**Originally Printed in Plant Engineering March/April 2025 Maintenance Roundtable
Experts reveal these maintenance trends you need to watch
This panel of experts reveals some of the top manufacturing maintenance trends. From artificial intelligence and machine learning to predictive maintenance, you’ll want to watch and implement these strategies.
By Plant Engineering
Maintenance insights
- Artificial intelligence (AI) and machine learning (ML) are playing a larger role in maintenance initiatives.
- Real-time monitoring and analytics can help predict equipment failures before they happen.
- Preparing for downtime can be a real challenge for many organizations.
Panel of experts
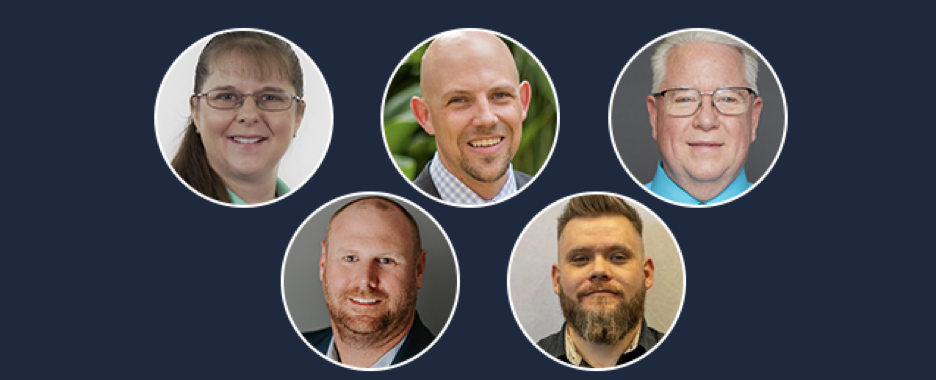
Clockwise from upper left: Stacey Jones, Global Portfolio Leader, Asset Performance Management, ABB; Erik Lindhjem, Vice President of Reliability Solutions, Emerson; Greg Nolan, Certified Compressed Air Systems Specialist, Hitachi Global Air Power; Mark Ruffin, Vice President, Sales and Engineering, Teadit; and John Wilkerson, Technical Training Manager, Kaishan Compressor USA.
What future trends should engineers, plant managers and designers expect for predictive and/or preventive maintenance, looking one or two years ahead?
Greg Nolan: Compressors being an integral utility for most manufacturing, we are seeing an increased priority being given to both predictive and preventive maintenance (PM). Remote monitoring capabilities will continue to expand, allowing compressed air users to see more information regarding their compressed air system on their phone or tablet.
Stacey Jones: Two things: Enhanced condition monitoring with wired and wireless sensors. The use of sensors for condition monitoring is becoming more widespread. These sensors track performance and provide insights into potential issues like abnormal vibrations or heat, enabling proactive maintenance.
Second, increased adoption of predictive maintenance leveraging artificial intelligence/machine learning (AI/ML)-enabled technologies. With advancements in internet of things and AI technologies, more organizations will be leveraging real-time data to anticipate equipment failures before they occur. This approach can help to reduce downtime and extend asset life but change management will be critical to realize the true value of implementing these new technologies.
Mark Ruffin: Predictive maintenance (PdM) strategies leverage real-time monitoring and analytics to anticipate failures before they occur, while preventive maintenance follows a scheduled approach to replace components at fixed intervals. Combining both methods ensures the best balance of cost efficiency and reliability.
As it relates to sealing products, temperature cycles can increase the likelihood of leaks. Extending the run times of units increases the likelihood of having process upsets that can cause temperature swings. Some sealing technologies are more forgiving of temperature swings than others. Engineers should work with their sealing product supplier to understand what product would be best for their application and implement assembly best practices. Having the right sealing product and installing it the correct way will provide the application with the reliability associated with longer run times.
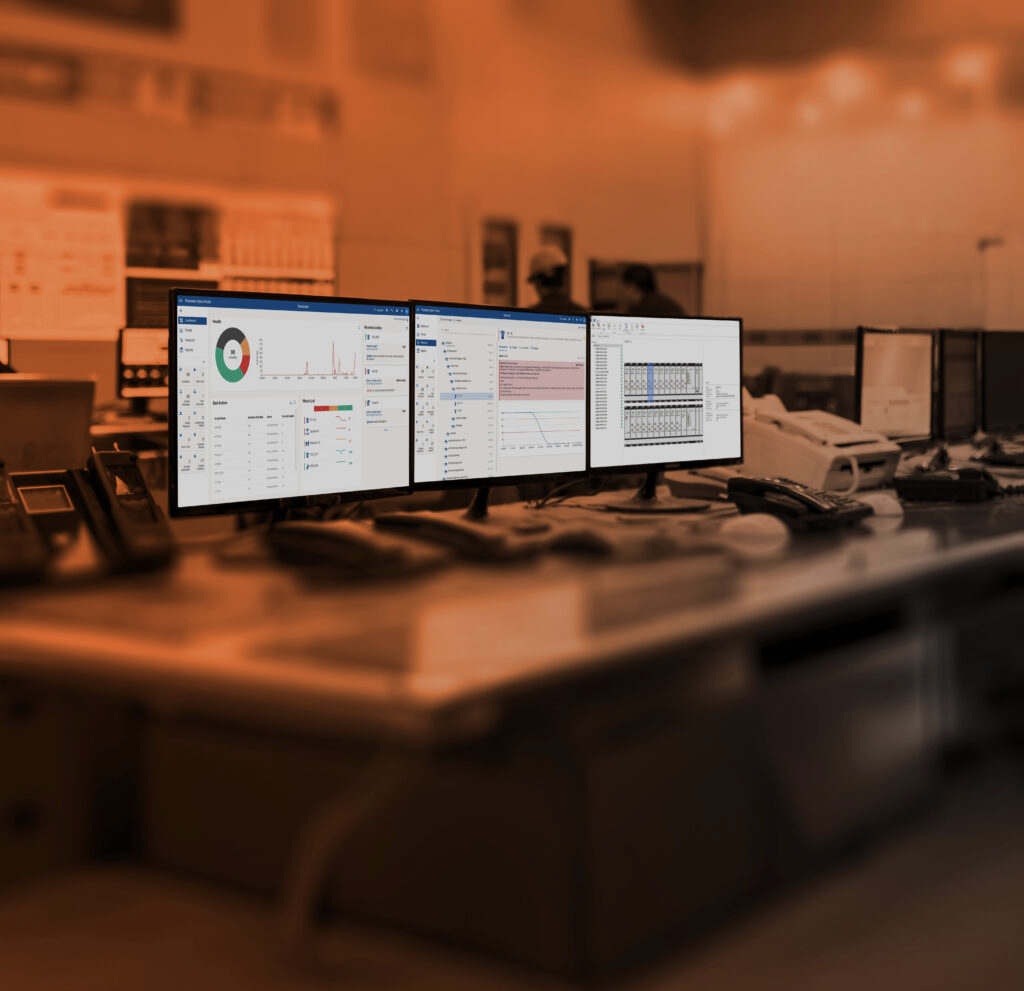
Courtesy: Emerson
What’s the current trend in maintenance for industrial and manufacturing facilities?
Ruffin: Companies are focusing on reliability-centered maintenance (RCM) and predictive strategies that optimize uptime, reduce failures and ensure compliance with safety and environmental standards. These approaches rely on advanced monitoring, historical data and expert-driven analysis.
Additionally, there is an effort to extend turnaround cycles. Previously, a five-year cycle was considered relatively standard. Currently, it is not uncommon for units to run for six years between turnaround cycles.
What are the fundamental distinctions between predictive and preventive maintenance and how do these approaches complement each other in an ideal maintenance strategy?
John Wilkerson: The fundamental distinction between preventive and PdM lies in their approach and application. Preventive maintenance follows a manufacturer’s recommended schedule based on a generic installation scenario. Essentially, if a machine is installed as the manufacturer specifies — or within acceptable variations — performing the recommended maintenance ensures reliability between service intervals.
PdM, on the other hand, uses data-driven insights — gathered through human expertise, technology or a combination of both — to monitor the actual performance of a machine. It identifies when the equipment is deviating from the manufacturer’s baseline parameters and allows operators to take corrective action before issues escalate.
In an ideal maintenance strategy, these two approaches work in tandem. Preventive maintenance lays the foundation for reliable operation, while predictive maintenance provides the specificity needed to address the unique challenges of real-world applications, where equipment may not always operate under optimal conditions. By combining both methods organizations can maximize equipment reliability, minimize downtime and ensure maintenance activities are precisely aligned with the demands of each application.
Jones: PM involves regular, scheduled maintenance activities to prevent equipment failures while PdM uses real-time data and advanced analytics to detect equipment issues and predict when a potential failure may occur. Some equipment degrades and fails on a predictable frequency (like oil degradation or clogged filters) and PM is ideal. However, a large percentage of equipment failures (~80% per industry analysts) still happen randomly. To catch these, PdM has the advantage. For the best maintenance strategies, you need to use both to realize the following benefits:
- Holistic coverage: Combining PdM and PM ensures that both unexpected and predictable issues are addressed. PdM can catch anomalies that PM might miss, while PM ensures routine checks and upkeep.
- Optimized resource allocation: PdM helps prioritize critical maintenance tasks based on real-time data, while PM ensures that all equipment receives regular attention.
Ruffin: Businesses are adopting condition-based maintenance techniques, integrating sensor technology, machine learning and failure trend analysis to improve asset longevity and operational efficiency. The use of load-indicating studs is an example of performing maintenance based on data. If the stud shows a significant loss in load, then a leak is more likely to happen. Retightening following safe and recommended practices, is a maintenance activity that can prevent the need for reactive maintenance.
Describe the successes from using programs that incorporate predictive, preventive, reliability-centered or reactive maintenance.
Jones: There is a time and place for each maintenance approach. Deciding which strategy to apply depends on the criticality, cost and impact of the equipment. For high-criticality and high-impact equipment, both preventive and PdM technologies should be applied. However, for redundant or low-cost equipment, reactive maintenance may be more appropriate.
To determine which equipment to focus on, implementing an RCM approach is essential. Successful maintenance strategies begin with identifying which assets to prioritize in the maintenance budget. Next, research how this type of equipment has failed in the past — whether predictably or randomly. Based on this analysis, apply the level of PdM that best manages these risks.
By following these steps organizations can ensure that their maintenance efforts are both efficient and effective, ultimately leading to improved reliability and reduced costs.
Nolan: PdM is generally based on expected life cycles of a component and PM is usually based on the compressor manufacturer’s recommended maintenance schedule. Using both aspects of maintenance and adjusting a maintenance schedule to account for environmental conditions and duty cycles, you end up with a more reliable compressor system that will limit the need for reactive maintenance that can cost the user production.
Wilkerson: Organizations that successfully implement a maintenance program incorporating predictive, preventive, reliability-centered and reactive maintenance enjoy significant benefits in equipment uptime, operational efficiency and cost savings. Each approach plays a unique role, but together they create a robust framework for addressing maintenance challenges proactively and effectively.
PdM, often powered by advanced technologies like AI-driven vibration analysis, helps detect subtle changes in equipment performance, such as bearing wear, before they escalate into major issues. PM provides a structured, routine approach to maintaining equipment reliability based on manufacturer recommendations. Meanwhile, RCM shifts the focus beyond warranty compliance to prioritize long-term operational consistency by tailoring strategies to specific applications.
The role of reactive maintenance, while less desirable, cannot be eliminated entirely. However, with the other three components in place, the frequency and costs of reactive responses are significantly reduced. For example, having a clear plan for emergency scenarios — such as knowing which rental service to call at 2 a.m. when critical equipment fails — ensures swift recovery and minimizes downtime.
Companies that integrate all four approaches experience far fewer unplanned outages and lower out-of-pocket expenses tied to urgent repairs. By reducing costly reactive maintenance, these organizations increase uptime, maintain productivity and achieve a lower total cost of ownership for their equipment. This comprehensive strategy not only protects operational continuity but also drives measurable improvements in efficiency and reliability.
What types of computer applications are in use to support your maintenance functions?
Erik Lindhjem: Software is becoming more critical to supporting maintenance functions with each passing year. However, it isn’t just software installed on servers that reliability teams depend upon to drive better performance, safety and uptime in the plant. The software available in smart devices in the field and software-as-a-service applications in the cloud are increasingly important as well. Ultimately, closing the loop on maintenance is becoming less about hardware and software and more about mobility of data — putting critical information in front of the right people at the right time.
Today, highly effective maintenance and reliability teams are embracing a boundless automation vision of seamless data mobility to drive critical data from the intelligent field, through the edge and into the cloud, empowering them to more easily get the right work done quickly and effectively. Ultimately, those teams are employing solutions like asset monitoring software, edge analytics, predictive maintenance software and enterprise-level asset performance management platforms to identify asset issues by exception, prioritize maintenance and more effectively execute that maintenance with customized decision support. Building those solutions as part of a seamlessly integrated architecture is helping teams make those workflows repeatable at scale, while ensuring problems and solutions are continually fed to analytics to make each subsequent problem identification and repair faster.
What are some of the key challenges for improving maintenance at your facility?
Wilkerson: One of the key challenges in improving maintenance is scheduling downtime. Even in facilities that don’t run three shifts or operate around the clock, there’s often resistance to planned downtime. It stems from the perception that any halt in operations, even temporarily, disrupts productivity. This mindset frequently leads to delays in addressing maintenance needs, especially as equipment ages or personnel roles change.
The challenge is compounded by human nature’s tendency to favor reactive over preventive behavior. Much like avoiding a doctor’s visit until a problem arises, many facilities postpone maintenance until a failure occurs. This reactive approach often results in higher costs and longer disruptions compared to proactive strategies.
Overcoming this requires a cultural shift toward proactive planning and the integration of predictive, preventive and RCM practices. By embedding these practices into operations, facilities can identify potential issues early, schedule downtime efficiently and maintain equipment within manufacturer specifications. It’s worth noting that even facilities running 24/7 can schedule and manage downtime effectively with proper planning, reducing the long-term risks of unexpected breakdowns and costly repairs.
Describe the connected devices for remote monitoring your facility incorporates.
Lindhjem: Today, more and more plants are finding they have limited staff and even more limited time to spend in data collection and analysis. Much of the collection problem can be solved with capital expenditure projects to implement wireless vibration monitoring, edge analytics devices and other automation technologies. However, these teams still need the time and expertise to deal with the data those solutions generate. As a result, many are turning to connected services solutions that deliver remote monitoring of machinery. The most advanced automation solutions providers offer remote asset monitoring solutions where experts leverage analytics (artificial intelligence/machine learning (AI/ML)/first principle) to identify emerging issues with plant machinery, evaluate them and make recommendations to help their customers’ reliability teams better maintain their assets, without spending time tied to their desks performing deep data analysis. The most advanced connected services providers have extensive networks of partner organizations that provide even more tailored service. While still performing remote monitoring, these partner sites are typically close to the plants and likely know the equipment and how it is operated and can thus do a very thorough job of recommending how to address issues.