In today’s rapidly evolving industrial landscape, there is a growing emphasis on environmental sustainability and the reduction of harmful emissions. Fugitive emissions, which refers to the unintended release of gases or vapors from industrial processes, pose significant challenges to environmental preservation. To address this issue, industries are increasingly adopting more rigorous controls to minimize fugitive emissions and ensure compliance with stringent environmental regulations. Over the years, various sectors have made a significant commitment to addressing this issue through the implementation of enhanced monitoring systems, improved maintenance practices, updated sealing technologies, employee training, regulatory compliance, and technology integration reducing the occurrence of fugitive emissions.
Providing a reliable sealing mechanism to prevent leaks and minimize fugitive emissions is crucial as industries strive to enhance their environmental sustainability and meet stringent regulatory requirements. There is an increasing focus on upgrading sealing technologies by adopting advanced gaskets and seals. Industries can achieve more rigorous control over fugitive emissions, ensuring operational efficiency while minimizing environmental impact.Gaskets are essential components used in industrial equipment to provide a seal between two surfaces and prevent leakage of fluids or gases. As such, the performance of gaskets is critical to ensuring the safety and reliability of industrial operations. However, assessing gasket performance can be challenging due to the complex operating conditions under which gaskets operate.
One such industry standard that guides the selection and performance of gaskets is EN 13555. Developed by the European Committee for Standardization (CEN), EN 13555 provides guidelines for the classification and testing of gaskets, ensuring their reliability and efficiency in controlling fugitive emissions. In this article, we will elaborate on the highlights to give an understanding of the standard.The standard defines all parameters involved in studying gasket behavior in flanged joints, which are later used in calculation definitions in EN 1591-1 which provides a comprehensive algorithm that explains the operation of joints, considering various factors such as the elastic deformation of the joint, as well as both elastic and plastic deformations of the sealing material.
From a gasket selection point of view, the EN 13555 standard defines several parameters crucial in determining the suitable gasket for a specific application. These parameters, outlined in the standard, help ensure optimal sealing performance and compliance with industry requirements. According to the EN 13555 standard, some key parameters defined for gasket selection include:
From a gasket selection point of view, the EN 13555 standard defines several parameters crucial in determining the suitable gasket for a specific application. These parameters, outlined in the standard, help ensure optimal sealing performance and compliance with industry requirements. According to the EN 13555 standard, some key parameters defined for gasket selection include:
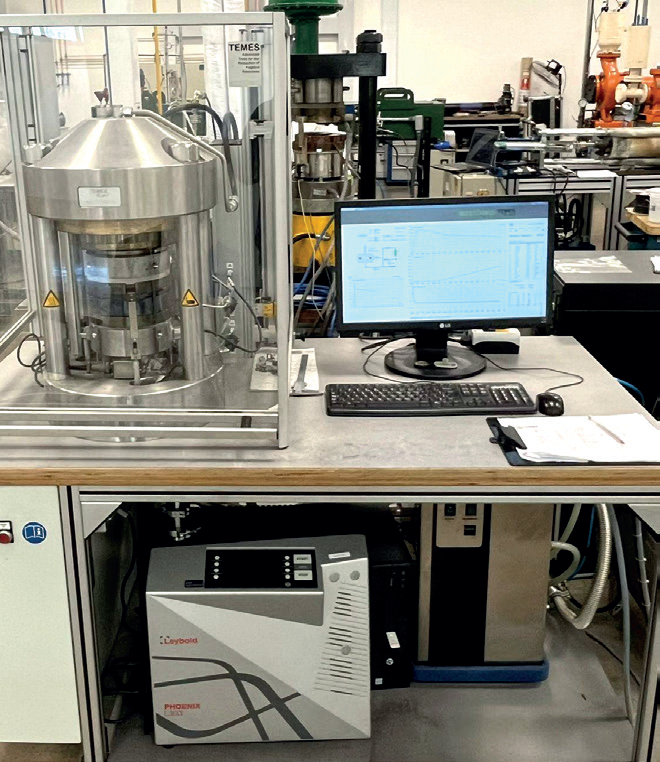
– QSmax: Maximum surface pressure that may be imposed on the gasket at the indicated temperatures without collapse or ‘crash.’– EG: Unloading modulus of elasticity determined from the thickness recovery of the gasket between the initial compression surface pressure and unloading to a third of this initial surface pressure (modulus of elasticity).
– PQR: Factor allowing for the effect on the imposed load of the relaxation of the gasket between the completion of bolt up and long-term experience service temperature.
– ΔeGC: Additional change in thickness of the gasket under the service conditions of temperature and gasket surface pressure in the axial direction.
– LN: Tightness classes that denotes maximum limit of defined leak rates. This is shown in Table 1.
– Qmin: Minimum gasket surface pressure on assembly required at the ambient temperature to seat the gasket into the flange facing roughness and close internal leakage channels, ensuring the tightness class is at the required level L for the internal test pressure.
– QSmin: Minimum gasket surface pressure required under the service pressure conditions (i.e., after off-loading and at the service temperature) to maintain the required tightness class L for the internal test pressure.
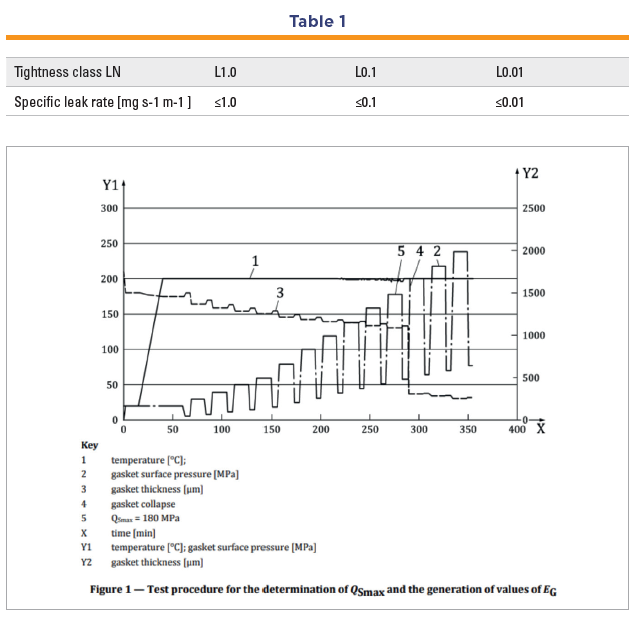
The standard provides more detailed guidance on test preparation and evaluation. EN 13555 specifies the required instrumentation and measurement procedures, including the use of calibrated equipment to ensure accurate and reliable results. It also provides clear guidelines on the evaluation of test results, including the calculation of maximum leakage rate, total leakage volume, and time to reach a specified leakage rate. This guidance helps ensure that test results are consistent and reliable across different testing laboratories and allows for better comparison of gasket performance across different manufacturers and products.
– PQR: Factor allowing for the effect on the imposed load of the relaxation of the gasket between the completion of bolt up and long-term experience service temperature.
– ΔeGC: Additional change in thickness of the gasket under the service conditions of temperature and gasket surface pressure in the axial direction.
– LN: Tightness classes that denotes maximum limit of defined leak rates. This is shown in Table 1.
– Qmin: Minimum gasket surface pressure on assembly required at the ambient temperature to seat the gasket into the flange facing roughness and close internal leakage channels, ensuring the tightness class is at the required level L for the internal test pressure.
– QSmin: Minimum gasket surface pressure required under the service pressure conditions (i.e., after off-loading and at the service temperature) to maintain the required tightness class L for the internal test pressure.
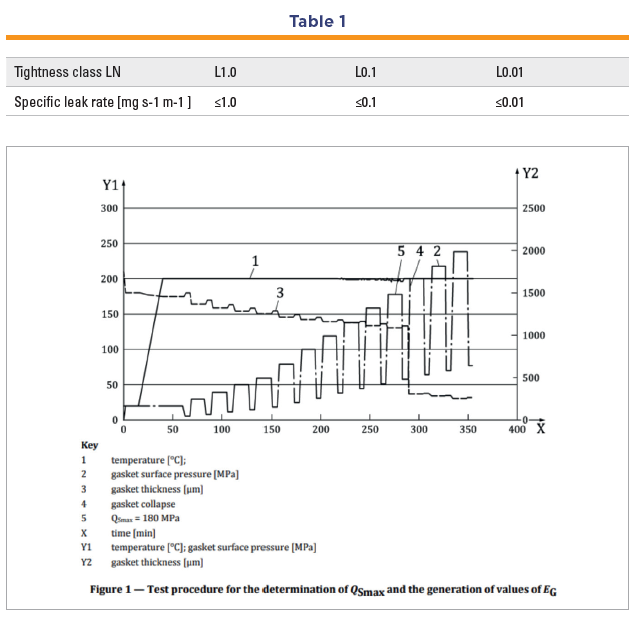
The standard provides more detailed guidance on test preparation and evaluation. EN 13555 specifies the required instrumentation and measurement procedures, including the use of calibrated equipment to ensure accurate and reliable results. It also provides clear guidelines on the evaluation of test results, including the calculation of maximum leakage rate, total leakage volume, and time to reach a specified leakage rate. This guidance helps ensure that test results are consistent and reliable across different testing laboratories and allows for better comparison of gasket performance across different manufacturers and products.
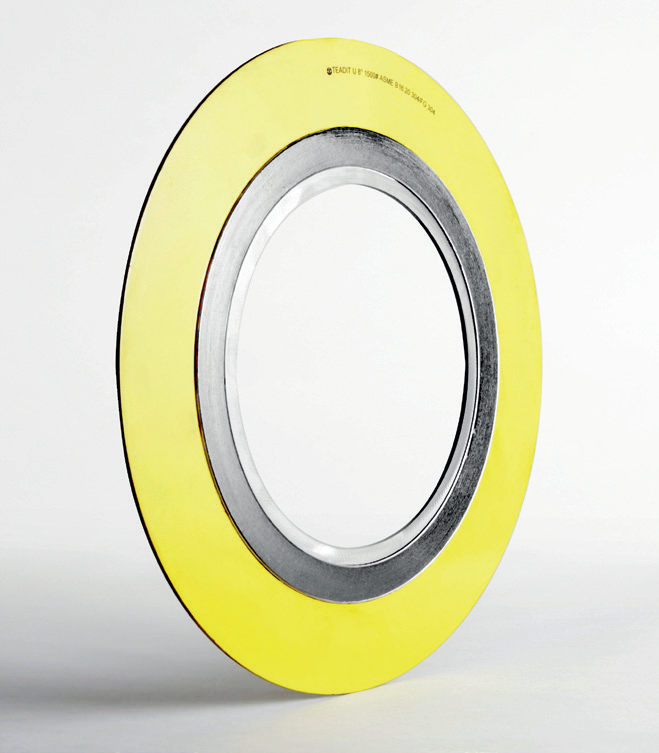
EN 13555 provides detailed guidance on sample preparation, storage, and conditioning. The standard specifies the size and shape of the samples and how they should be stored and conditioned before testing. These guidelines help ensure that test results are consistent and accurate, reducing the risk of errors and variability in test results.
The standard describes two different scenarios: one for determining the values of Qmin(L) and QSmin(L) related to leakage and another for determining QSmax, EG, PQR, ΔeGC, and μG related to gasket behavior. The first set of parameters relates to leakage, while the second set relates to gasket behavior.
Test Method
The fundamental importance of a gasket lies in its ability to establish and sustain a reliable seal. It is noteworthy that the data obtained from these tests not only serve as valuable input for the calculation method defined in the standard but also proves beneficial for advancing the development of improved gaskets.The standard describes two different scenarios: one for determining the values of Qmin(L) and QSmin(L) related to leakage and another for determining QSmax, EG, PQR, ΔeGC, and μG related to gasket behavior. The first set of parameters relates to leakage, while the second set relates to gasket behavior.
For gasket behavior, the test procedure involves increasing the temperature of the gasket to the desired level while applying an initial surface pressure. Subsequently, cyclic compression and recovery loadings are applied to the gasket, gradually increasing the surface pressures until reaching the point where the gasket collapses or the maximum load of the test machine or the maximum specified surface pressure by the manufacturer is reached. Throughout each loading cycle, the reduction in thickness per unit of surface pressure increment is measured and recorded.The surface pressure value observed in the cycle immediately before the collapse is considered as QSmax for that particular temperature. The test procedure, visually depicted in Figure 1 of the standard, is presented below for reference.
These unloading cycles, represented in the figure, allow the generation of values for EG as described in the standard.
The PQR factor is determined by comparing the residual load to the original load obtained from a relaxation test conducted on a compression press with a known stiffness. The ΔeGC factor measures the additional change of the gasket thickness associated with load loss during the controlled stiffness relaxation test. The stiffness of the rig used for the test varies depending on the flange designation, it is set as 500 kN/mm for an EN 1514 DN 40/ PN 40 gasket and 1,500 kN/mm for an EN12560 4” Class 300 gasket.
These unloading cycles, represented in the figure, allow the generation of values for EG as described in the standard.
The PQR factor is determined by comparing the residual load to the original load obtained from a relaxation test conducted on a compression press with a known stiffness. The ΔeGC factor measures the additional change of the gasket thickness associated with load loss during the controlled stiffness relaxation test. The stiffness of the rig used for the test varies depending on the flange designation, it is set as 500 kN/mm for an EN 1514 DN 40/ PN 40 gasket and 1,500 kN/mm for an EN12560 4” Class 300 gasket.
For the scenario corresponding to Leakage Data, the standard defines the test procedure in a loading and unloading cycle manner on the gasket, with measurement of the leakage rate at the effective surface pressure with internal gas pressure; gas is marked to be Helium. Figure 1 shows an expanded PTFE gasket to provide an understanding of its data.The thicker line represents the loading curve, blue arrows show the direction in how the load curve is read. The thinnest line corresponds to the unloading curve of the test, green arrows show the direction in how the unloading curve is read. Each black dot on these curves corresponds to the applied surface pressure and the measured leakage point. Data between those dots are interpolations for diagram representation. The yellow dots, called Qmin or QSmin, represent the assembly or operational stress required to comply with the tightness class obtained through interpolation.
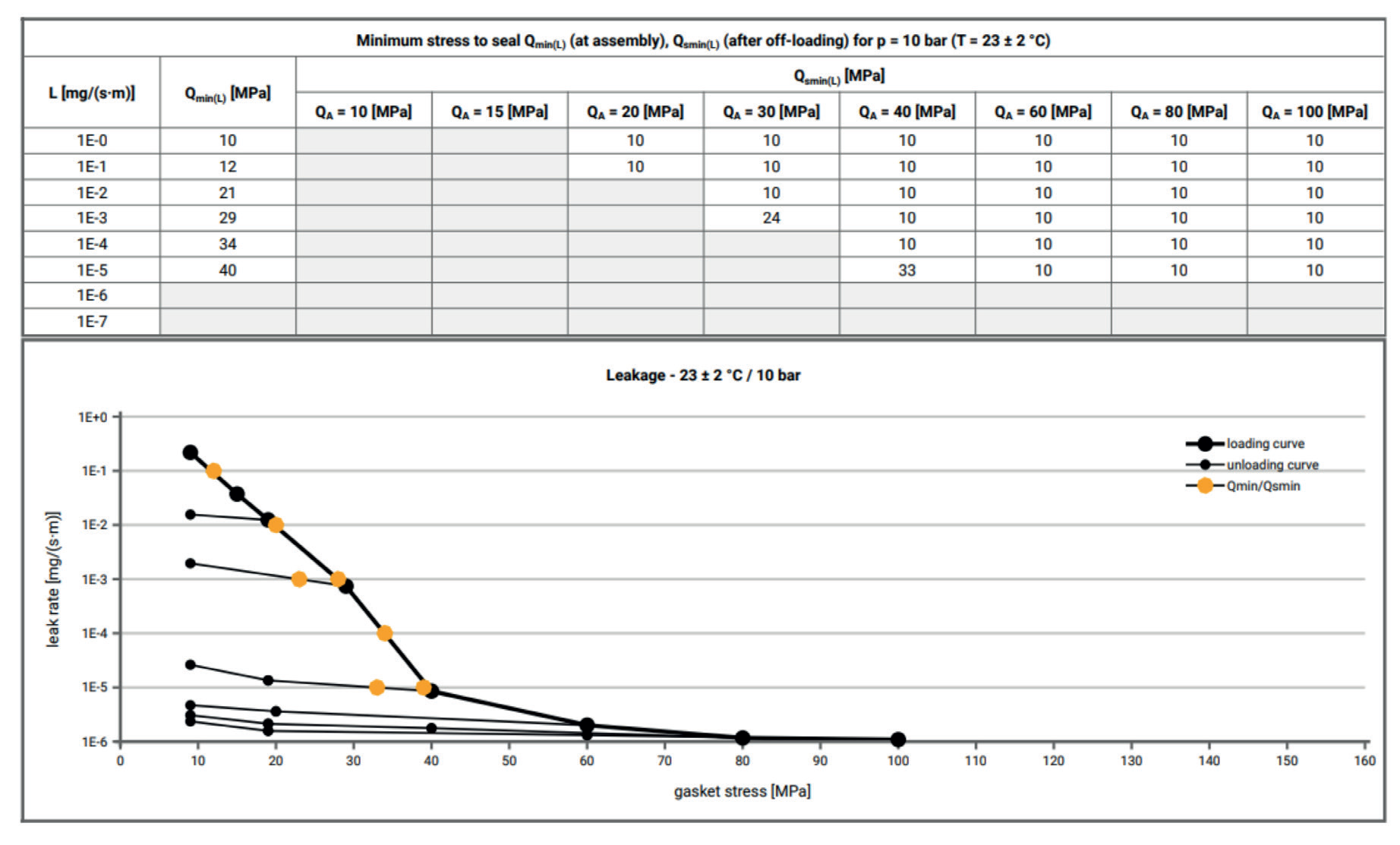
One way to use this information is to verify the amount of gasket stress that remains on the gasket after it has been adjusted to the flange surface and has undergone relaxation. Assuming a gasket stress of 30 MPa during installation and considering a PQR of 0.5, the gasket stress after relaxation would be 15 MPa. The image below illustrates these values and indicates their position in relation to leakage levels. This value suggests compliance with tightening class L0.01. If the application requirements demand compliance with a higher class, it will be necessary to increase the assembly gasket stress to above 40 MPa.
The test method provides a representation of the performance of gaskets under actual operating conditions and is appropriate for evaluating the suitability of gaskets for specific applications. From cyclic compression and recovery loadings to relaxation tests, the procedures outlined in EN 13555 offer a comprehensive approach to assessing gasket behavior under various operating conditions.
Conclusion
In summary, EN 13555 serves as a comprehensive and reliable framework for the testing and selection of gaskets in industrial applications. By defining key parameters and providing detailed testing procedures, the standard ensures that gaskets meet stringent performance requirements and contribute to the reduction of fugitive emissions. The adoption of leakage test standards enables industries to achieve optimal sealing performance, operational efficiency, and environmental sustainability. It is important to mention that no one standard covers all aspects of sealing, however combining EN 13555 with other common industry standards, for example, ASME B16.20 or proprietary methods on leader companies, the industry can confidently continue to prioritize environmental stewardship and regulatory compliance, these tests methodologies play a vital role in promoting the development of improved gaskets and enhancing the overall reliability and safety of industrial operations. By adhering to these standards, companies can confidently select and implement gaskets that provide reliable sealing, minimize leakage, and contribute to a greener and more sustainable future.