How reverse engineering technology can enhance reliability and minimize downtime.
In the realm of industrial pumps, sealing discussions typically center around mechanical seals. At times, the conversation broadens to compare mechanical seals with alternative packing solutions, evaluating their respective merits. However, a crucial yet frequently overlooked seal is the flange gasket, which seals the connection between the pump and the piping systems, as well as the internal chambers of the pump or compressor.
Gaskets are crucial in preventing leakage and maintaining pressure within the pump. Recognizing the unique challenges of flange gaskets and adopting advanced solutions can mitigate the risk of unplanned downtime and pump failures.
Understanding the distinctions between gaskets and other sealing devices, such as mechanical seals and gland packings, is essential for effective pump maintenance and leak prevention. Mechanical seals and gland packings are specifically designed for pump areas that need to contain fluid while accommodating the movement of a rotating shaft.
Gland packing, a rope-like material, is cut into rings and wrapped around the shaft sleeve, while mechanical seals allow the rotating shaft to pass through a stationary housing to ensure the pump’s ‘wet’ area remains lubricated without allowing fluid to escape.
In contrast, gaskets are typically employed in stationary applications, serving as a sealing element between parts that are in contact but do not move relative to each other.
Permitting any of these conditions to continue will inevitably result in gasket failure. Regular inspection and timely replacement of flange gaskets can streamline maintenance schedules. Engineers incorporating gasket checks into their routine maintenance plans can prevent minor issues from escalating into major problems.
Reverse engineering facilitates the development of gaskets tailored to the pumping system's specific requirements. This approach is particularly valuable in cases where the original manufacturer no longer produces a specific gasket or when the gasket is unique to a particular process. Modern technologies enable specialized gasket manufacturers to address this challenge efficiently.
By capturing an image of the existing gasket or flange, manufacturers can generate precise schematics, allowing for the accurate recreation of gaskets that meet the exact specifications of the application. With this technology, the absence of assembly drawings and precise measurements is no longer a significant challenge for creating the needed gasket.
While various methods exist, one applicable example is to laser scan a sample gasket using a scanning tool, as seen in Image 1. This allows a digital file to be created that can be imported into typical manufacturing programs. The replacement gasket can then be produced, and a file can be stored for future manufacturing as required. This approach reduces lead times and allows for preordering in anticipation of planned maintenance.
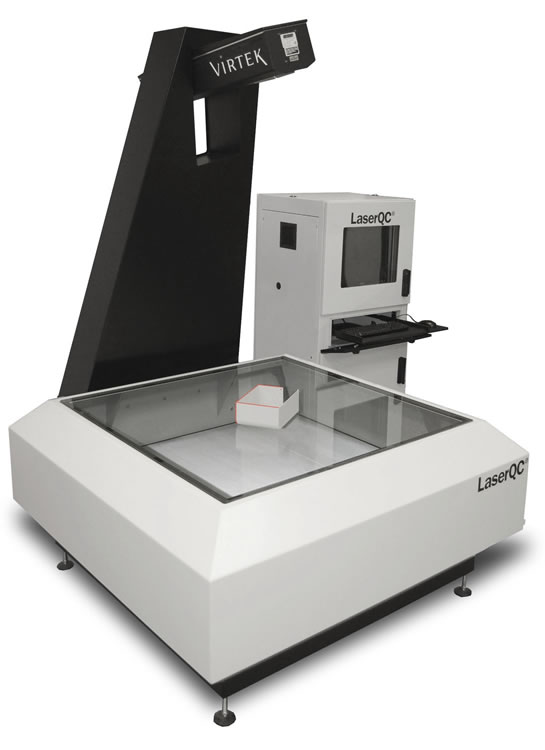
The first step in executing this type of process is the receipt of a gasket or an image of the gasket with atypical geometry, as seen in Images 2 and 3. Instead of trying to measure all the curves and radii, the gaskets can be placed on the scanner and digitally scanned. The output is then imported into manufacturing computer-aided design (CAD) software to produce manufacturing drawings, as shown in images 4 and 5.
By Angelica Pajkovic & Dale Norman, Teadit
In the realm of industrial pumps, sealing discussions typically center around mechanical seals. At times, the conversation broadens to compare mechanical seals with alternative packing solutions, evaluating their respective merits. However, a crucial yet frequently overlooked seal is the flange gasket, which seals the connection between the pump and the piping systems, as well as the internal chambers of the pump or compressor.
Gaskets are crucial in preventing leakage and maintaining pressure within the pump. Recognizing the unique challenges of flange gaskets and adopting advanced solutions can mitigate the risk of unplanned downtime and pump failures.
Understanding the distinctions between gaskets and other sealing devices, such as mechanical seals and gland packings, is essential for effective pump maintenance and leak prevention. Mechanical seals and gland packings are specifically designed for pump areas that need to contain fluid while accommodating the movement of a rotating shaft.
Gland packing, a rope-like material, is cut into rings and wrapped around the shaft sleeve, while mechanical seals allow the rotating shaft to pass through a stationary housing to ensure the pump’s ‘wet’ area remains lubricated without allowing fluid to escape.
In contrast, gaskets are typically employed in stationary applications, serving as a sealing element between parts that are in contact but do not move relative to each other.
Flange Gasket Properties
Flange gaskets are often considered a secondary concern, but overlooking their importance can lead to operational challenges. The geometry of the internal pump gaskets can be complex, leading to the need for custom gasket solutions, especially when keeping older equipment working in a situation where OEM parts are not an option. For pump maintenance engineers and end users, understanding and addressing the unique challenges of flange gaskets and where to find solutions can impact the asset's efficiency and longevity.Risks of Overlooking Gaskets
A flange gasket seal failure can result in downtime, environmental risks and potential damage to a pump system. As such, maintaining the integrity of these gaskets is of the utmost importance, necessitating regular inspections to identify and mitigate any conditions that may lead to gasket failure. The following conditions should be carefully monitored:Extreme temperatures
Pumps often operate under extreme conditions, with high pressure and temperature fluctuations. These environments can cause gaskets to degrade over time, leading to leaks and potential system failures.Irregular flange surface
Flange misalignment or surface irregularities can create uneven stress on the gasket, leading to sealing failures. This issue is common in systems that undergo frequent assembly and disassembly or where flange mating is not precise.Vibration and mechanical stress
Pumps are often subject to vibrations and mechanical stresses that can loosen the flange connections or degrade the gasket material over time, leading to leaks.Chemical compatibility
Industrial pumps are often required to process a variety of aggressive or abrasive media. The gasket must be compatible with chemicals, slurry and other potentially hazardous materials to prevent degradation and ensure a reliable seal.Permitting any of these conditions to continue will inevitably result in gasket failure. Regular inspection and timely replacement of flange gaskets can streamline maintenance schedules. Engineers incorporating gasket checks into their routine maintenance plans can prevent minor issues from escalating into major problems.
A Case for Reverse Engineering
When gasket replacement is necessary and standard gaskets are inadequate, reverse engineering customized flange gaskets can mitigate the risk of unplanned downtime and substantial losses.Reverse engineering facilitates the development of gaskets tailored to the pumping system's specific requirements. This approach is particularly valuable in cases where the original manufacturer no longer produces a specific gasket or when the gasket is unique to a particular process. Modern technologies enable specialized gasket manufacturers to address this challenge efficiently.
By capturing an image of the existing gasket or flange, manufacturers can generate precise schematics, allowing for the accurate recreation of gaskets that meet the exact specifications of the application. With this technology, the absence of assembly drawings and precise measurements is no longer a significant challenge for creating the needed gasket.
While various methods exist, one applicable example is to laser scan a sample gasket using a scanning tool, as seen in Image 1. This allows a digital file to be created that can be imported into typical manufacturing programs. The replacement gasket can then be produced, and a file can be stored for future manufacturing as required. This approach reduces lead times and allows for preordering in anticipation of planned maintenance.
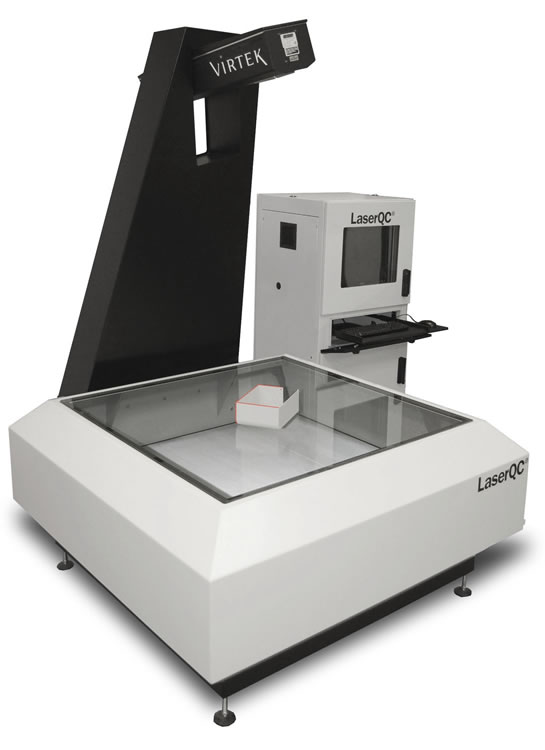
Image 1: Example of a scanning tool (Images courtesy of Teadit)
The first step in executing this type of process is the receipt of a gasket or an image of the gasket with atypical geometry, as seen in Images 2 and 3. Instead of trying to measure all the curves and radii, the gaskets can be placed on the scanner and digitally scanned. The output is then imported into manufacturing computer-aided design (CAD) software to produce manufacturing drawings, as shown in images 4 and 5.
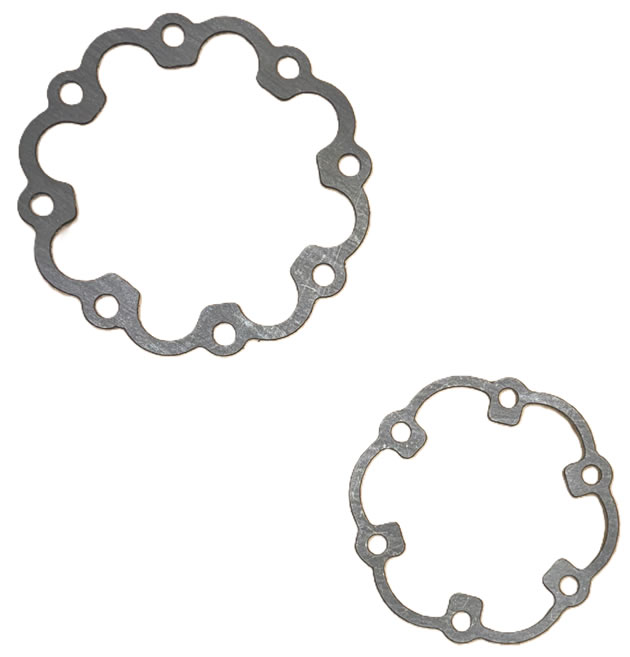
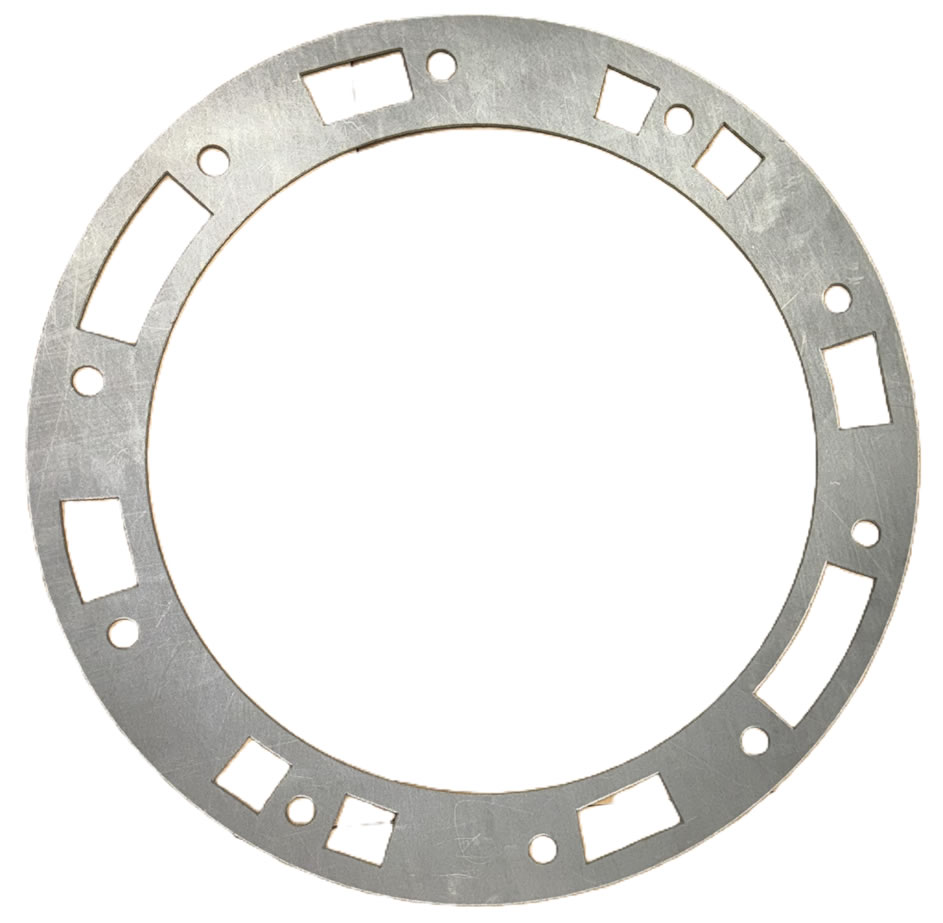
Images 2 and 3: Examples of atypical geometry gaskets
This provides the geometry for the required gasket, while the materials to be used are either determined by the sample gasket or the conditions of operations (temperature, media, pressure, etc.).
This provides the geometry for the required gasket, while the materials to be used are either determined by the sample gasket or the conditions of operations (temperature, media, pressure, etc.).
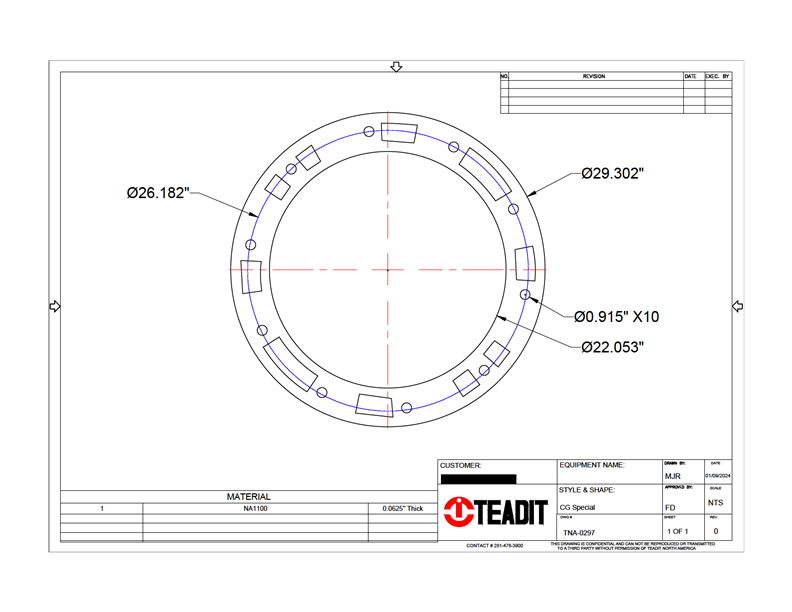
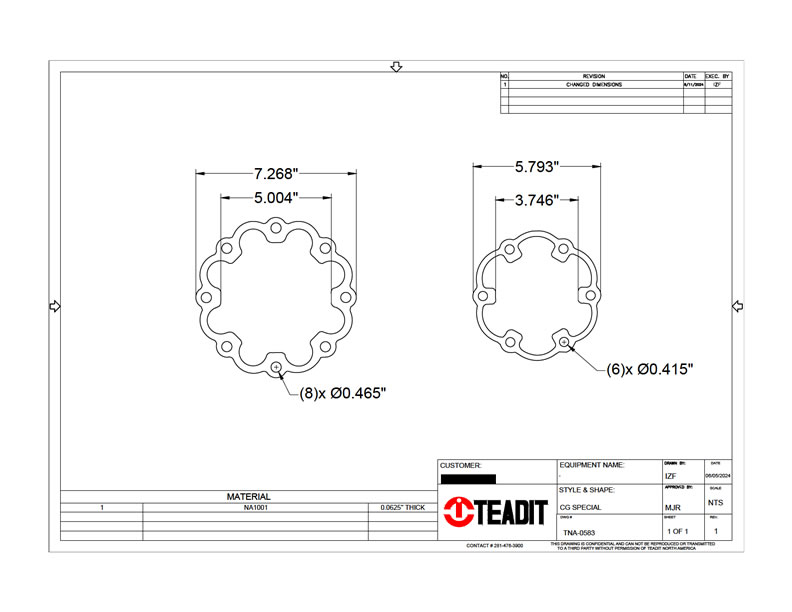
Images 4 and 5: Examples of schematic drawings. These drawings are then used to create the physical gasket.
In addition to replicating parts for fabrication, the newly produced schematics can help operators better understand how parts function.
The replication of these hard-to-source gaskets ensures the pump system remains operational without the need for extensive modifications, reduces the lead time for the product from days or weeks to mere hours and ultimately minimizes downtime and restores the pump system's functionality.
For maintenance engineers and end users, addressing the challenges associated with flange gaskets is not just a matter of routine—it is a strategic priority that can safeguard equipment, protect investments and ensure smooth, uninterrupted operations.
Modern advancements in gasket technology offer solutions tailored to the specific demands of pump systems. High-performance materials, such as those used in spiral wound gaskets or expanded polytetrafluoroethylene (PTFE) gaskets, provide improved sealing capabilities, even under extreme temperatures and pressures, while advanced scanning programs provide tailored solutions when the standard gasket does not provide an adequate seal.
By recognizing the importance of flange gaskets and adopting these advanced solutions, pump maintenance engineers can enhance the reliability of their systems, minimize downtime and ensure the safety and efficiency of their operations. Giving flange gaskets the attention they deserve is not just good practice—it is essential for long-term success.