In the highly specialized environment of nitrogen facilities, leak prevention and equipment integrity are paramount. Nitrogen, while non-toxic, is an asphyxiant that displaces oxygen, making small leaks potentially life-threatening for personnel in confined spaces or enclosed areas. Additionally, facility efficiency and integrity are significant concerns, as nitrogen leaks can impact process stability and lead to eventual equipment degradation.
Providing custom solutions to address unique flange sealing challenges is vital to ensuring safe operations. When given complex operating conditions and stringent regulatory requirements, a gasket manufacturing company was able to deliver solutions that delivered robust performance, ensuring safety and efficiency for critical nitrogen applications.
Initially, a spiral wound gasket was used in the application, but concerns arose re-garding the long-term compatibility of this gasket type with the facility’s nitro-gen-based processes.
The facility management, therefore, grew concerned that the corroded flanges could lead to compromised seal-ing performance. Upon inspection, the corrosion was deemed severe enough that maintenance personnel decided to replace the entire flange to prevent potential leaks. As replacing flanges is costly and time-consuming, the facility required a solution that could seal directly at the bore of the flange and increase the long-term reliability and safety of the process.
Providing custom solutions to address unique flange sealing challenges is vital to ensuring safe operations. When given complex operating conditions and stringent regulatory requirements, a gasket manufacturing company was able to deliver solutions that delivered robust performance, ensuring safety and efficiency for critical nitrogen applications.
The Challenge
A nitrogen facility encountered recur-ring issues with corrosion of flange faces due to chemical exposure and pressure conditions. Upon disassembling the flanges, the maintenance personnel ob-served significant pitting on the raised face portions of the thermowell flange connections.Initially, a spiral wound gasket was used in the application, but concerns arose re-garding the long-term compatibility of this gasket type with the facility’s nitro-gen-based processes.
Problem Identification
The original spiral wound gasket was found to be insufficient for use in the nitrogen processing system. While the gasket winding sealed sufficiently to prevent a leak, the metal inner ring left a small void near the inside diameter of the flange exposed to the media. This unsealed area allowed the media to ac-cumulate on the flange face. The stag-nant media began pitting the faces of the flange, causing corrosion between the flange bore and the inside diameter of the gasket winding.The facility management, therefore, grew concerned that the corroded flanges could lead to compromised seal-ing performance. Upon inspection, the corrosion was deemed severe enough that maintenance personnel decided to replace the entire flange to prevent potential leaks. As replacing flanges is costly and time-consuming, the facility required a solution that could seal directly at the bore of the flange and increase the long-term reliability and safety of the process.
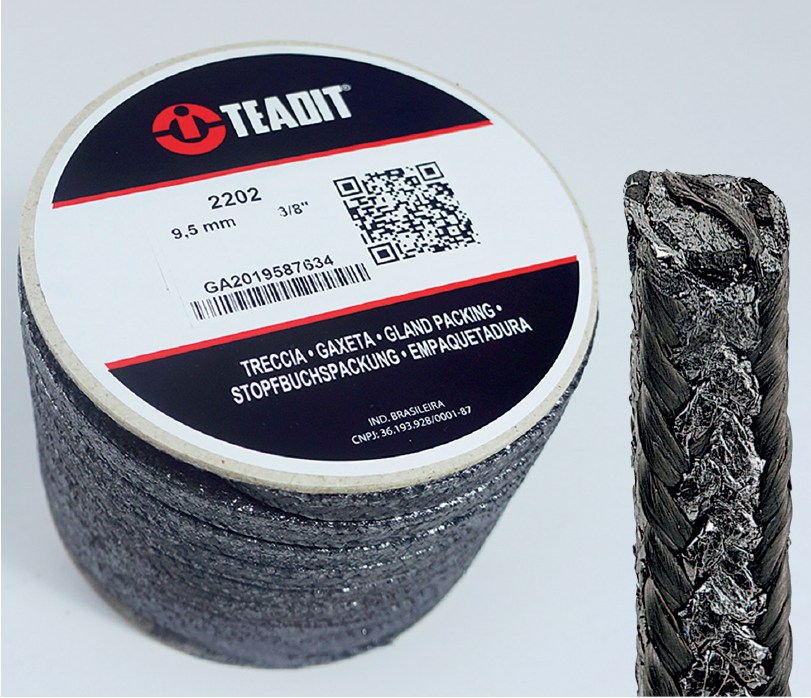
Solution Driven Approach
The manufacturer’s engineering team conducted a comprehensive root-cause analysis to understand the full extent of the issue. Based on the findings, it was determined that a unique dual-sealing system would provide a more robust solution. This approach involved replacing the original spiral-wound gasket with a double-rail camprofile gasket. To prevent media buildup at the bore of the flange, a layer of compressible mechanical packing (Teadit 2202) was also installed.1. Dual Sealing System: The manufacturer’s gasket design consisted of a 321ss core manufactured with two serrated, concentric sealing rings. This construction allowed for reliable sealing at the bore, eliminating any space where media could accumulate and cause corrosion, while simultaneously providing external leak-free sealing.
2. Packing Solution for Shaft Protection: To further secure the connection and minimize media exposure to sensitive components, the manufacturer provided a packing solution that was installed around the conical shaft within the thermowell.
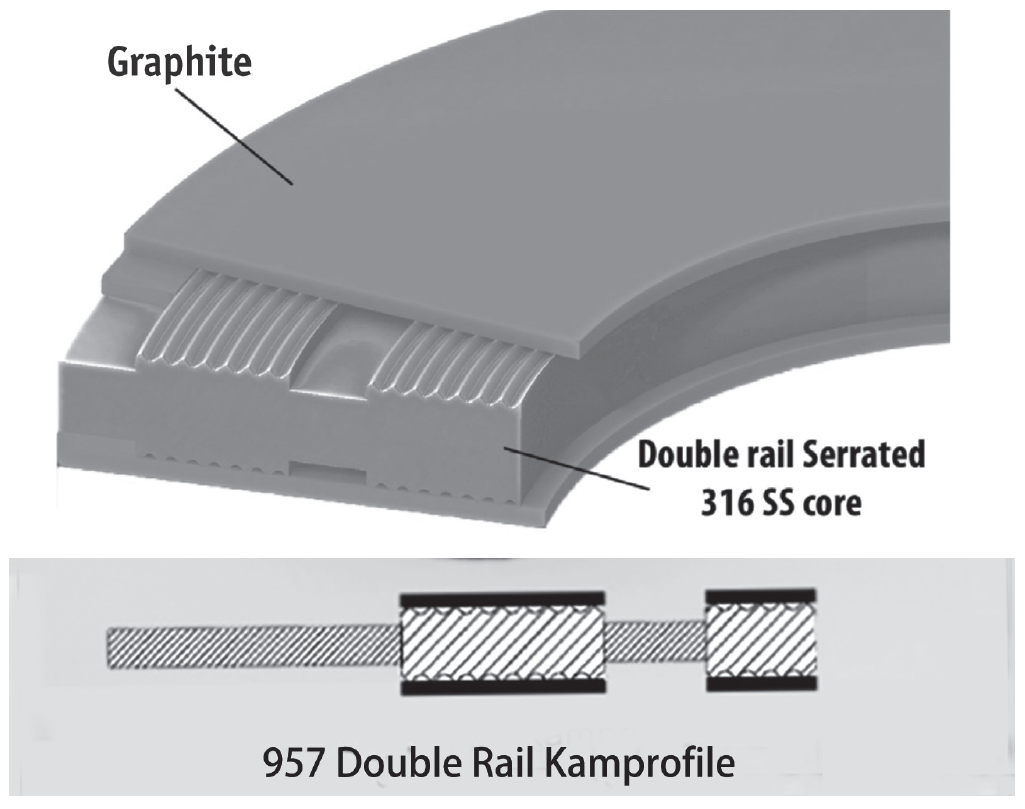
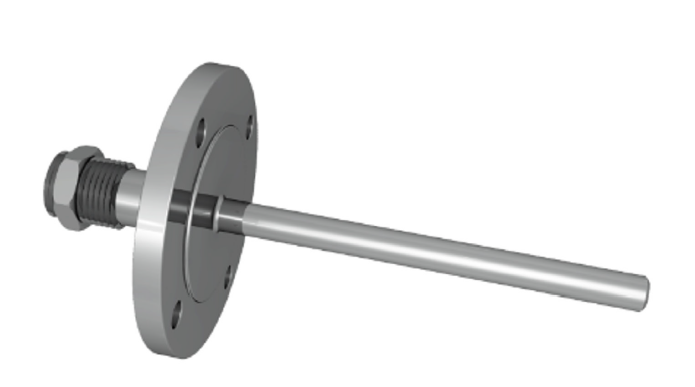
The company’s innovative packing style was selected and sized to create an interference fit, which offered additional protection for the shaft and aided in the prevention of media accumulating in the thermowell. The packing style was recommended becauseof the combined benefits of high compressibility and extrusion resistance.
As the braid is constructed with pure expanded graphite, it can expand radially and seal effectively against the shaft. The carbon fiber reinforcement drastically increased the packing’s ability to withstand pressure and not extrude.
As the braid is constructed with pure expanded graphite, it can expand radially and seal effectively against the shaft. The carbon fiber reinforcement drastically increased the packing’s ability to withstand pressure and not extrude.
Implementation and Results
After replacing the original gasket with the specialized gasket, and adding the packing around the shaft, the nitrogen facility reported a marked reduction in corrosion during subsequent inspections. The dual-sealing system ensured a more reliable seal and provided an added layer of protection for the components by preventing media from reaching areas prone to pitting.Key benefits of the new solution included:
- Enhanced Corrosion Resistance: By sealing directly at the flange bore and adding packing at vulnerable points, the solution prevented media from stagnating within the flange face.
- Extended Maintenance Cycles: With reduced corrosion, the facility no longer needed to replace pitted flanges during planned maintenance events. As the replacement process can involve cutting the flange to remove the damaged gasket, re-welding it once the new gasket is installed, and performing a hydro test, this solution significantly reduces downtime and cost.