In rotating equipment applications, abrasive media can come in many forms; from the comparatively mild, like liquid chocolate, to the extremes found in industries such as mining, pulp & paper, and sugar processing. Moreover, slurry properties and content can vary greatly between the various industries and applications.
Slurry concentration, particle size, hardness, and the tendency to solidify or dewater, are all important considerations when developing an approach to addressing the sealing challenges relative to these applications. Pump Engineer had the pleasure of learning from Daniel Angulo, Mechanical Engineer at Teadit, the best approach to choosing the correct mechanical packing for industrial pumps.
Factors to Consider
There is no ‘one size fits all’ solution for the diverse scenarios of abrasive pumping applications; understandinghow the myriad of factors at play can affect overall seal performance can provide insight into how to choose the best mechanical packing to obtain the desired performance.
When selecting a mechanical packing for a slurry service, there are many important factors to consider. Not only must the slurry make-up be considered, but also how its properties can change during the life of the service. Mechanical packing related issues arise when the primary seal is compromised, and abrasives migrate and deposit across the face of the packing rings. This will create more friction, which in turn increases the overall temperature in the system, leading the packing to get hard and brittle; in short, the packing loses its sealing capability.
Maintaining Packing Integrity
The standard practice in abrasive slurry applications is to utilize flush water to cool, lubricate, and clean the mechanical packing. This is to ensure its long-term reliable operation in various services. Additionally, mechanical packing made with high strength synthetic or aramid fibers, like Teadit 2004, are built to withstand the abuse of abrasion. The downside is that these fibers often exhibit less than ideal heat dissipation, thermal conductivity, and chemical resistance characteristics compared to traditional mechanical packings, such as those manufactured from graphite and PTFE. In order to get the best of both worlds, packings like Teadit 2003 and 2017, utilize aramid reinforced corners to provide added strength, in combination with PTFE or graphited PTFE yarns where chemical resistance or overheating are concerns.The high rate of flush water required to mitigate the negative impact of abrasive materials in slurry applications can also lead to massive amounts of water consumption, especially when considering the number of pieces of rotating equipment present in many plants.
Using flush water has additional downsides as well. Some applications require costly systems to separate and evaporate this additional water that can get into the process flow and mix with the process media. The challenge is to maintain the flush water pressure to ensure that it remains positive compared to the process. Flush water itself can also carry abrasive particles that can impede the fluid flow leading the pump to run dry.
Solutions for Every Application
Today, there are a wide range of high-performance slurry pump packing materials that can be used; from Phenolic, Novoloid, synthetic, and carbon fibers, to PTFE/graphite fibers, and moldable ‘putty-like’ materials. Packing manufacturers, like Teadit, incorporate the use of different combinations of fibers, lubrication, and impregnations to handle various slurry applications. These mechanical packings can be mixed with restructured PTFE rings and moldable packing materials to obtain a positive seal in the application with or without flush water. In some instances, an engineered design that combines different packing styles with one another is the best option.For example, pump packing constructed with Phenolic fibers, and those made with a combination of high tensile strength carbon yarn, have proven successful in difficult slurry services as they provide the reinforcement necessary to resist wear and abrasion. These graphite/carbon packings deliver low heat generation with excellent thermal conductivity. Impregnation and lubrication of materials like graphite, PTFE, and mineral or silicone oils also play an important role in high-performance slurry pump packings by contributing to heat dissipation, sealability, and chemical resistance protection.
Solutions for Every Application
Today, there are a wide range of high-performance slurry pump packing materials that can be used; from Phenolic, Novoloid, synthetic, and carbon fibers, to PTFE/graphite fibers, and moldable ‘putty-like’ materials.Packing manufacturers, like Teadit, incorporate the use of different combinations of fibers, lubrication, and impregnations to handle various slurry applications. These mechanical packings can be mixed with restructured PTFE rings and moldable packing materials to obtain a positive seal in the application with or without flush water. In some instances, an engineered design that combines different packing styles with one another is the best option.
For example, pump packing constructed with Phenolic fibers, and those made with a combination of high tensile strength carbon yarn, have proven successful in difficult slurry services as they provide the reinforcement necessary to resist wear and abrasion. These graphite/carbon packings deliver low heat generation with excellent thermal conductivity. Impregnation and lubrication of materials like graphite, PTFE, and mineral or silicone oils also play an important role in high-performance slurry pump packings by contributing to heat dissipation, sealability, and chemical resistance protection.
Regardless of the application, when choosing the best mechanical packing option, it is important to consider all the factors in order to determine the optimal fit. Often, it only requires one important consideration to narrow down the potential choices.
Common Packing Suggestions
In an abrasive fluid where graphite contamination is not tolerable (like in paper production), Teadit 2774, which consists of Phenolic fibers with a PTFE impregnation, is often a great option. This packing combination has an excellent cost vs. benefit ratio and qualifies as one of the best options for pulp and paper, sugar, and alcohol industries; all of which require a packing that can withstand granular and abrasive media. It provides high durability and resistance to chemical attack without wearing out or damaging the shaft.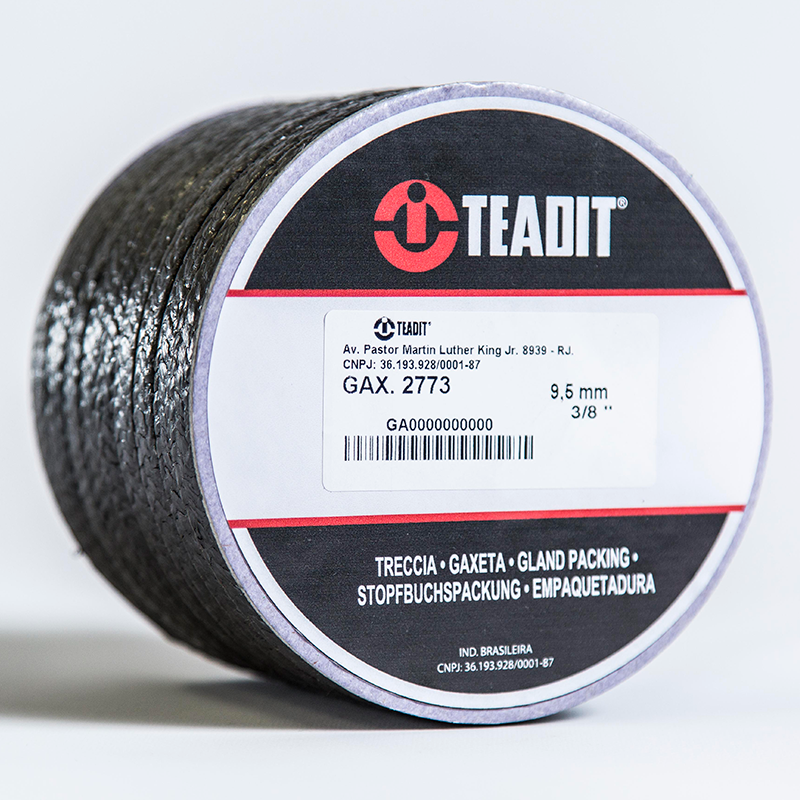
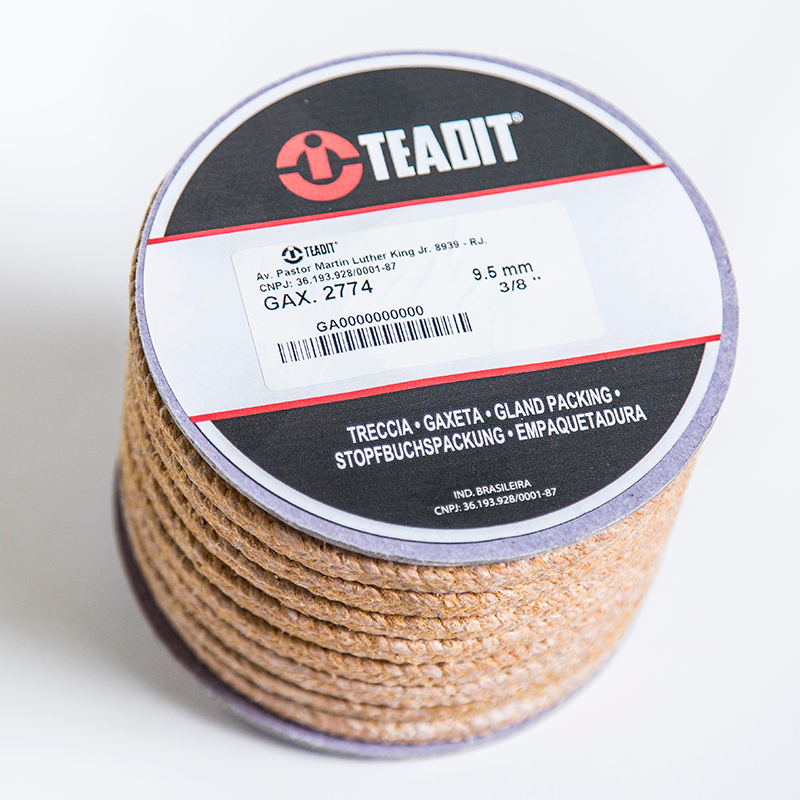
On the other hand, in applications where color is not of great concern, Teadit 2773 (Novoloid fiber with PTFE and graphite paste impregnation) has been successful sealing in a variety of abrasive media, such as those see in the steel industry, or the manufacturing of non-bleached paper. It has also been quite successful in mining applications. It has an excellent performance in pumps utilized for slag, ore pulp, irrigation, and wastewater treatment plants.
A more general service selection might be Teadit 2007 which features the proprietary EG8G-S PTFE/graphite yarn. This packing combines the chemical resistance of PTFE with the heat dissipation characteristics of graphite, thus allowing much higher shaft speeds than conventional PTFE packings. However, it is important to contact Teadit’s engineering team to evaluate the application conditions first before specifying. Also, Teadit 2202, carbon/graphite with carbon reinforced corners in the braiding can be another good general option. Graphite has excellent heat dissipation characteristics, and the carbon fiber reinforcement in the corners and the body of the packing makes it three times more resistant to extrusion and has increased pressure handling capabilities compared to non-reinforced flexible graphite packing.
One last recommendation, in general, the use of sleeves and shafts manufactured with hard metallurgical material is always a good option in slurry applications. Even the best mechanical packing can fail if the sleeve or shaft material is made with soft metal. A general hardness recommendation for shaft and sleeves will be materials with at least 60 HRC.
Benefits of Careful Considerations
With the most recent packing material advances and innovations at Teadit developed through extensive research and development initiatives, abrasive applications are no longer expensive and difficult to seal. Whether using a single material, or combination of different packings, there are many options available to control the performance and environmental demands of problematic slurry applications. If the application is properly addressed and fully considered, selecting the appropriate materials can generate significant savings.Stepping up to a high-performance material designed to specifically handle the abuse of slurry applications will easily offset the expense of a less effective solution.