Among the various environmental concerns, the management of hazardous substances like Benzene, Toluene, Ethylbenzene, and Xylene (collectively known as BWON compounds) holds significant importance due to their potential adverse effects on human health and the environment. Achieving compliance with regulations regarding the management of BWON is not only a legal obligation but also a moral imperative for sustainable industrial practices.
In recent years, regulatory agencies in the United States have intensified their focus on mitigating BWON emissions from industrial facilities. As a result, companies are increasingly turning to gaskets and sealing technologies to mitigate the release of harmful contaminants.
The Benzene Waste Operations NE-SHAPs (National Emission Standards for Hazardous Air Pollutants) more commonly known as BWON, was promulgated in 1990 under the Clean Air Act (40 Code of Federal Regulations (CFR) Part 61, Subpart FF). The BWON standard was put in place to control benzene emissions from facility waste; it applies to petroleum refineries, chemical plants, coke by-product recovery facilities, and treatment, storage, and disposal facilities (TSDFs). TSDFs must only comply with this standard if they handle waste from one of the other facilities listed. BWON is a unique standard as it combines waste and wastewater quality management in an air standard for controlling benzene emissions.
The regulation (40 CFR Part 61, Sub-part FF) includes multiple subsections including applicability, waste & waste stream determination, compliance operations, point of waste generation, and treatment & equipment standards.
In recent years, regulatory agencies in the United States have intensified their focus on mitigating BWON emissions from industrial facilities. As a result, companies are increasingly turning to gaskets and sealing technologies to mitigate the release of harmful contaminants.
What is BWON
BWON compounds are commonly found in industrial processes such as petroleum refining, petrochemical production, chemical manufacturing, and paint production; they are known collectively for their toxicological properties. Benzene, for instance, is a known carcinogen and is associated with various health issues.The Benzene Waste Operations NE-SHAPs (National Emission Standards for Hazardous Air Pollutants) more commonly known as BWON, was promulgated in 1990 under the Clean Air Act (40 Code of Federal Regulations (CFR) Part 61, Subpart FF). The BWON standard was put in place to control benzene emissions from facility waste; it applies to petroleum refineries, chemical plants, coke by-product recovery facilities, and treatment, storage, and disposal facilities (TSDFs). TSDFs must only comply with this standard if they handle waste from one of the other facilities listed. BWON is a unique standard as it combines waste and wastewater quality management in an air standard for controlling benzene emissions.
The regulation (40 CFR Part 61, Sub-part FF) includes multiple subsections including applicability, waste & waste stream determination, compliance operations, point of waste generation, and treatment & equipment standards.
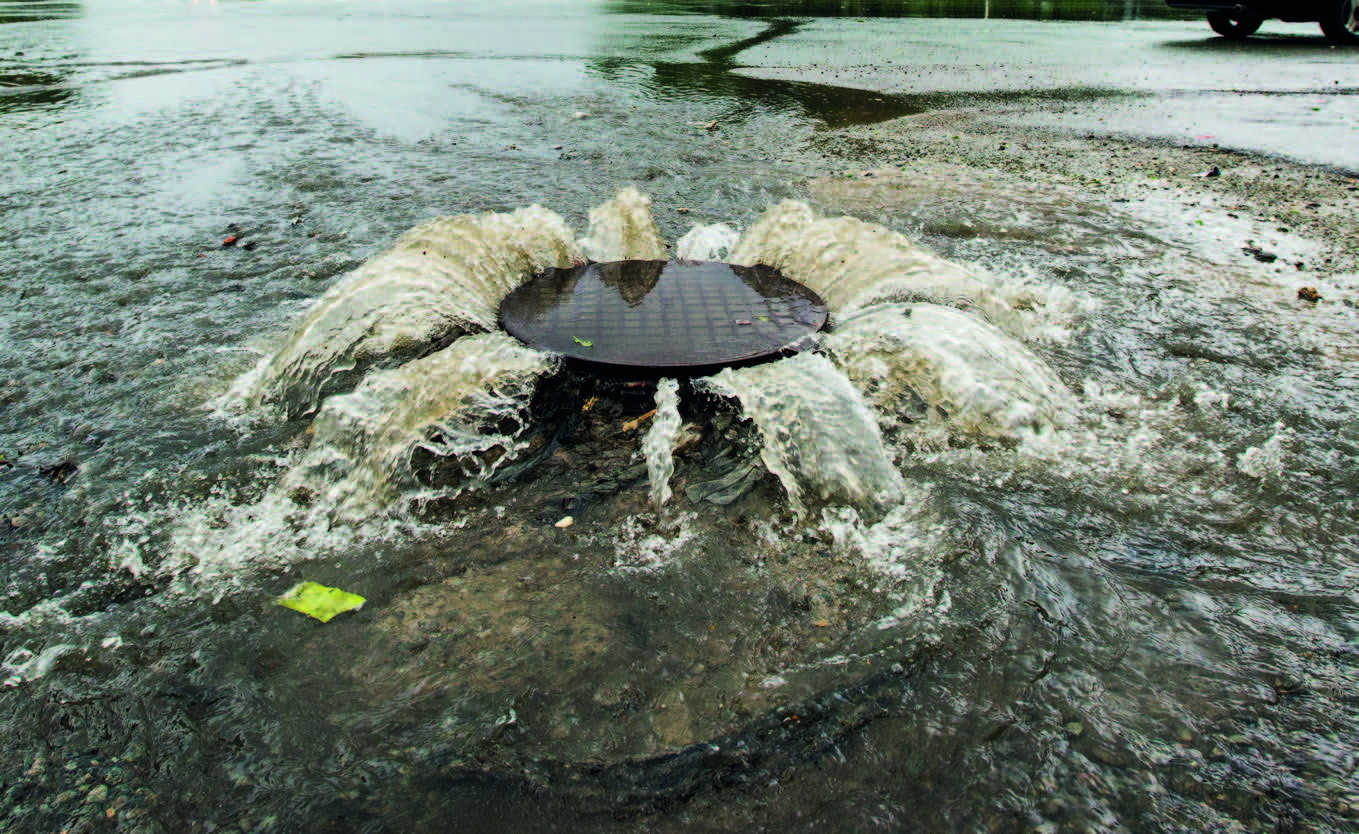
Ongoing Challenges
Recent Federal inspections of refinery and chemical facility BWON programs have found that many sources of un-permitted benzene emissions originate from facility Waste Management Units (WMUs). Leaks from equipment such as tanks, oil-water separators, and valves are common sources of unpermitted benzene emissions and can result in regulatory violations. The standard, in § 61.643-§ 61.347, § 61.349, expressly states that WMUs must be engineered to operate with No Detectable Emissions (NDE) as indicated by a detection instrument that reads less than 500 ppmv VOC above background.More precisely, the standard in each paragraph states: “The cover and all openings (e.g., access hatches, sampling ports, and gauge wells) shall be designed to operate with no detectable emissions as indicated by an instrument reading of less than 500 ppmv above background, as determined initially and thereafter at least once per year.”
The standard for closed-vent systems and control devices, §61.349, varies slightly, “The closed-vent system shall be designed to operate with no detectable emissions as indicated by an instrument reading of less than 500 ppmv above background, as determined initially and thereafter at least once per year.”
Compliance requirements for these standards are determined by a facility’s Total Annual Benzene (TAB) quantity. To calculate the TAB quantity for a waste stream, the annual waste quantity of the waste stream is multiplied by the flow weight, volume basis, and annual average benzene concentration (weight %) of the waste stream. The waste stream quantities will be calculated in mega-grams per year (Mg/yr); one (1) mega-gram is equivalent to one (1) metric ton.
BWON allows for two ways to determine the benzene concentration for a waste stream: through process knowledge or direct measurement. Therefore, the benzene quantity (BQ) of each waste stream is determined by estimating the stream’s annual benzene waste quantity.
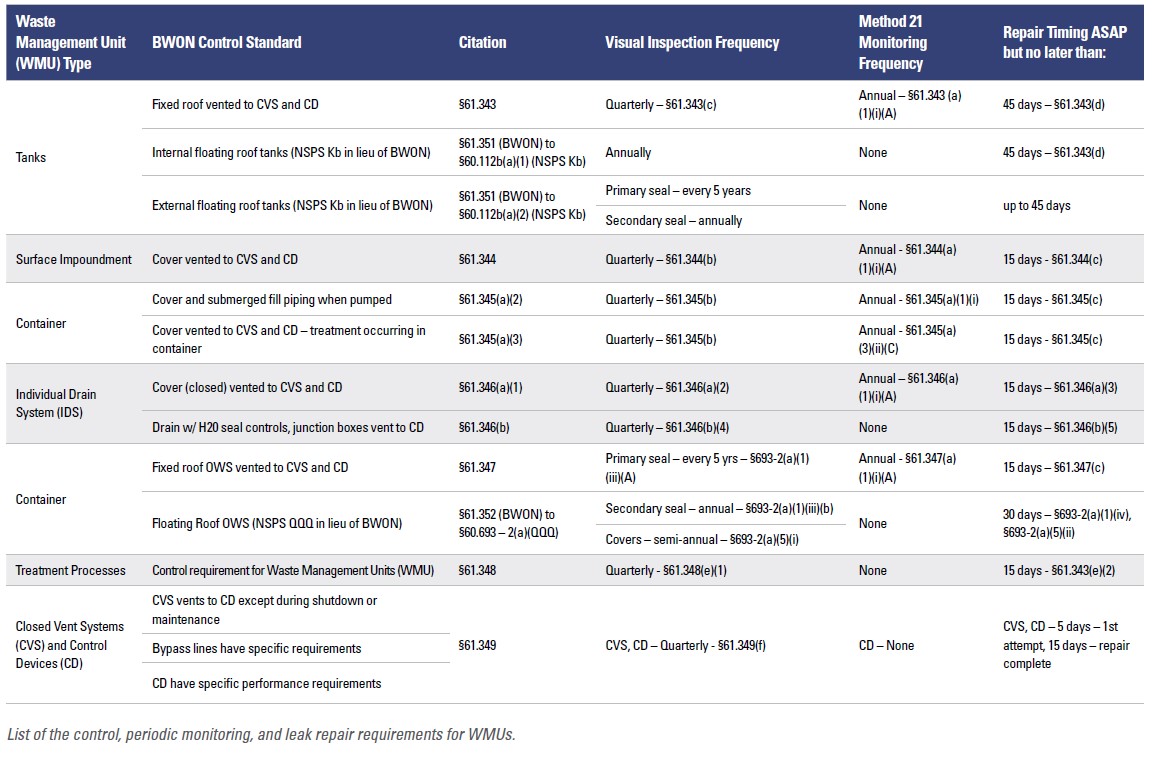
The objective is to ensure the waste quantity is representative; the oil and water fraction of the waste must be determined. There are vital thresholds that must be used when determining which streams are applicable and which are not. For example, waste streams that are <10% water are organic waste and all detectable emissions >500 ppmv must be timely mitigated (repaired).
It is important to note that most facilities will have a TAB greater than 10 Mg/yr and will require environmental controls on the equipment transporting process wastewater including the WMUs. This equipment is subject to no detectable emissions threshold and no detectable emissions monitoring standards as noted in §61.343 through §61.347 and §61.349. Unfortunately, current inspections continue to find sources emitting significantly higher emissions than 500 ppmv. It is therefore important to mitigate any risk of NDE with the appropriate assets.
The standard for closed-vent systems and control devices, §61.349, varies slightly, “The closed-vent system shall be designed to operate with no detectable emissions as indicated by an instrument reading of less than 500 ppmv above background, as determined initially and thereafter at least once per year.”
Compliance requirements for these standards are determined by a facility’s Total Annual Benzene (TAB) quantity. To calculate the TAB quantity for a waste stream, the annual waste quantity of the waste stream is multiplied by the flow weight, volume basis, and annual average benzene concentration (weight %) of the waste stream. The waste stream quantities will be calculated in mega-grams per year (Mg/yr); one (1) mega-gram is equivalent to one (1) metric ton.
BWON allows for two ways to determine the benzene concentration for a waste stream: through process knowledge or direct measurement. Therefore, the benzene quantity (BQ) of each waste stream is determined by estimating the stream’s annual benzene waste quantity.
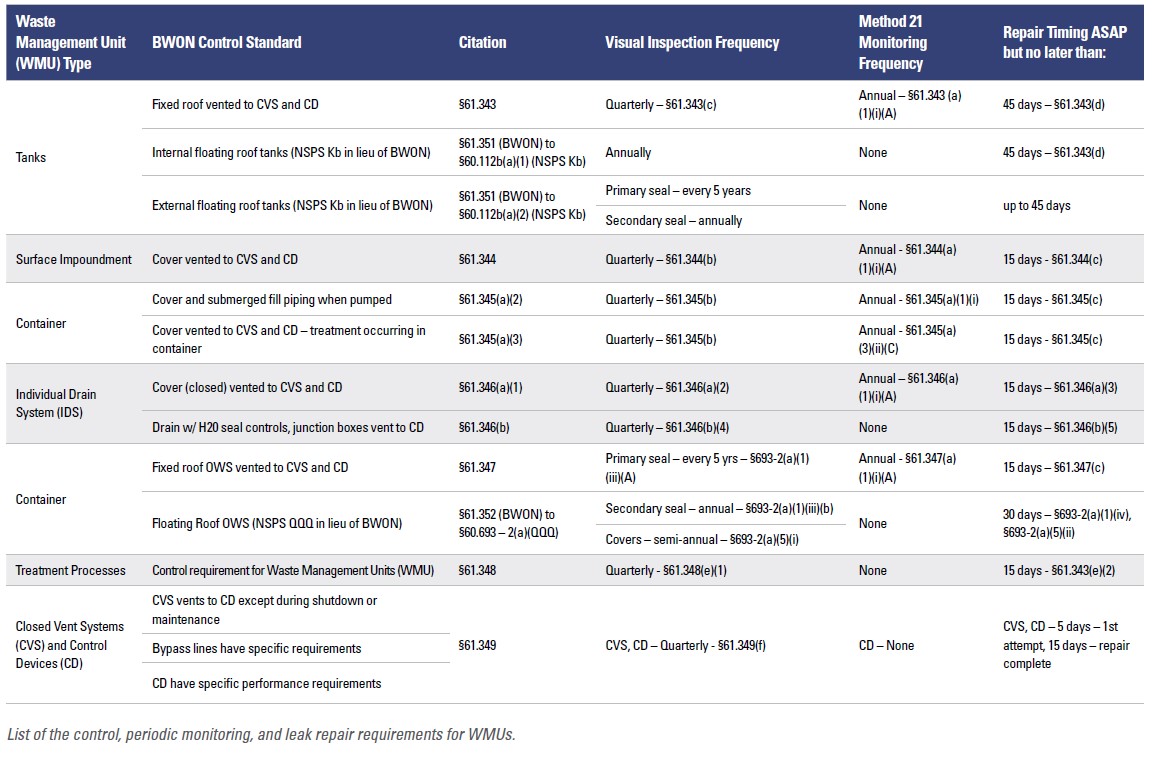
The objective is to ensure the waste quantity is representative; the oil and water fraction of the waste must be determined. There are vital thresholds that must be used when determining which streams are applicable and which are not. For example, waste streams that are <10% water are organic waste and all detectable emissions >500 ppmv must be timely mitigated (repaired).
Emission Control Options
Once the TAB is determined, the facility will fall within one of the three control options:- Facilities with a TAB greater than 10Mg/yr. These facilities are required to install environmental controls on their waste streams and WMU and submit quarterly and annual reports [§61.355(a)(3)].
- Facilities with a TAB less than 10 Mg/ yr but greater than 1 Mg/yr. These facilities are not required to install controls but must submit an annual TAB report and an updated report if the TAB goes above 10 Mg/yr [§61.355(a)(4)].
- Facilities with a TAB of less than 1 Mg/yr. These facilities are required to submit an initial TAB report and update the report if the TAB goes above 1 Mg/yr [§61.355(a)(5)].
It is important to note that most facilities will have a TAB greater than 10 Mg/yr and will require environmental controls on the equipment transporting process wastewater including the WMUs. This equipment is subject to no detectable emissions threshold and no detectable emissions monitoring standards as noted in §61.343 through §61.347 and §61.349. Unfortunately, current inspections continue to find sources emitting significantly higher emissions than 500 ppmv. It is therefore important to mitigate any risk of NDE with the appropriate assets.
Key Terms
With many complicated standards, it is essential to understand the key terms used in the regulation (40 CFR Part 61, SubpartFF) standard and throughout this article.- Waste – Any material resulting from industrial, commercial, mining, or agricultural operations, or from community activities that is discarded or is being accumulated, stored, or physically, chemically, thermally, or biologically treated before being discarded, recycled, or discharged.”
- Examples of waste include slop oil routed to slop tanks, spent caustics, sludge, DAF float sent offsite, pump drainages, lab wastes, and unit wash-down material.
- Waste Management Unit (WMU) – A piece of equipment, structure, or transport mechanism used in handling, storage, treatment, or disposal of waste.
- Examples of a WMU include a tank, surface impoundment, container, oil-water separators individual drain system, steam stripping unit, thin-film evaporation unit, waste incinerator, and landfill.
- Wastewater Treatment System (WTS) – Any component, piece of equipment, or installation that receives, manages, or treats process wastewater, product tank drawdown, or landfill leachate prior to direct or indirect discharge in accordance with the National Pollutant Discharge Elimination System permit regulations under 40 CFR part 122. These systems typically include Individual Drain Systems (IDS), Oil-Water Separators (OWS), air flotation units, equalization tanks, and biological treatment units.
- Waste Stream – The waste generated by a particular process unit, product tank, or WMU. The characteristics of the waste stream (e.g., flow rate, benzene concentration, water content) are determined at the point of waste Generation.
- Examples of a waste stream include process wastewater, product tank drawdown, sludge and slop oil removed from WMUs, and landfill leachate.
- Closed-vent system (CVS) – A system that is not open to the atmosphere and is composed of piping, ductwork, connections, and, if necessary, flow-inducing devices that transport gas or vapor from an emission source to a control device (CD).
- Container – Any portable WMU with a capacity greater than or equal to 0.1 cubic meters (26.4 gallons) in which a material is stored, transported, treated, or otherwise handled.
- Examples of containers are drums, barrels, tank trucks, barges, dumpsters, tank cars, dump trucks, and ships.
- Control device (CD) – An enclosed combustion device, vapor recovery system, or flare.
- Cover – A device or system which is placed on or over a waste placed in a WMU so that the entire Waste surface area is enclosed and sealed to minimize air emissions. A cover may have openings necessary for the operation, inspection, and maintenance of the WMU, such as access hatches, sampling ports, and gauge wells, provided that each opening is closed and sealed when not in use. Example of covers includes a fixed roof installed on a tank, a lid installed on a container, and an air-supported enclosure installed over a WMU.
- Individual Drain System (IDS) – The system used to convey waste from a processing unit, product storage tank, or WMU to another WMU. The term includes all process drains and common junction boxes, together with their associated sewer lines and other junction boxes, down to the receiving WMU.
- No Detectable Emissions (NDE) – Less than 500 parts per million by volume (ppmv) above background levels, as measured by a detection instrument reading in accordance with the procedures specified in § 61.355(h).
- Oil-Water Separator (OWS) – A WMU, generally a tank or surface impoundment, is used to separate oil from water. An OWS consists of not only the separation unit but also the forebay and other separator basins, skimmers, weirs, grit chambers, sludge hoppers, and bar screens that are located directly after the IDS and prior to additional treatment units such as an air flotation unit, clarifier, or biological treatment unit.
- Examples of an OWS include an API separator, parallel-plate interceptor, and corrugated plate interceptor (CPI) with the associated ancillary equipment.
- Point of Waste Generation (POG) – The location where the waste stream exits the process unit component or storage tank prior to handling or treatment in an operation that is not an integral part of the production process, or in the case of WMU that generate new Wastes after treatment, the location where the Waste stream exits the WMU component.
- Process Wastewater – Water that encounters benzene during manufacturing or processing operations conducted within a processing unit. Process wastewater is not organic waste, process fluids, product tank drawdown, cooling tower blowdown, stream trap condensate, or landfill leachate.
- Surface Impoundment – A WMU is a natural topographic depression, man-made excavation, or diked area formed primarily of earthen materials (although it may be lined with man-made materials), which is designed to hold an accumulation of liquid wastes or waste containing free liquids, and which is not an injection well.
- Examples of surface impoundments are holding, storage, settling, and aeration pits, ponds, and lagoons.
- Tank – A stationary WMU that is designed to contain an accumulation of waste and is constructed primarily of non-earthen materials (e.g., wood, concrete, steel, plastic) that provide structural support.
- Total Annual Benzene (TAB) – The sum of the annual benzene quantity for each waste stream at the facility that has a flow-weighted, volume basis, annual average water content greater than 10% or that is mixed with water (or other waste), at any time, and the mixture has an annual average water content greater than 10%.”
- Treatment Process – A stream stripping unit, thin-film evaporation unit, waste incinerator, or any other process used to comply with § 61.348.
Achieving Compliance
There are currently two primary methods used to improve compliance with the NDE control standards for WMUs. The first is to use reliable, low-emission gaskets. The second is to use an optical gas imaging camera to identify detectable emissions around all seams, seals, covers, and openings on WMUs.Low-emission gaskets and packing offer several advantages over traditional materials. They are specifically formulated to withstand environments commonly found in industrial processes, ensuring long-term performance and reliability. Additionally, these materials are compliant with environmental regulations and standards, providing peace of mind for facility operators and regulators alike.
In addition to their environmental benefits, low-emission gaskets can lead to cost savings for industrial facilities. By reducing the frequency and severity of leaks, these materials help minimize downtime, maintenance costs, and potential fines associated with regulatory non-compliance. Furthermore, the long service life of low-emission gaskets translates to lower overall lifecycle costs for facilities.
Implementing low-emission sealing products as part of an integrated emissions reduction strategy can help industrial facilities achieve and maintain compliance with BWON and NSPS regulations. However, companies need to consider other factors, such as proper installation, maintenance, and monitoring practices, to ensure the effectiveness of these materials in reducing emissions.
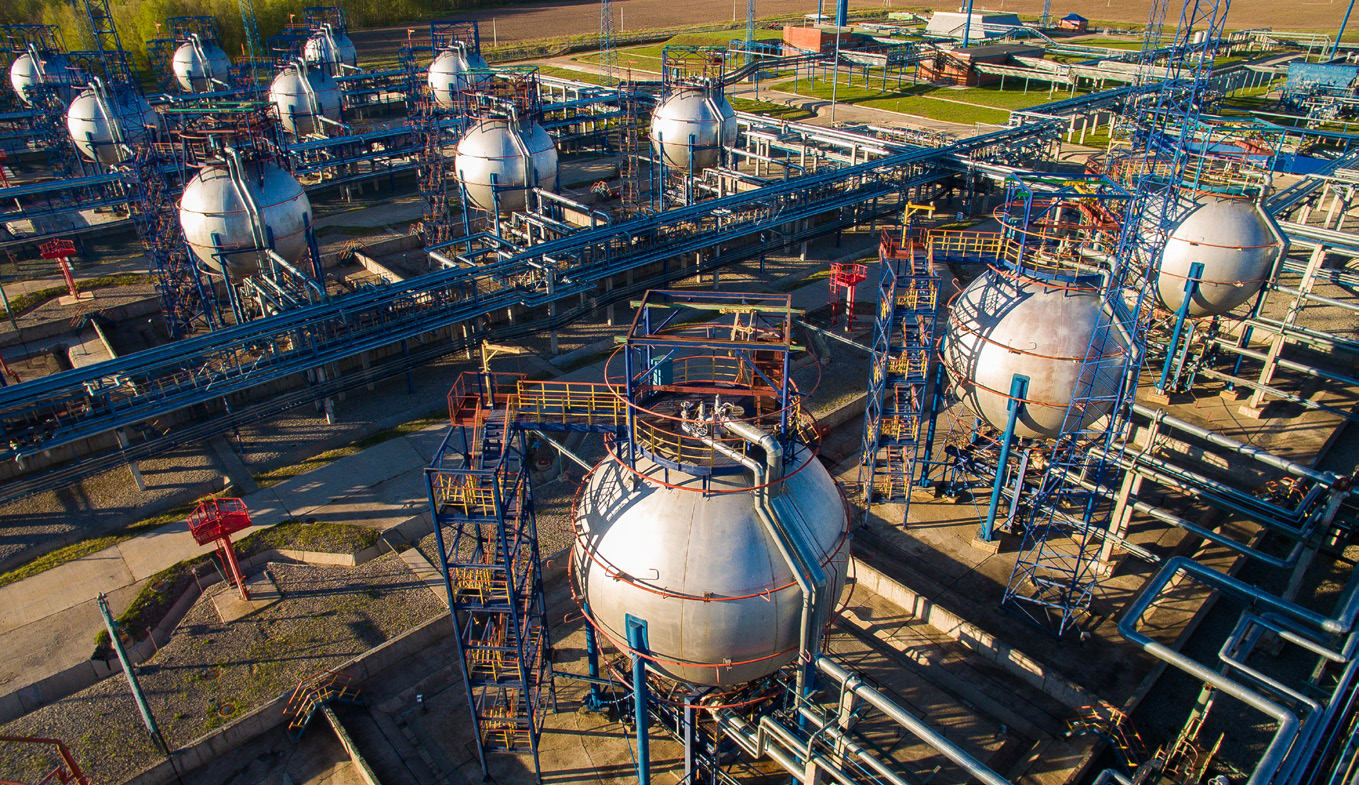
Moving Forward
Recent legal actions, such as consent decrees against industrial facilities, underscore the intricacies of emissions management and emphasize the necessity of proactive measures to mitigate environmental impacts. These consent decrees represent significant milestones in environmental enforcement, requiring companies to implement comprehensive measures to reduce emissions and enhance compliance.Key components of these decrees typically include upgrading pollution control equipment, adopting advanced monitoring technologies, and investing in community outreach and education initiatives. Proactive emissions management, including real-time monitoring and rigorous leak detection protocols, is a cornerstone of consent decrees, emphasizing the importance of identifying and mitigating sources of emissions promptly.
Low-emission gaskets, packing, and sealing solutions play a critical role in reducing benzene emissions and ensuring compliance with BWON and NSPS regulations. By investing in these specialized materials and adopting best practices in emissions management, industrial facilities can protect public health, minimize environmental impact, and achieve long-term sustainability. Additionally, embracing lessons from consent decrees against industrial facilities can provide valuable insights into proactive emissions management and community engagement, ultimately contributing to a cleaner, healthier environment for all.
Low-emission gaskets, packing, and sealing solutions play a critical role in reducing benzene emissions and ensuring compliance with BWON and NSPS regulations. By investing in these specialized materials and adopting best practices in emissions management, industrial facilities can protect public health, minimize environmental impact, and achieve long-term sustainability. Additionally, embracing lessons from consent decrees against industrial facilities can provide valuable insights into proactive emissions management and community engagement, ultimately contributing to a cleaner, healthier environment for all.