Gold mining operations often utilize Pressure Oxidation (POx) as a crucial process for extracting gold from refractory ores. This advanced technique involves using high-pressure and high-temperature conditions to oxidize sulfide minerals, thereby releasing gold particles for subsequent recovery. In POx applications in gold mines, pumping systems and sealing devices are pivotal in ensuring efficient and reliable operation. Pump Engineer had the pleasure of speaking to TEADIT about the company’s innovative sealing and packing solutions, as well as keeping the integrity and reliability of complex pumping systems found in POx applications.
Pressure oxidation (POx) is the most demanding extraction method in the mining industry and requires dependable sealing devices that have been tested; these devices must withstand corrosive and abrasive slurries, as well as endure punishing temperatures and pressures; TEADIT discusses the significance of these components, their key challenges, and the strategies employed to overcome them.
The Role of Pumping Systems in Pox Applications
Pumping systems form the backbone of POx applications in gold mines. They are responsible for circulating and transferring various process streams, including slurries, gases, and liquids. The primary functions of pumping systems in a POx circuit include oxygen injection, slurry circulation, and liquor and solution transfer. Oxygen injection processes utilize high-pressure pumps that facilitate oxygen into the autoclave, ensuring optimal conditions for the oxidation of sulfide minerals and subsequent gold extraction. During slurry circulation, pumps maintain a consistent and uniform suspension of ore particles and reactants within the autoclave, aiding in efficient mass transfer and reaction kinetics. Lastly, pumping systems used in liquor and solution transfers enable the movement of various processes, such as acid solutions, neutralization liquids, and pregnant leach solutions, between different stages of the POx circuit.Sealing and packing devices are fundamental to mitigating these potential challenges as they create safety barriers that help operate these complex pumping systems successfully.
Overcoming Obstacles in POx Pumping Systems
From wear and tear to maintaining the integrity of equipment, and operating in extreme temperatures, pumping systems in POx applications face several obstacles that must be addressed to ensure efficient operation. The abrasive nature of the ore slurry, combined with the corrosive chemicals used in the process poses significant challenges to pump components. These factors often lead to wear, erosion, and reduced lifespan. Additionally, users must follow industry requirements for successful operation in extreme circumstances. POx applications demand pumps capable of handling high-pressure conditions that often exceed several hundred pounds per square inch (psi). The integrity and reliability of seals, gaskets, and valves under such extreme pressures are crucial. POx autoclaves operate at elevated temperatures as well, ranging from 150°C to 240°C (302°F to 464°F). Pumping systems must be designed to withstand these high temperatures to ensure reliable performance without compromising safety. Sealing and packing devices are fundamental to mitigating these potential challenges as they create safety barriers that help operate these complex pumping systems successfully.Sealing Devices for POx Applications
Sealing devices are integral to the performance and safety of pumping systems in POx applications. Critical sealing devices employed in this context include mechanical seals and gland packing. Mechanical seals are vital to containing the process fluids within the pump and preventing leakage. Specialized mechanical seals with robust materials and designs that can withstand POx slurries’ abrasive and corrosive nature are necessary. Gland packing, or compression packing, on the other hand, is an alternative sealing method commonly used in POx pumping systems. It involves packing the pump shaft with a material that forms a barrier against leakage. Proper selection of packing material is crucial to ensure compatibility with the process conditions.Utilizing Mechanical Packing
Mechanical packing is commonly used in specific areas of POx applications active in gold mines, where it is suitable for sealing requirements. A few key considerations regarding the use of mechanical packing in gold mine operations range from autoclave sealings to applying mechanical packing to the shaft of slurry pumps, valve stems and more.POx autoclaves require sealing around the agitator shaft, which maintains a uniform suspension of ore particles and reactants. Mechanical packing can create a reliable seal in this area, preventing leakage of the slurry and process fluids. Slurry pumps are critical in circulating the ore slurry within the autoclave. Mechanical packing can be applied around the shaft of the slurry pump to create an effective seal, avoiding leakage of the abrasive slurry, and maintaining efficient operation.
In addition to the pump system and its components, various valves are used in POx applications to control the flow of process fluids. Mechanical packing can be employed to seal the valve stems to ensure leak-tight operation and prevent the escape of corrosive liquids or gases. The POx processes involve various stages of acid solutions. Acid transfer systems can benefit from mechanical packing when it is used in pumps and valves, providing an effective seal against leakage, and preventing corrosion-related issues.
Selecting Quality Mechanical Packing
When selecting mechanical packing for POx applications in gold mines, it is essential to consider specific requirements of the process, such as temperature, pressure, and the corrosive nature of the process fluids. The packing material should be compatible with extreme conditions and resistant to abrasion and corrosion. TEADIT has a tremendous portfolio and a highly experienced engineering team that can help users select the most suitable material.The packing material should be compatible with extreme conditions and resistant to abrasion and corrosion. TEADIT has a tremendous portfolio and a highly experienced engineering team that can help users select the most suitable material.
Many important factors must be considered when selecting mechanical packing for slurry services. Users should consider the slurry makeup and understand that its properties can change during the life of the service. Mechanical packing related issues arise when the primary seal is compromised, resulting in abrasives to migrate and deposit across the face of the packing rings. This creates more friction, which increases the overall temperature in the system, making the packing hard and brittle, thus losing its sealing capability.
The standard practice in abrasive slurry applications uses flush water to cool, lubricate, and clean the mechanical packing. This is to ensure its long-term reliable operation in various services. TEADIT offers mechanical packing made with high-strength synthetic or aramid fibers, such as the Teadit 2773 (Novoloid yarn with PTFE and graphite paste impregnation), built to withstand abrasion abuse. The downside is that these fibers often exhibit less than ideal heat dissipation, thermal conductivity, and chemical resistance characteristics than traditional mechanical packings, such as those manufactured from graphite and PTFE.
To get the best of both worlds, TEADIT offers packings like Teadit 2003, which utilize aramid reinforced corners to provide added strength, combined with PTFE or graphited PTFE yarns where chemical resistance and overheating are concerns.
Using flush water has additional downsides as well. Some applications require costly systems to separate and evaporate this extra water that can get into the process flow and mix with the process media. Not to mention the challenges of maintaining the flush water pressure to ensure that it remains positive compared to the process; this is of particular concern as the process pressure increases, like in many mining applications. Flush water can also carry abrasive particles that impede the fluid flow leading the pump to run dry.
Today, a wide range of high-performance slurry pump packing materials can be used, from Phenolic, Novoloid, synthetic, carbon fibers to PTFE or graphite fibers, and moldable ‘puttylike’ materials. Pump packing constructed with Phenolic fibers has proven successful in complex slurry services, along with the combination of high tensile strength carbon yarn, which provides the reinforcement necessary to resist wear and abrasion. These graphite and carbon packings deliver low heat generation with excellent thermal conductivity.
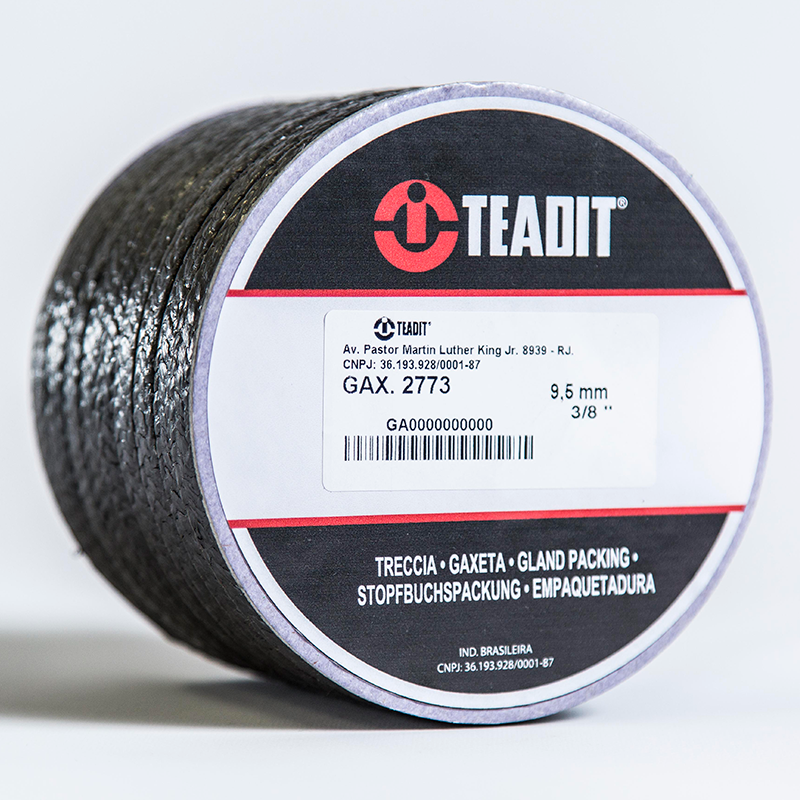
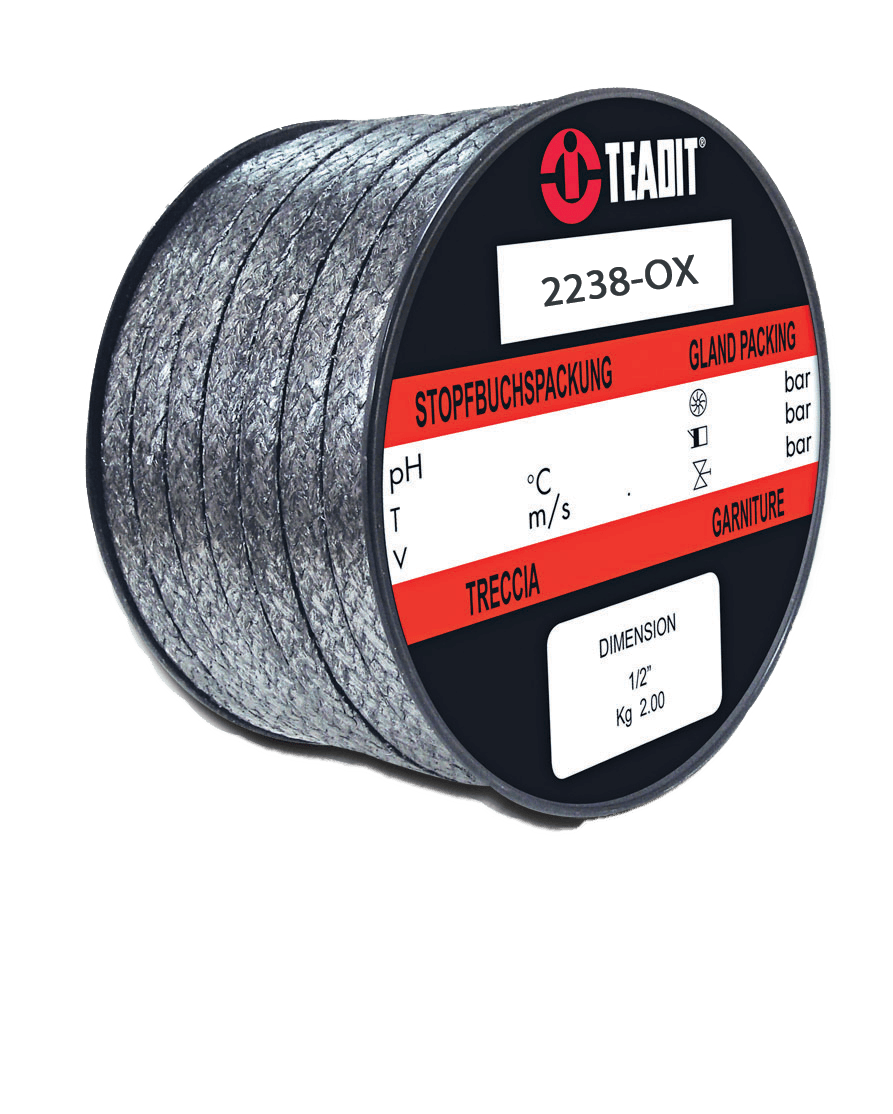
Combining Various Packing Styles
Additionally, impregnation and lubrication with materials like graphite, PTFE, and mineral or silicone oils also play an essential role in high-performance slurry pump packing by contributing to heat dissipation, sealability, and chemical resistance protection. Packing manufacturers incorporate different combinations of fibers, lubrication, and impregnations to handle various slurry applications. These mechanical packings can be mixed with restructured PTFE rings and moldable packing materials to obtain a positive seal in the application with or without flush water. Sometimes, an engineered design that combines different packing styles is the best option.Oxygen service packing is a specialized type of mechanical packing explicitly designed for applications involving oxygen or oxygen-enriched environments. The materials used to manufacture this component is compatible with oxygen and can withstand its reactive nature. In the context of Pox applications in gold mines, where high-pressure oxygen injection is a crucial component, 02 service packing plays a vital role in maintaining a reliable and leak-free seal.
These materials are selected to prevent combustion or chemical reactions that could compromise safety. In POX applications, the slurry and process fluids may contain abrasive particles and corrosive chemicals. The O2 service packing should be constructed with materials that can withstand these harsh conditions without premature wear or degradation, in addition to following stringent testing. Teadit 2238-OX (for valves) is designed for O2 services and was tested by BAM guidelines. It is made in a controlled environment to maintain the highest level of cleanliness and comply with all the safety features needed to manufacture a product for O2 services. Regular monitoring and maintenance of mechanical packing are necessary to ensure its effectiveness over time. Periodic inspection, adjustment, and replacement of the packing material should be carried out to prevent leakage and maintain reliable sealing performance.
It is worth noting that while mechanical packing can be suitable for specific sealing requirements in POx applications, other areas may require using alternative sealing methods, such as mechanical seals or other specialized sealing technologies. The choice of the sealing device should be based on a thorough evaluation of the specific application parameters and the desired level of performance and reliability.
Enhancing Efficiency and Reliability
Employing strategies such as monitoring, maintenance, and material selection can help address the challenges associated with pumping systems and sealing devices in Pox applications. It is vital the appropriate corrosion-resistant materials are selected. High-alloy steels, ceramic coatings, and elastomers can withstand the corrosive and abrasive nature of the process fluids. Moreover, implementing robust monitoring systems detect signs of premature wear, erosion, or seal failure.TEADIT at a Glance
TEADIT Group is a globally recognized leader in developing and manufacturing innovative solutions for critical fluid sealing processes. With a wide range of sealing products, TEADIT has become a vital resource for various industries, including Oil & Gas, Chemical Processing, and Power Generation, helping them achieve emission-free environments. Continuously investing in research and development, TEADIT stays at the forefront of industry needs.TEADIT’s packing and sealing innovations enable top-of-the-line solutions for these complex systems. In addition to replacing components or employing predictive and regular maintenance, it is essential that these innovations are implemented to prevent unexpected downtime. TEADIT’s ongoing commitment to research and development provides solutions for pumping systems in POx applications, making many options available to users looking to enhance failure prevention practices and optimize performance.