The chemical compound hydrogen fluoride is commonly referred to as HF. When it comes in contact with moisture, it reacts to form hydrofluoric acid; a highly corrosive, toxic, and extremely dangerous substance that causes severe burns to human skin and other body tissues. It is a colorless gas or, when below 67°F, a fuming liquid.
Despite its aggressive nature, HF is an important source of the fluorine that is used in the manufacturing of a number of products including refrigerants, plastics, and pharmaceuticals. HF can also be used in the alkylation units at petroleum refineries turning crude oil into gasoline.
HF Alky Units
In refining, the fluidized catalytic cracking unit (also known as FCC or cat cracker) produces low-molecular-weight olefins, typically either propylene or butylene. The alkylation units produce a high-octane gasoline blend-stock known as alkylate by reacting the light olefins from the FCC with isobutane. This reaction occurs with the aid of an acid catalyst. The acid is either sulfuric acid (H2SO4) or hydrofluoric acid (HF). While HF alkylation units are very effective, they are particularly vulnerable to hydrofluoric acid corrosion. This creates unique maintenance, reliability, and safety concerns. Because of the severe nature of this service, many consider HF alky units to be one of the most critical sealing applications in all of the industry.Flange Corrosion
Hydrofluoric acid corrosion is a concern in any process that utilizes HF, because even trace amounts of water are reactive. Dry hydrogen fluoride, or Anhydrous HF, poses no risk to common carbon steel piping, vessels, and flanges. But these same carbon steel components are not intended to be subjected to HF acid, or wet hydrogen fluoride.While HF process units are carefully monitored and controlled, unexpected problems are inevitable. Water introduced and remaining in the system during cleaning or maintenance activities, or intrusions from leaks in other parts of the manufacturing process, can lead to HF acid formation, which can lead to corrosion and eventually dangerous leaks. Areas within the process that provide the potential for pooling are at the greatest risk for acid corrosion.
Because the HF alkylation process operates at temperatures and pressures that exceed the reliable service capabilities of most soft sheet gasketing materials, semi-metallic options like spiral wound gaskets or camprofile gaskets are commonly used. ASME B16.20 spiral wound gaskets include a metal ring set inside of the sealing element to prevent unwanted inward radial buckling. These inner rings create small gaps between the face of the metal inner ring and the inside portion of the flange face at the bore. That recessed area just inside of the pipe creates the perfect environment for HF pooling to occur. Once the HF acid begins pooling on the flange face, the refinery will quickly experience corrosion to the inside diameter of the flange face. The tapering or pitting of the flange face is a cause for major rework and can be a tremendous expense, especially if it results in replacing and/or upgrading flanges. To counteract this problem, most refineries are requiring the installation of specially designed alky gaskets. These alky gaskets utilize various types of new technologies that incorporate a secondary seal to protect the inside diameter of the flange face.
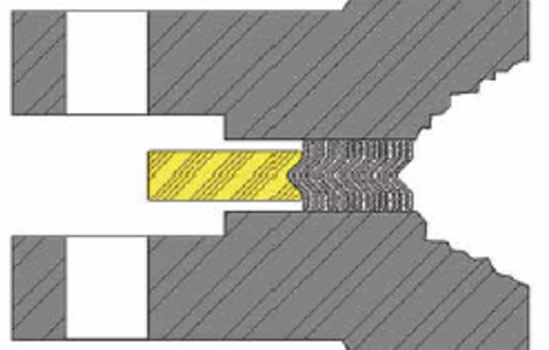
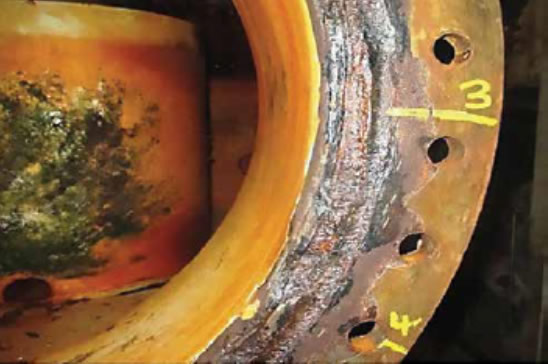
Sealing Challenges
There are two competing requirements in creating an effective seal for use in HF acid service. First, the gasket needs to exhibit excellent sealability. Due to the high risk it poses to human health, exposure limits for HF in the workplace are extremely stringent and gasket tightness is the key to meeting the required thresholds. If the primary gasket seal is not ‘low-emission level’ tight and can reliably stay at that level in service, then any other benefit of the gasket design is inconsequential. Second, the gasket needs to create an effective seal at the flange inside diameter to eliminate potential pockets for HF acid pooling, leading to unwanted flange corrosion.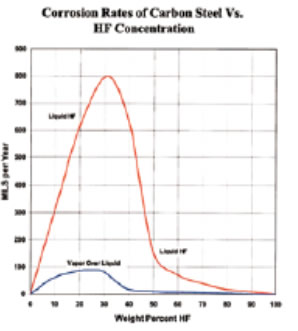
Gasket manufacturers have used varying gasket designs in their efforts to meet the needs of HF alky units. While each exhibits subtle nuances, the overall concepts seem fairly consistent. The approach has been to develop a two-part gasket: one to provide the primary fire-safe sealing, and the other to provide the flange corrosion protection. The primary sealing element utilizes flexible graphite as a facing or filler material in combination with Monel 400. There are design variations between what type of metal construction (spiral wound, solid metal with serrations, corrugated metal, etc.) is used for the primary seal. Regardless of which construction style is selected, it is highly recommended to specify a high-temperature, oxidation-inhibited grade of flexible graphite to be used as the primary sealing material.
Commonly, these specialized HF service gaskets utilize an expanded PTFE secondary sealing element of some type. PTFE is highly effective in aggressive services due to its nearly universal inertness to process media. Additionally, expanded PTFE is highly compressible, allowing it to easily conform to flange sealing surfaces that may already exhibit some wear or corrosion. There are many design variations in thicknesses, core types, adherence methods, and expanded PTFE types used in secondary sealing. When utilizing expanded PTFE as part of the secondary sealing solution, it is highly recommended to specify a low creep material that has uniform density. Just because a material is a soft, white PTFE, that alone does not mean that it is qualified to be used to seal HF acid.
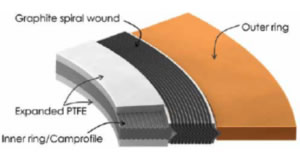
These are referred to as two competing requirements because both the primary and secondary sealing need to occur without negatively impacting either component’s ability to perform as designed. That is more difficult than it would first appear. At its most basic level, gasket sealability is a direct result of optimizing the stress applied to the gasket at the flange sealing surface. Stress is simply a force, in this case the clamping load developed by the flange bolts, distributed over an area.
By incorporating a secondary sealing element in an alky gasket design, the sealing surface area of the gasket increases. This means that great care needs to be given to optimizing both the primary and secondary seals to ensure that each seals adequately. A secondary seal that is too thin or too soft may not be able to be adequately compressed to effectively protect the flange surface as required, or account for existing surface wear. Conversely, a secondary seal that is too thick or too robust may perform well in preventing flange corrosion, but may also prevent adequate loading of the primary seal, potentially creating an extremely dangerous situation.
Gasket Programs
Finally, it is worth mentioning that there are no gasket materials or designs that will perform as required without the proper program in place to manage them. Several considerations need to be made, and questions asked, such as:How are the flange assemblers at the site trained and verified on installing alky gaskets correctly every time? How is inspection done to determine if existing flange corrosion is at an unacceptable level? Are there torque cards and charts easily accessible by all necessary team members and do those torque values correspond with the current gasket design, fastener grade, and lubrication method? Are specifications written in such a way that there is no ambiguity in purchasing the items or having orders filled from the supplier? Are all necessary inbound inspection processes in place and how are the gaskets to be properly stored prior to use? Is there adequate inventory on-hand to reduce emergency needs? Are contractors permitted to deviate from site specifications? Is there a tagging and inspection procedure? Does your gasket design require or recommend a 4-hr or 24-hr retorque and if so, is that being followed?
There are gasket designs that take all of these factors into consideration and gasket programs that help manage the success of the gasket design. When it comes to something as serious as sealing HF acid, it is essential to ensure there is a fire-safe gasket with a low-emission level primary seal, properly designed ePTFE secondary seal. It is also integral to oversee the integrity of the sealing performance within a managed program.