In recent years, there has been a growing concern surrounding the presence of Per- and Polyfluoroalkyl Substances (PFAS) in the environment and their potential impacts. PFAS are a group of over 4500 synthetic chemicals widely used in various industrial and consumer products due to their unique properties, including water and oil repellency, as well as heat and chemical resistance. However, their persistent nature and widespread use have led to their ubiquitous presence in the environment, posing significant challenges for mitigation and remediation efforts.
These concerns have forced significant discussion on how best to proceed with the use of PFAS, including the use of distinct groups of compounds such as Polytetrafluoroethylene (PTFE), which in turn has prompted the question of what the world would look like without them.
Challenges of PFAS
PFAS are unique compounds due to their remarkable stability. The nature of the compound allows them to persist in the environment for extended periods without breaking down. While this trait is ideal for numerous applications, its persistence may pose potential environmental threats.One of the primary concerns associated with PFAS exposure is the adverse effects on human health some of them may cause. Studies have linked certain PFAS exposure to various health issues, especially in vulnerable populations, such as pregnant women, infants, and individuals with compromised immune systems. Nevertheless, these studies are limited and only address a small number of the chemicals classified under the PFAS definition.
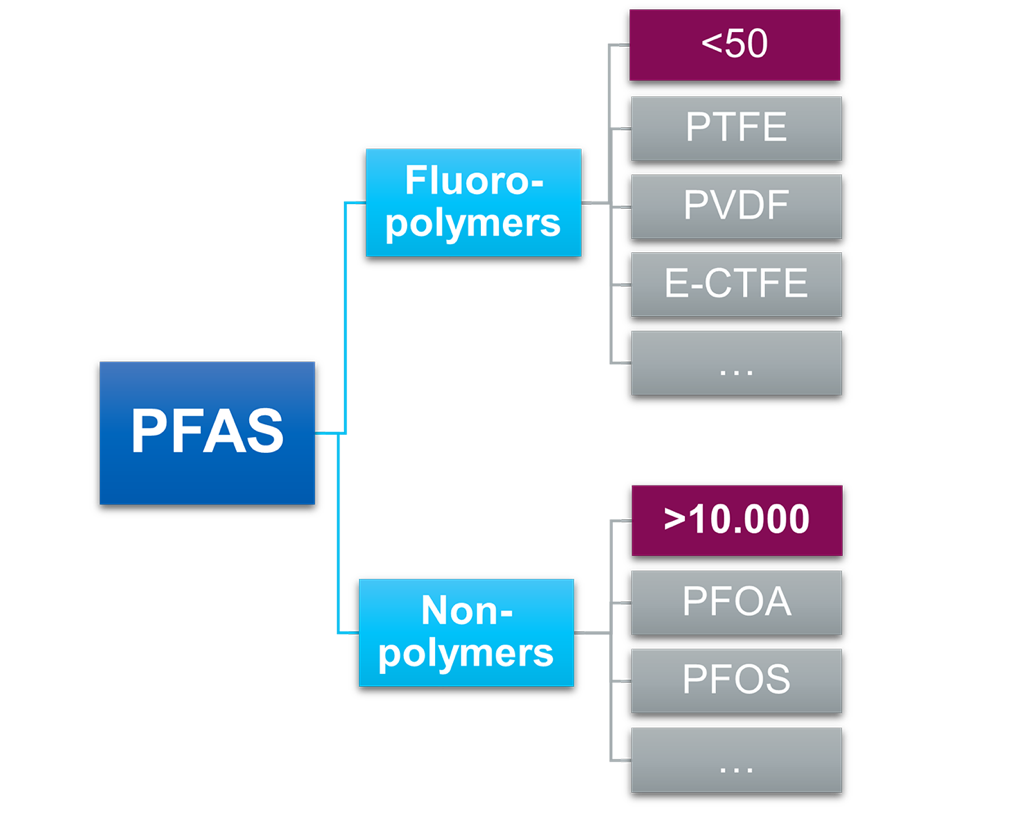
Distinguishing PFAS
PFAS chemicals can be divided into two main categories: Non-polymers and polymers. Among the non-polymers, PFOA (perfluorooctanoic acid) and PFOS (perfluorooctanoic sulfonate) stand out as primary concerns and have undergone extensive study. These substances exhibit bio-persistence and have been detected in water supplies, soil, and living organisms. Their widespread presencehas fueled legislative efforts aimed at regulating PFAS.
Among polymers, PTFE is perhaps the most notable group. In general, all fluoropolymers are grouped as PFAS within the (new) Organization for Economic Cooperation and Development (OECD) definition of PFAS, however, multiple studies and trade organizations consider these compounds to be a distinct group of PFAS. For example, PTFE’s unique nature currently meets the accepted regulatory assessment criteria of PLCs (Polymers of Low Concern). PTFE itself is nontoxic, not bioavailable, not water soluble and has nonmobile molecules; therefore, it is considered low risk to human health and the environment.
Commonly known by the E.I. DuPont de Nemours and Company’s trademarked brand name of Teflon, PTFE has long been regarded for its ability to serve as an effective, versatile solution in various industries. It has been commonly used as a graft material in surgery, as a coating on catheters, as well as a lubricant for valve stem packings. As it is one of the most chemically resistance materials on earth and has one of the lowest known coefficients of friction, it is also an ideal choice for sealing applications. Its industrial use can reduce friction, wear and energy consumption in several applications that have no other technically available PTFE substitutes today.
Properly addressing the PFAS problem requires a multifaceted approach that encompasses regulation, remediation and research efforts. In recent years, there has been a growing recognition of the need for stricter regulations to limit the use and release of certain PFAS into the environment. Several countries and regions have implemented or proposed regulations to restrict the use of PFAS in certain products and to regulate their environmental discharge.2 Additionally, there is a growing emphasis on remediation strategies to mitigate PFAS contamination in soil and water. However, regulating all PFAS under the same umbrella might not be the best approach.
Most fluoropolymer applications are considered by many as essential to day-to-day life; they are necessary to maintain the current standard of living and are also being used to abate ongoing fugitive emissions. PTFE, along with other polymer compounds, are currently classified in the same group as other noticeably harmful PFAS. This classification is based primarily on the basic definition of what qualifies as a PFAS. The fact that PTFE has however been deemed a PLC, provides insight into why many individuals are having difficulties gaining a good grasp on the PFAS problem.
Why It Is So Complicated
Understanding that there are significant variances between the various PFAS compounds, and that grouping them all in one class does not allow the consequences of their use to be accurately represented, can shed some light on some of the current challenges individuals are facing when it comes to understanding the PFAS problem.Envisioning a world without PTFE as a sealing material prompts a closer examination of the potential implications and challenges that would arise in such a scenario.
One immediate consequence of the absence of PTFE would be the effect it would have on industrial applications. To start, it could effectively put an end to most hydrogen projects. PTFE seals play a vital role in electrolysis, providing the necessary protection to the components exposed to high temperatures and corrosive chemicals.
In the valve industry, for example, it is utilized for resilient (soft) seated valve designs to provide chemical resistance and enhance closure performance. PTFE-lined valves can be found in highly corrosive applications, PTFE gaskets are found in chemical plants, PTFE-coated bolts are used for harsh atmospheric conditions and PTFE lubricants are utilized in the nuclear industry.
From an environmental perspective, the elimination of PTFE would have an impact on the recent implementation of Certified Low Leak Technology (CLLT). CLLT packing refers to a valve stem seal (packing) design that will not exceed a 100-ppm fugitive emission threshold for a minimum of five years as defined in various EPA consent decrees. The implementation of CLLT packing by the EPA was a result of years of data estimating that 60% of all fugitive emissions could be attributed to valve stem seals or packing.4
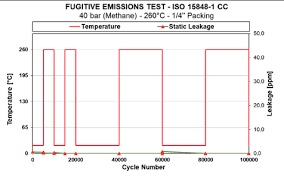
Special attention can also be given to the utilization of PTFE in sealing applications within the transport vehicle industry, particularly in environments with cryogenic temperatures. Cryogenic temperatures, often denoted by temperatures near or below the freezing point of liquid nitrogen (-196°C), pose a notable challenge to material durability. Demonstrating high strength, toughness, and self-lubrication even at low temperatures, PTFE remains operational within a temperature range from -268°C to 260°C, as documented in the "Teflon PTFE – Properties Handbook." Maintaining flexibility at extremely low temperatures is crucial for PTFE, as it ensures the effectiveness of seals in cryogenic conditions.
Beyond specific applications, the absence of PTFE as a sealing solution would have broader implications for the chemical and petrochemical industries, product design, manufacturing processes and supply chains.
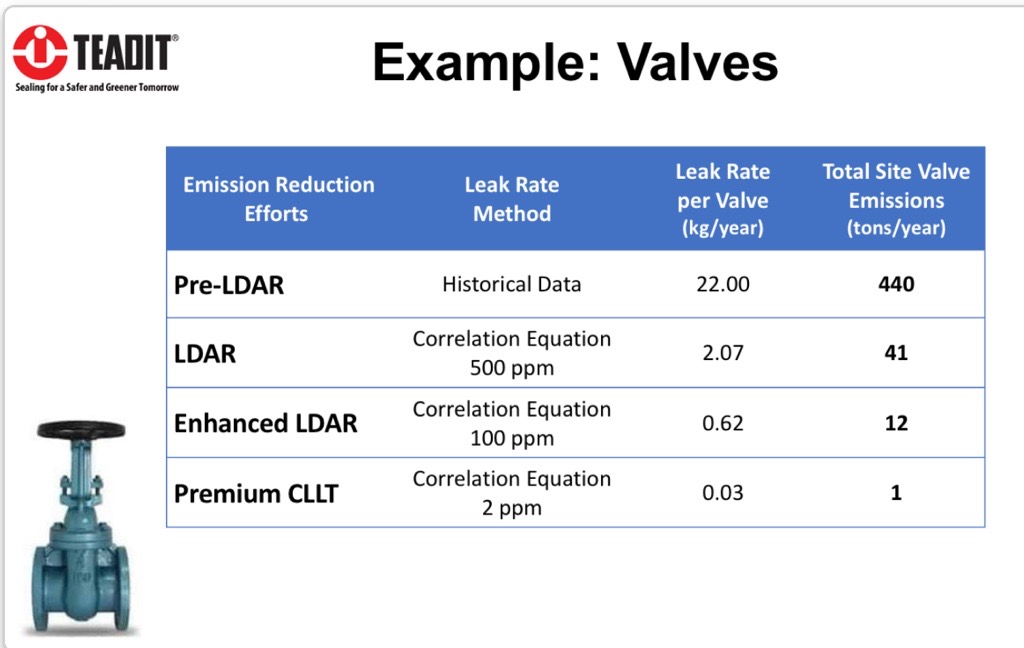
Looking Forward
Research efforts are underway to better understand the fate and transport of PFAS in the environment, as well as their potential health impacts. This includes studying the mechanisms of specific PFAS bioaccumulation in organisms, assessing the long-term effects of low-dose exposure, and exploring alternative chemicals and materials that can replace PFAS in various applications. It also includes determining suitable criteria to use to accurately classify each subset compound and how it should be regulated.While it may seem like a simple matter of eliminating the use of PFAS, the PFAS problem represents a complex and multifaceted challenge that requires coordinated efforts from government agencies, industry stakeholders, researchers, and the public. Progress has been made in understanding and addressing some PFAS contamination, but much work remains to be done to effectively mitigate its impacts and ensure that the decisions made will not adversely impact other important initiatives such as mitigation of fugitive emissions and reduction of greenhouse gas emissions.
References
https://search.epa.gov/epasearch/?querytext=pfas&areaname=&areacontacts=&areasearchurl=&typeofsearch=epa&result_template=#/https://www.anthesisgroup.com/regulations-hub/pfas/#:~:text=On%20February%207%2C%202023%2C%20Denmark,ban%20on%20all%20PFAS%20chemicals.https://pfas-1.itrcweb.org/wp-content/uploads/2020/10/treatment_tech_508_Aug-2020-Final.pdfhttps://www.cpvmfg.com/news/low-e-valves/