gaskets that ensure compliance in low-emission applications.
What is a CD
Consent decrees (CD) are legally binding agreements between regulatory authorities such as the EPA, and organizations found in violation of laws. These decrees are typically used to resolve disputes or enforcement actions without going to trial. They require the organization to take specific corrective actions to comply with regulations, often including timelines, penalties for non-compliance, and mechanisms to ensure ongoing oversight.From a sustainability perspective, CDs promote compliance with laws like environmental regulations and expedite solutions in fugitive emission mitigation efforts.
Why Gaskets May Be Included in Future Consent Decrees
Gaskets are a critical component of sealing systems used in connectors, pipelines, and process equipment; however, they are yet to be incorporated into the Environmental Protection Agency’s (EPA) formal definition of “Certified Low-Leaking Technology.” Currently, the focus is on valves and packing, but as facilities continue to prioritize the reduction of fugitive emissions, gaskets are likely to come under increased regulatory scrutiny.Low-leaking valves and packing technologies must demonstrate their ability to maintain a leak rate below 100 parts per million (ppm) for five years, as per current EPA standards. Gaskets could soon face similar requirements, especially as the push for net-zero emissions accelerates. By integrating gaskets into these low-leakage requirements, companies will be able to further reduce emissions in ways that complement the existing standards for valves and packing.
The move toward low-emission gaskets will not only support ongoing environmental goals but will also help facilities avoid potential legal penalties under future consent decrees.
A Closer Look: Material Selection, Gasket Construction and Proper Assembly
Material selection is a critical component in the performance of SWGs. The filler material, typically graphite or PTFE, plays a significant role in enhancing the gasket’s sealing capabilities, as seen with Teadit’s 913M style gasket. Graphite is the most commonly used material due to its high thermal stability and excellent sealability, while PTFE (particularly expanded PTFE or ePTFE) offers excellent sealing performance in specific applications.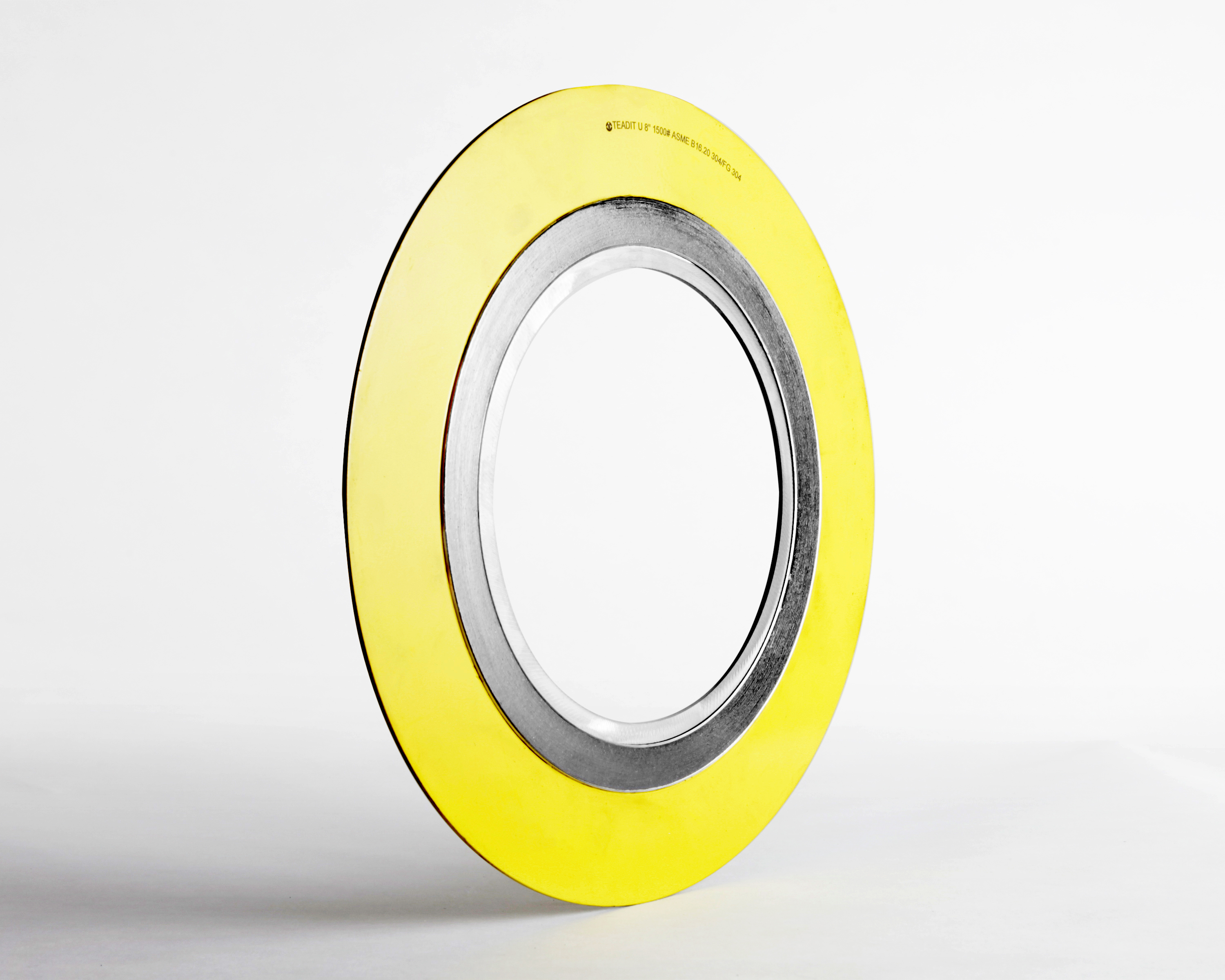
One often overlooked aspect of gasket performance is proper assembly. Even the best-designed gaskets will fail if not installed correctly. The ASME PCC-1 standard provides guidelines for properly installing gaskets, including recommendations on bolt tightening sequences and flange alignment practices, but not specific torque values. Ensuring these procedures are followed is essential for achieving the low-emission performance that SWGs can deliver. Teadit’s experts can provide specific torque values, as well as invaluable guidance and feedback during installation, helping to ensure that gaskets are properly fitted and aligned to optimize sealing performance. It can also provide onsite training for proper gasket installation and maintenance practices. This expertise helps prevent failures and maximizes the gasket’s contribution to emission control efforts.
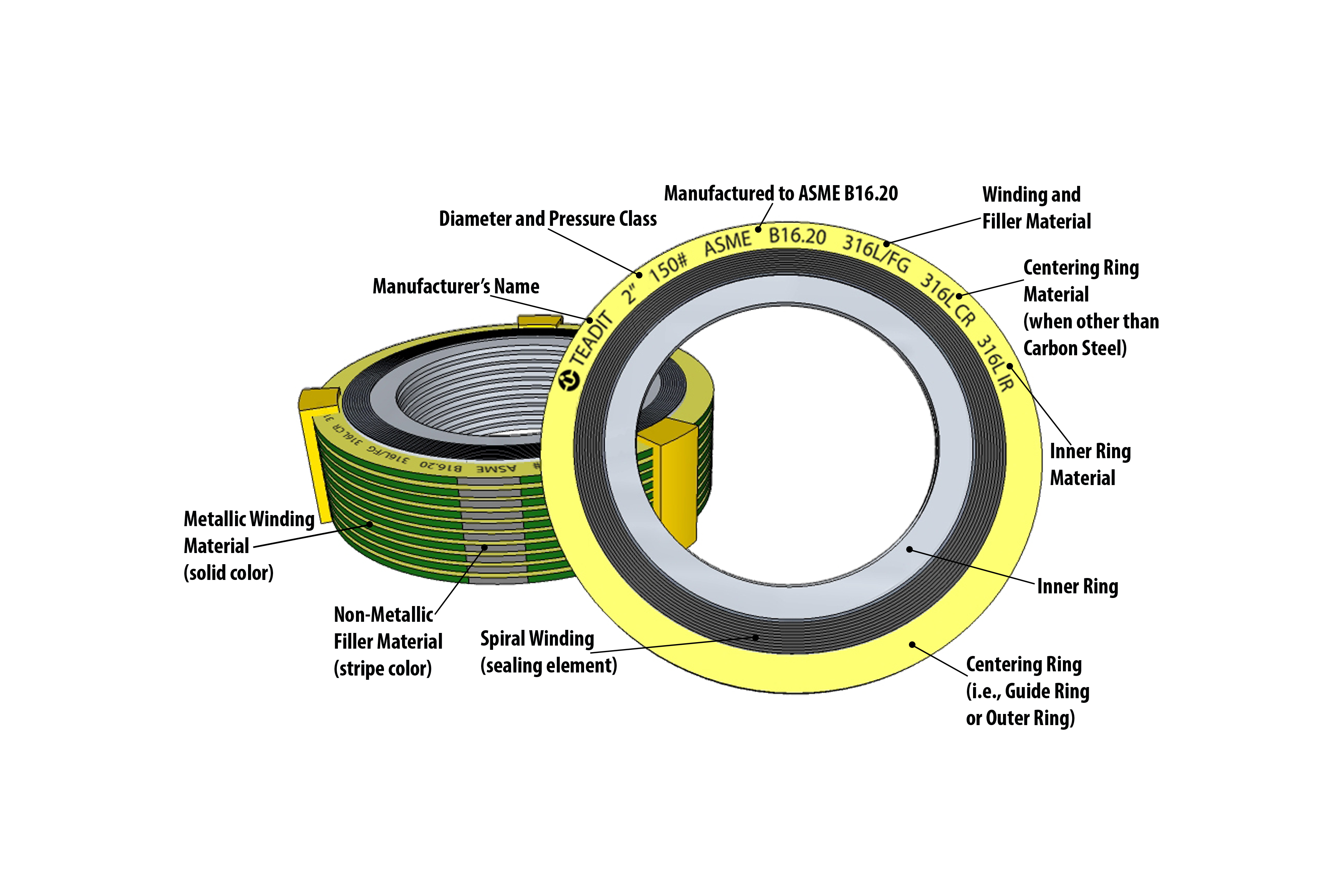
Spiral Wound Gaskets for Low-Emission Compliance
Spiral wound gaskets (SWG) are widely recognized for their sealing capabilities, particularly in applications requiring high compressive strength. These gaskets excel in preventing leakage due to their unique construction, which includes metal windings combined with filler materials such as graphite or PTFE.More specifically, spiral wound gaskets are constructed as alternate plies (circular layers counted as revolutions) of preformed metal windings and pliant fillers that are spirally wound.1 The combination of materials allows SWGs to conform well to imperfect flange surfaces, ensuring a tight seal even under extreme conditions like thermal cycling and pressure fluctuations. Not every SWG is created the same, however. For example, SWGs can vary in the density of metallic windings per unit length. Lower-density windings typically result in lower-cost gaskets, but higher-density windings offer significant advantages for sealability. Tests have demonstrated that gaskets with a greater number of metallic windings per unit length achieve lower leakage rates, even under high-stress conditions.

A crucial factor that makes Teadit’s 913M SWGs effective for low-emission applications is their alignment with the American Society of Mechanical Engineers (ASME) B16.20 standard, which serves as the primary testing protocol for gaskets in the U.S.. Although there is no universally accepted definition of a low-emission gasket, SWGs are one of the few gasket types rigorously tested for both compression and sealability, making them a reliable choice for industries aiming to reduce fugitive emissions. Compression testing ensures the gasket can withstand and maintain the necessary load to form a seal, while sealability testing verifies that the gasket can effectively prevent leakage under operating conditions.
While some manufacturers have already begun offering low-emission variants of their spiral wound gaskets, most do not guarantee they will meet the specific leakage limits, such as 100 or 500 parts per million (ppm). Interestingly, Teadit has taken the initiative to offer only low-emission gaskets as its standard product. This proactive approach eliminates the need for customers to choose between standard and low-emission options, aligning with a broader industry push toward sustainability and compliance.
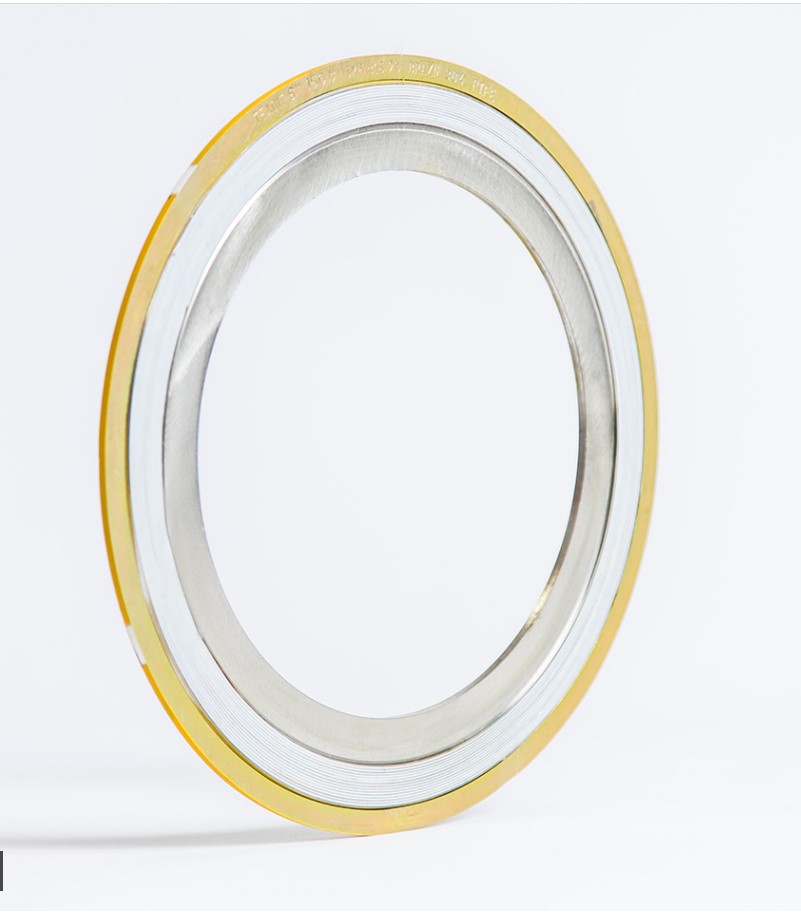
Challenges in Testing and Certification
Currently, there is no universally accepted definition of what constitutes a low-emission gasket. While ASME B16.20 sets a specific performance baseline for testing SWGs, the industry has long known how to achieve better performance. For instance, Teadit’s SWGs often surpass these standards, achieving leakage rates that are an order of magnitude lower than the ASME allowable limits.This gap in standardization presents both a challenge and an opportunity. As environmental regulations tighten, the industry may see the introduction of more stringent testing protocols for gaskets used in emission-sensitive applications.
When determining which manufacturers’ gaskets to use for low-emission SWGs, the purchaser should investigate the number of tests conducted and the size/class of gaskets tested to justify the LE designation. Future consent decrees could reference specific leakage thresholds, requiring gaskets to meet performance standards well beyond the current ASME requirements.
Upgrading to Low-Emission Gaskets
To transition to low-emission gaskets a site will be required to implement updated methodologies, such as sourcing the right technology and updating procurement practices to ensure compliance. Additionally, companies will need to phase out old inventory and provide adequate training for the correct installation of these gaskets. Ensuring that gaskets are installed properly is critical to achieving the strict leak definitions outlined in regulatory standards. One approach some end users are taking to implement this change is through natural attrition. Others are taking a more active approach and are actively seeking out non-low-emission gaskets and creating maintenance activities to replace them.The Role of SWGs in a Low-Emission Future
As industries face increasing pressure to reduce emissions, SWGs, such as Teadit’s 913M gasket, stand out as a viable solution for ensuring compliance with future regulations. Their sealing capabilities, especially in challenging environments, make them an ideal choice for low-emission applications. While current consent decrees may not yet specify SWGs, their proven performance in achieving tight seals and minimizing leakage suggests they will be crucial to future environmental compliance strategies.In a world where emission standards are only becoming stricter, spiral wound gaskets offer both a technical solution and a path toward a greener, more sustainable future.
REFERENCE
ASME B16.20-2017 (Revision of ASME B16.20-2012) Metallic Gaskets for Pipe Flanges.