In wastewater management, proper sealing is essential to prevent leaks, which can cause environmental hazards, inefficiencies, and regulatory issues. Selecting appropriate packing materials (e.g., PTFE, graphite, carbon fiber) is crucial for leak prevention and protection against wear and chemicals.
Wastewater refers to water that has been utilized and subsequently contaminated by human activities, rendering it unsuitable for immediate reuse without proper treatment. It typically comprises of a mixture of organic and inorganic pollutants, including chemicals, pathogens, and debris, varying according to its source.
Wastewater can be categorized into several types: domestic wastewater, originating from household activities such as bathing, laundry, and food preparation; industrial wastewater, produced by industrial processes and manufacturing, often containing complex chemicals and heavy metals; stormwater runoff, which is water from precipitation that collects contaminants as it flows over impervious surfaces like roads and pavements; and agricultural wastewater, which includes runoff from farmlands, often carrying fertilizers, pesticides, and animal waste.
Effective treatment and management of each type of wastewater is essential to prevent environmental contamination and to maintain water quality standards. These systems often handle aggressive fluids that can cause damage to equipment and, if not properly sealed, may allow harmful leaks.
1. Preventing environmental contamination: Wastewater can contain harmful bacteria, toxic chemicals, and other contaminants that, if leaked, could harm ecosystems and pose health risks. A well-sealed system prevents these dangerous substances from reaching the environment.
2. Maintaining system efficiency: Reducing leaks leads to a system that operates more efficiently, reducing the need for reprocessing and saving energy. Leaks can lead to pressure loss, increased energy consumption, and premature wear on equipment, all of which drive up operational and maintenance costs.
3. Avoiding regulatory fines: In many regions, such as Europe and the U.S., environmental regulations impose heavy fines on companies responsible for wastewater leaks. Proper sealing helps ensure compliance with local regulations, avoiding penalties.
4. Ensuring public health: Leaks from wastewater systems can contaminate local water supplies, posing serious health risks. Effective sealing solutions help protect the public from exposure to hazardous substances.
Wastewater refers to water that has been utilized and subsequently contaminated by human activities, rendering it unsuitable for immediate reuse without proper treatment. It typically comprises of a mixture of organic and inorganic pollutants, including chemicals, pathogens, and debris, varying according to its source.
Wastewater can be categorized into several types: domestic wastewater, originating from household activities such as bathing, laundry, and food preparation; industrial wastewater, produced by industrial processes and manufacturing, often containing complex chemicals and heavy metals; stormwater runoff, which is water from precipitation that collects contaminants as it flows over impervious surfaces like roads and pavements; and agricultural wastewater, which includes runoff from farmlands, often carrying fertilizers, pesticides, and animal waste.
Effective treatment and management of each type of wastewater is essential to prevent environmental contamination and to maintain water quality standards. These systems often handle aggressive fluids that can cause damage to equipment and, if not properly sealed, may allow harmful leaks.
Why proper sealing is crucial in wastewater systems
Sealing in wastewater systems is important for several reasons:1. Preventing environmental contamination: Wastewater can contain harmful bacteria, toxic chemicals, and other contaminants that, if leaked, could harm ecosystems and pose health risks. A well-sealed system prevents these dangerous substances from reaching the environment.
2. Maintaining system efficiency: Reducing leaks leads to a system that operates more efficiently, reducing the need for reprocessing and saving energy. Leaks can lead to pressure loss, increased energy consumption, and premature wear on equipment, all of which drive up operational and maintenance costs.
3. Avoiding regulatory fines: In many regions, such as Europe and the U.S., environmental regulations impose heavy fines on companies responsible for wastewater leaks. Proper sealing helps ensure compliance with local regulations, avoiding penalties.
4. Ensuring public health: Leaks from wastewater systems can contaminate local water supplies, posing serious health risks. Effective sealing solutions help protect the public from exposure to hazardous substances.
Packing solutions
Selecting the correct sealing solutions to ensure a system’s integrity can be challenging, as wastewater can contain varying levels of abrasiveness and may also be chemically aggressive. Certain types of seals and packing materials will perform better than others depending on the specific conditions, such as the presence of slurry, chemical compatibility, the application’s pressure, and the temperature of the media.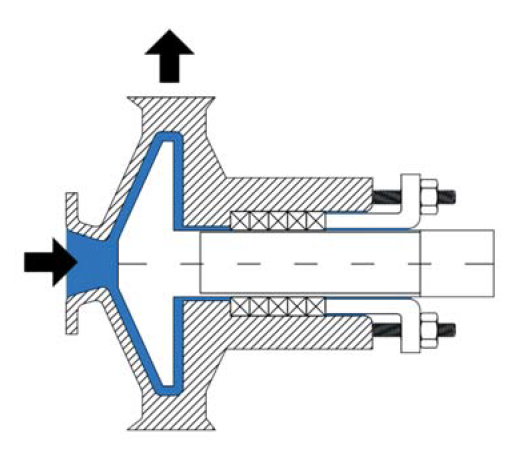
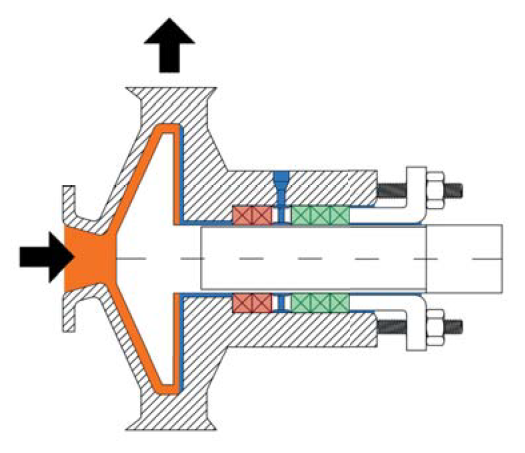
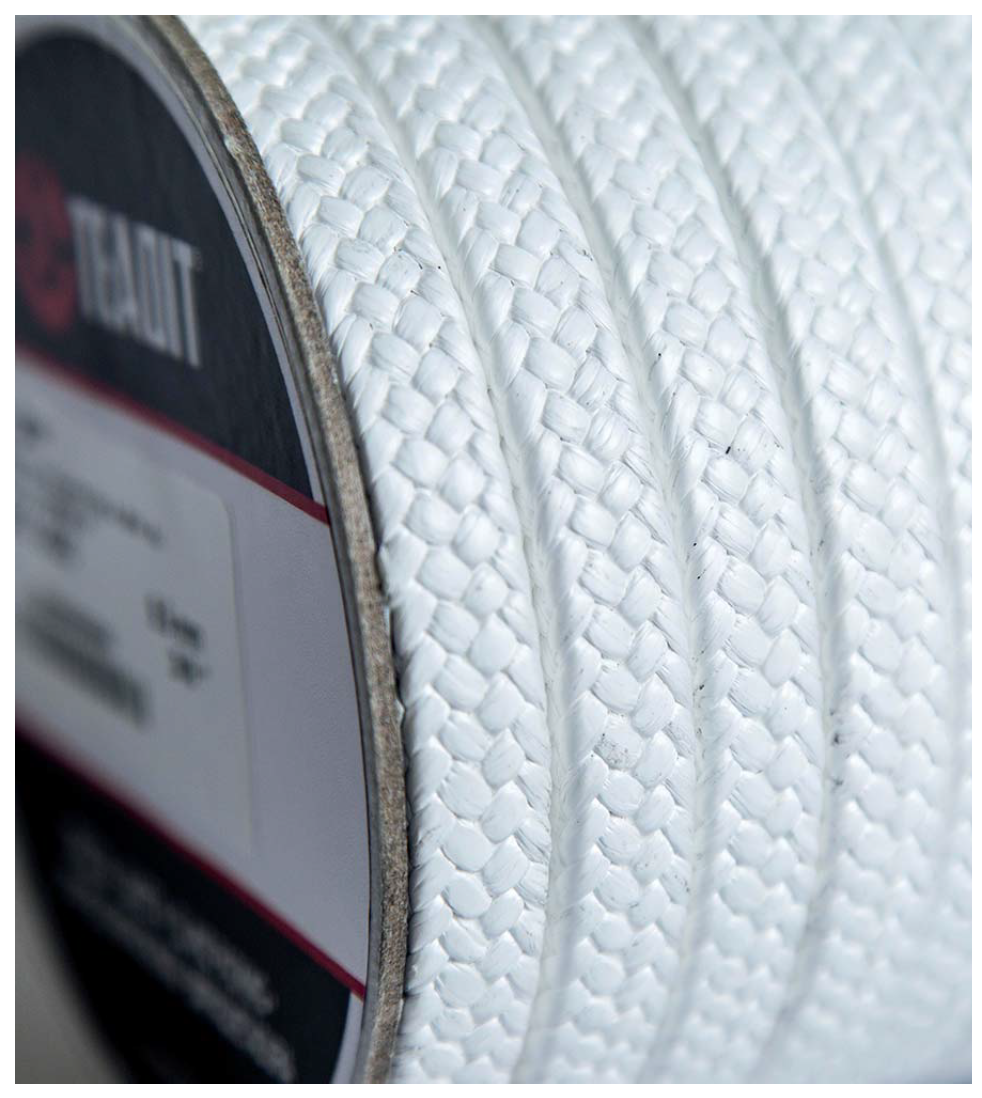
There are three primary types of packing seals typically used in wastewater applications to address these factors.
There are three main approaches to preventing leaks when working with abrasive materials in pump packing.
1. For pumps that process abrasive or slurry-filled media, packing materials with highly resistant synthetic fibers, like those with synthetic fibers, phenolic, and similar packing styles, are recommended. While these durable materials resist abrasives well, they also have higher coefficients of friction than other options, like carbon/graphite packing, which can sometimes cause challenges with temperature management.
2. In some wastewater applications, combining different packing materials may be necessary to balance performance and longevity. A dual packing system, for example, combines two types of packing: one designed to handle abrasive materials and another with lower friction and higher heat dissipation. For example, a dual packing system could consist of the first two packing rings (closer to the impeller) being a synthetic fiber packing style, highly resistant to abrasion. The subsequent packing rings could then be graphite and PTFE to minimize energy consumption and ensure smooth operation.
Graphite or carbon fiber packing
For general applications involving moderately abrasive media or chemical aggressiveness, graphite and carbon fiber packings—such as Teadit’s style 2200C and 2002—are excellent choices. Known for their ability to withstand high temperatures and resist aggressive chemicals, these packings provide a long-lasting seal with exceptional performance. Both of these styles, for instance, are constructed with a diagonal braiding of high-purity, continuous filament carbon fiber yarn impregnated with graphite and a corrosion inhibitor. This combination gives it enhanced properties, including a very low coefficient of friction and excellent heat dissipation, enabling use without flush water. These materials are ideal for abrasive environments and help extend the service life of pumps and valves by reducing wear.PTFE (Polytetrafluoroethylene) packings
For highly chemically aggressive wastewater applications, PTFE packings are ideal due to their excellent chemical resistance and low friction properties. Although not all PTFE packings are FDA-compliant, choosing FDA-compliant materials can support standardization across an entire plant, even as FDA standards are not typically required for wastewater systems. Teadit’s packing styles 2005 and 2006, for example, offer versatile and efficient sealing solutions when aggressive media is not present. Style 2005 is particularly suited for low-shaft-speed equipment, such as valves, while style 2006 includes a break-in lubricant, making it suitable for higher-shaft-speed equipment, like pumps. The complex braiding method using filled ePTFE results in packing with uniform density, high flexibility, and smoothness. This leads to very low emission values and an extremely long service life for the packing. Due to the high suppleness, only a minimum of maintenance is required.Highly resistant synthetic fiber packings
For the most abrasive wastewater applications, such as those containing heavy slurries, highly resistant synthetic fiber packing like Teadit style 2773 is recommended. These packings offer exceptional abrasion resistance and can withstand harsh operating conditions. Style 2773, for instance, is primarily composed of phenolic fibers and impregnated with PTFE, graphite, and similarly heat-resistant silicone oil. Both styles provide excellent options for handling varying levels of abrasiveness.Seals for pump applications
It is important to note that the packing used for valve stems often differs from that used in pump systems. Valve packing is typically designed to eliminate visible leakage entirely, providing a highly effective seal. In contrast, pump packing is expected to leak very slightly in a controlled manner. This minimal leakage is necessary to cool and lubricate the packing; without it, the packing can overheat and potentially burn.There are three main approaches to preventing leaks when working with abrasive materials in pump packing.
1. For pumps that process abrasive or slurry-filled media, packing materials with highly resistant synthetic fibers, like those with synthetic fibers, phenolic, and similar packing styles, are recommended. While these durable materials resist abrasives well, they also have higher coefficients of friction than other options, like carbon/graphite packing, which can sometimes cause challenges with temperature management.
2. In some wastewater applications, combining different packing materials may be necessary to balance performance and longevity. A dual packing system, for example, combines two types of packing: one designed to handle abrasive materials and another with lower friction and higher heat dissipation. For example, a dual packing system could consist of the first two packing rings (closer to the impeller) being a synthetic fiber packing style, highly resistant to abrasion. The subsequent packing rings could then be graphite and PTFE to minimize energy consumption and ensure smooth operation.
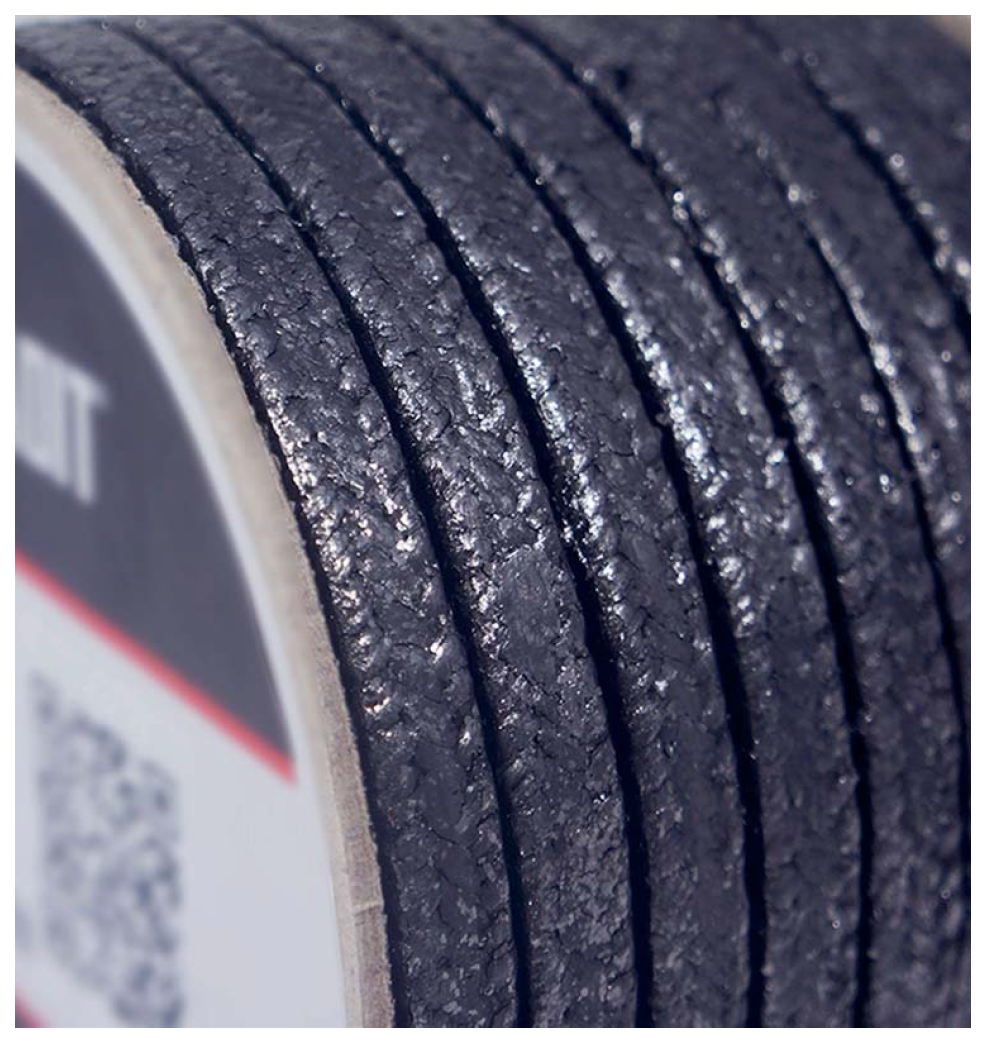
3. Using flush water is a highly effective strategy for wastewater applications where leaks of the transported fluid cannot be tolerated. In this method, clean water is injected into the stuffing box at a pressure slightly higher than the abrasive fluid, typically 1 bar higher. This water acts as a barrier, preventing the abrasive material from coming into direct contact with some of the packing rings, thus extending its life, reducing the friction between packing and shaft, and reducing maintenance costs. This approach also guarantees that any fluid leaking will be clean water, not wastewater.
While this strategy can effectively prevent hazardous leaks, there are two potential challenges to be aware of.
>While this strategy can effectively prevent hazardous leaks, there are two potential challenges to be aware of.
- The lantern ring may shift, potentially allowing a packing ring to obstruct the flush port, which can cause the flush to travel along the outer diameter of the stuffing box.
- Contaminated flush water can lead to the deterioration of the packing material.1 Although; typically, in these types of applications, the fluid being sealed tends to be even more aggressive than casual contaminations in the flush water.
Final thoughts
Effective sealing in wastewater applications requires a deep understanding of the specific challenges and media involved. While no single packing solution fits all needs, understanding the properties of various packing styles is a starting point for selecting appropriate materials based on abrasiveness and regulatory requirements. It is always best to consult a manufacturer to determine the optimal solution for a particular system. The right combination of materials, design, and maintenance strategies can ensure compliance, protect the environment, and improve operational efficiency.