To maximize the lifespan of an industrial component, each asset must follow a standard operating procedure and adhere to a specific maintenance program. These programs involve regular inspections and timely repairs to prevent unexpected breakdowns and costly downtime. By implementing a comprehensive strategy, companies can extend the lifespan of their equipment, improve safety standards and enhance overall productivity.
Maintenance programs can generally be categorized into three types: preventive maintenance (PM), condition-based maintenance (CBM) and corrective maintenance (CM).
It is recommended that each piece of equipment have one or more of these dedicated maintenance programs. This approach ensures maintenance tasks are performed regularly and consistently.
When developing maintenance programs, it is important to consider the types of equipment and their operating parameters. A comprehensive inventory of all equipment and machinery must be established, including detailed records of specifications, operating conditions and maintenance history.
Once established, the development of an asset-specific maintenance program involves three key criteria:
Adhering to the manufacturer's recommendations is necessary to meet regulatory requirements. They also provide insight into some signs operators should watch for once the asset is installed in a plant or refinery. Therefore, to ensure an expansion joint PM program is as comprehensive as possible, it’s best to consider SME recommendations for each type of expansion joint.
For nonmetallic expansion joints, the best maintenance practice involves replacing the bellows (fabric belt) and thermal insulation pillow in case of a rupture. Regular visual inspections of the bellows are crucial and, in some cases, a thermal camera inspection can be beneficial to detect issues early.
If the bellows of metallic expansion joints rupture or leak, the entire expansion joint must usually be replaced. Regular maintenance and inspection can help prevent such occurrences and extend the joints' lifespan.
For metallic expansion joints, preventive maintenance should involve:
When an expansion joint issue is detected, it’s wise to contact the manufacturer for assistance. They can provide guidance on the criticality of the repair and suggest the appropriate course of action. Prompt communication with the manufacturer ensures issues are addressed correctly and efficiently, minimizing downtime and maintaining the system's safety and functionality.
Furthermore, well-maintained machinery operates more efficiently, reducing energy consumption and operational costs. Investing in industrial maintenance not only safeguards the longevity and reliability of assets but also fosters a proactive approach to addressing potential issues before they escalate, ultimately contributing to the sustainability and competitiveness of the business.
Learning Objectives
Expansion Joint Maintenance Insights
Maintenance programs can generally be categorized into three types: preventive maintenance (PM), condition-based maintenance (CBM) and corrective maintenance (CM).
- Preventive maintenance: This type of maintenance is time-based and scheduled at regular intervals, such as monthly, annually or biennially. It involves routine inspections and servicing to prevent equipment failures.
- Condition-based maintenance: CBM relies on monitoring the condition of equipment to decide when maintenance should be performed. Techniques such as vibration analysis, thermography and acoustic testing are used to assess the health of the equipment.
- Corrective maintenance: This approach addresses issues as they occur, focusing on fixing problems after they have been identified during regular operations or inspections.
It is recommended that each piece of equipment have one or more of these dedicated maintenance programs. This approach ensures maintenance tasks are performed regularly and consistently.
Preventive Maintenance’s Role in Maintenance Programs
Unlike other equipment, expansion joints are often maintained under CM programs, where issues are addressed as they arise. Implementing PM programs can significantly improve operational reliability by moving from a reactionary approach to a preventive one. Not only does it improve performance, but operators can achieve better resource allocation, maintenance staff can focus on proactive tasks rather than constantly addressing emergencies and the frequency and duration of unplanned downtime can be reduced.When developing maintenance programs, it is important to consider the types of equipment and their operating parameters. A comprehensive inventory of all equipment and machinery must be established, including detailed records of specifications, operating conditions and maintenance history.
Once established, the development of an asset-specific maintenance program involves three key criteria:
- Determining equipment criticality. Identify and prioritize equipment based on its importance to the operation. Critical equipment that has no redundancy and can cause significant downtime if it fails should receive more attention.
- Following manufacturer recommendations. Follow the maintenance guidelines provided by the equipment manufacturers. These recommendations are often a part of environmental or operational permits.
- Identifying operational conditions: Consider the equipment's operating environment, including temperature, pressure and the type of fluids being handled. This helps determine the appropriate maintenance actions and intervals.
Steps to Build a Maintenance Program for Expansion Joints
Five things must occur when building a maintenance program.- Identify equipment and assign criticality. List all the equipment, including expansion joints and assign a criticality rating based on factors like redundancy and impact on operations.
- Determine applicable maintenance types. For each piece of equipment, decide on the appropriate maintenance type. For expansion joints, this may include:
- Visual inspections during scheduled outages.
- Thermographic inspections to detect hot spots and leaks while in operation.
- Real-time condition monitoring for critical expansion joints, which can involve sensors to detect temperature and pressure changes.
- Establish a maintenance schedule. Develop a schedule that outlines when and how often each type of maintenance should be performed. For instance, visual inspections might be conducted bi-annually during plant shutdowns, while thermographic inspections could be quarterly.
- Consult experts and manufacturers. Engage with subject matter experts (SMEs) and manufacturers to ensure the maintenance program is comprehensive and current. This can involve reviewing new technologies and methodologies for monitoring and maintaining expansion joints.
- Implement and monitor the program. Roll out the maintenance program and continuously monitor its effectiveness. Adjust the program as needed based on inspection feedback and condition monitoring data.
Adhering to the manufacturer's recommendations is necessary to meet regulatory requirements. They also provide insight into some signs operators should watch for once the asset is installed in a plant or refinery. Therefore, to ensure an expansion joint PM program is as comprehensive as possible, it’s best to consider SME recommendations for each type of expansion joint.
Maintenance for Metallic Versus Nonmetallic Expansion Joints
There are two primary groups of expansion joints: metallic and nonmetallic. These categories encompass a range of products designed to meet various industrial needs and applications.For nonmetallic expansion joints, the best maintenance practice involves replacing the bellows (fabric belt) and thermal insulation pillow in case of a rupture. Regular visual inspections of the bellows are crucial and, in some cases, a thermal camera inspection can be beneficial to detect issues early.
If the bellows of metallic expansion joints rupture or leak, the entire expansion joint must usually be replaced. Regular maintenance and inspection can help prevent such occurrences and extend the joints' lifespan.
Preventive Maintenance for Installed Expansion Joints
Once the expansion joint is installed, operators should perform regular preventive maintenance checks. For nonmetallic expansion joints, frequent visual inspections should include:- Ensuring the outside bellows are free of material deposits that could obstruct air circulation.
- Checking for any missing bolts in the clamping bars.
- Looking for signs of rupture or leakage in the bellows.
- Observing any localized changes in the color of the outside bellows, which could indicate overheating or other issues.
For metallic expansion joints, preventive maintenance should involve:
- Checking for ruptures or leaks in the outside bellows.
- Monitoring the bellows’ pitch or movement indicator to identify any unexpected movements.
- Checking bellows’ convolution spoilt or local deformities.
- Checking leakage between bellows’ redundant plies.
- Checking pipe anchors and guides (can cause expansion joint unexpected movements).
- Comparing the theoretical fatigue life to historical expansion joint life and planning the expansion joint exchange.
When an expansion joint issue is detected, it’s wise to contact the manufacturer for assistance. They can provide guidance on the criticality of the repair and suggest the appropriate course of action. Prompt communication with the manufacturer ensures issues are addressed correctly and efficiently, minimizing downtime and maintaining the system's safety and functionality.
A Robust Maintenance Program Enhances Expansion Joint Performance
Building a robust maintenance program for expansion joints involves understanding different maintenance types, assessing equipment criticality and following manufacturer recommendations. By shifting from a reactive approach to a preventive and condition-based maintenance strategy, facilities can enhance reliability, reduce costs and maintain safety standards. Regular inspections, condition monitoring and expert consultations are key components of a successful maintenance program that ensures the long-term performance and safety of expansion joints.Furthermore, well-maintained machinery operates more efficiently, reducing energy consumption and operational costs. Investing in industrial maintenance not only safeguards the longevity and reliability of assets but also fosters a proactive approach to addressing potential issues before they escalate, ultimately contributing to the sustainability and competitiveness of the business.
Learning Objectives
- Understand the three types of expansion joint maintenance programs.
- Grasp the best practices for maintenance programs.
- Develop a robust expansion joint maintenance schedule.
Expansion Joint Maintenance Insights
- The three types of maintenance programs include preventive, condition-based and corrective.
- Expansion joints are maintained under condition-based programs.
- The two types of expansion joints are metallic and nonmetallic.
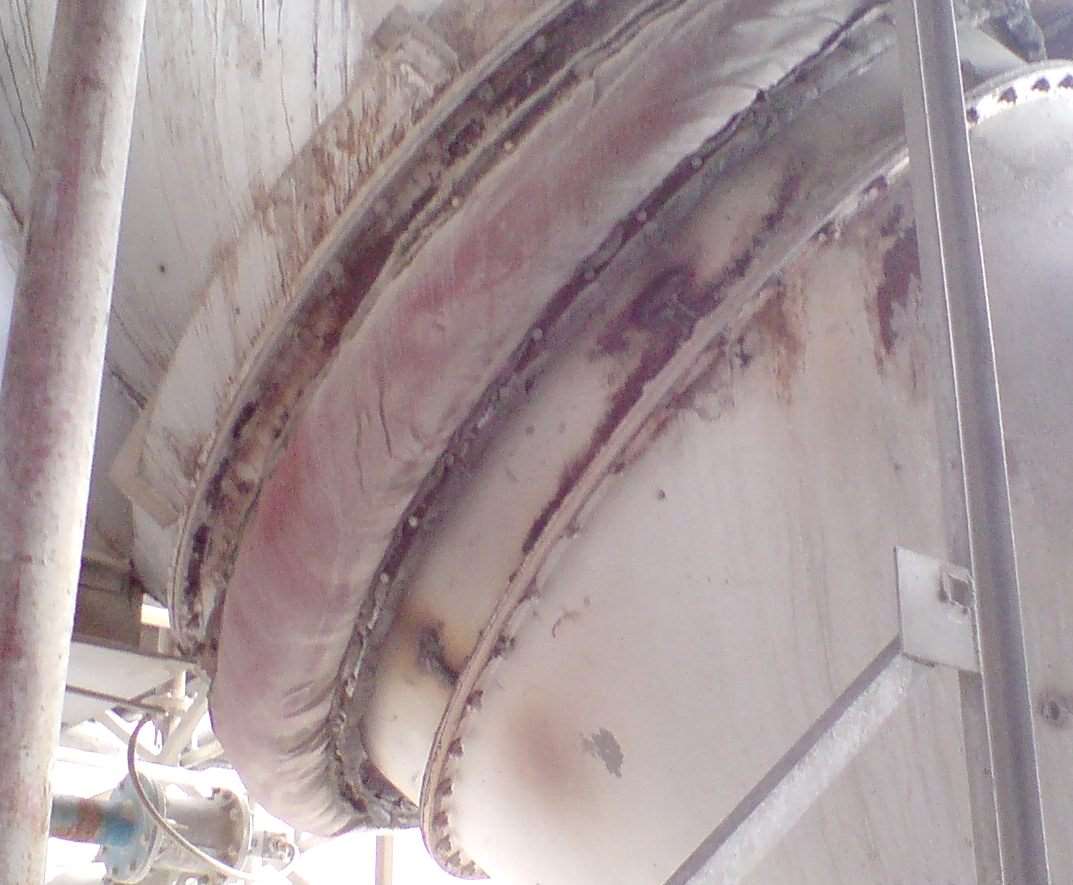
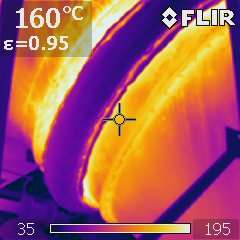
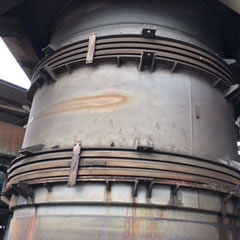