In the world of fluid sealing and gaskets, the story begins and ends with gasket stress. At its most basic level, bolted flange joint reliability depends on adequately loading a gasket to create and maintain a seal. While this sounds simple enough, experience has shown that the process of effectively sealing an industrial system is ripe with challenges.
With all these factors to consider, it can be challenging to seal standard pipe flanges, and these challenges can often be exacerbated in specialty equipment, vessels, and flanges. Stainless Steel World Americas had the pleasure of speaking with TEADIT to discuss how some of the most difficult applications to seal are those that are torque limited to low clamping forces, such as lined vessels and MONDI™ piping.
John Bickford, in his book “Gaskets and Gasketed Joints,” suggests that there can be hundreds of variables influencing joint reliability. These types of connections often require special consideration when it comes to gasket selection, as many traditional gasket technologies are not able to effectively seal under such low load conditions. Historically, both lined equipment and MONDI™ piping applications have utilized tailored approaches to sealing.
What is MONDI™ Piping?
MONDI™ piping is made with a special alloy of ductile iron that can handle high concentrations of sulfuric acid up to 300°F. (MONDI™ derives its name from MONsanto and Ductile Iron). This special metallurgy provides a longer operating life in this aggressive service due to its corrosion resistance characteristics. However, the flange connections for MONDI™ piping have limited load capacity, so the applied torque, and subsequent clamping forces, are lower than in traditional flanged connections.To account for this low-load condition, the traditional approach for sealing MONDI™ flange connections has been to utilize a step ring-type gasket. These gaskets feature a traditional ring gasket with a second, narrower ring affixed or machined into the face of the carrier gasket, to develop a stepped profile. The idea behind this design is that the applied load can be concentrated on the smaller raised profile. Since stress is simply the applied force distributed over the contact area of the gasket, this provides the desired effect of minimizing the surface area to maximize the developed sealing stress
The facing on MONDI™ flanges can also create challenges for less compressible (i.e. harder) gasket materials. These special considerations can make sealing MONDI™ pipe flanges challenging.
Most step ring-type gaskets utilize two separate layers of material held together with an adhesive layer. This creates several sealing concerns. First, the adhesive layer provides a potential leak path through the body of the gasket. Second, while these gaskets are commonly manufactured from PTFE-based materials that exhibit an indefinite shelf-life, the same is not true of the adhesive. Over time, gaskets being stored on site can delaminate. Finally, layered PTFE gaskets exhibit more creep than single-layer gaskets due to ‘slippage’ between the layers. Gaskets count on the friction created at the flange surface interface to help restrict and resist creep.
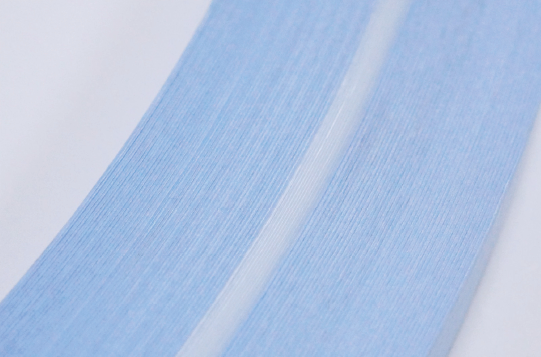
Introducing Origin® Technology
In 2017, as part of a continuous search for better performance and sustainability, Teadit introduced its patented, and award-winning, Origin® technology used to manufacture PTFE gaskets. This process produces gaskets made from sintered and wound PTFE tape.Tapes may be with or without fillers, expanded or not, with or without pigments. There are nearly infinite combinations to create the most suitable gasket product for each application. Different additives can be used in different regions of the gasket to have specific characteristics, including varying colors to identify these properties. Additionally, this technology allows the manufacture of thicker or large diameters gaskets without splices.
Another feature of this technology is the reduction of waste, since the fabrication of gaskets from the cutting of sheets is extremely inefficient, causing waste that can reach more than 60% of the sheet material. Origin® technology reduces process losses to virtually zero while substantially reducing environ- mental impact. In 2018, Origin® technology was recognized by The Chemours Company, receiving the Plunkett Award, which highlights innovations based on the use of fluoropolymers. It went on to be recognized three more times by winning the Plant Engineering ‘Product of the Year’ award in 2018, a Vaaler Award in 2019, and was also recognized by the Downstream Awards.
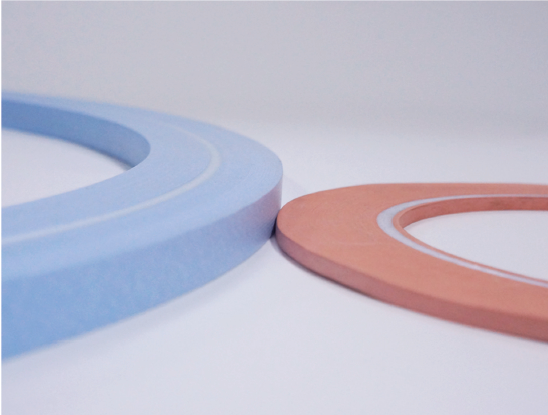
Origin® APF-510 for Sulfuric Acid Piping
TEADIT engineers’ study of the use of Origin® technology in acid piping applications has led to the development of the Origin® APF-510 gasket; a soft gasket with an impermeable sealing barrier for sulfuric acid process piping. It is designed to meet the specific conditions of piping where the flanges often have scratches, corrosion, or other irregularities.The Origin® APF-510 gaskets are produced from expanded PTFE tape with glass microspheres, resulting in an extremely compressible gasket that conforms to flange irregularities. To ensure a tight and reliable seal, a low porosity pure PTFE barrier is located near the gasket ID and under the pipe end to prevent permeation.
To test the design, TEADIT developed a rig using a MON- DI™ pressurized piping spool with two blind end flanges, one of which had a digital pressure gauge. The gaskets were installed as specified by the piping manufacturer. To simulate flange damage, a small hole was drilled through one of the flanges. After assembly and pressurization, the rig was submerged in water and evaluated for signs of leaks (i.e. bubbles) and the internal pressure was monitored for 48 hours. A second penetration test was performed utilizing the same rig filled with red dye and pressurized to twice the original pressure.
The Origin® APF-510 showed extremely favorable results in both lab tests. No visible signs of leakage were observed, and the final pressure loss after 48 hours was less than 0.5 psi. Additionally, the dye penetrant test clearly showed that no permeation occurred beyond the barrier layer.
Origin® in Glass-Lined Equipment
Another excellent application for Origin® technology is glass-lined equipment. Glass lining is popular in tanks and other vessels used in aggressive services. Obviously, great care must be given to prevent damage to the fragile glass lining. This means that connections to glass-lined vessels require limited clamping force to ensure that developed stresses do not exceed the glass’s capacity, resulting in cracks. Another challenge with glass-lined equipment is the inherent waviness in the mating surface. On large vessels, it is not uncommon to see variances as large as ¼” or more.Many glass-lined vessel OEMs utilize PTFE envelope gaskets which consist of a thin virgin PTFE outer jacket (or envelope) with, typically, two layers of a low-quality fiber material with a corrugated metal ring in between, used for filler. These gaskets are then shimmed when installed to compensate for gaps.
PTFE envelope technology is dated and comes with many known issues, the greatest of which is the PTFE envelope itself. As virgin PTFE exhibits a high level of cold flow, it is possible to over-compress and cut through, or otherwise damage, the thin outer shell of the gasket. When this happens, the inner filler materials, none of which are compatible with the aggressive services most glass-lined equipment handles, are exposed to the process media, and leaks quickly occur. Additionally, envelope gaskets exhibit poor recovery.
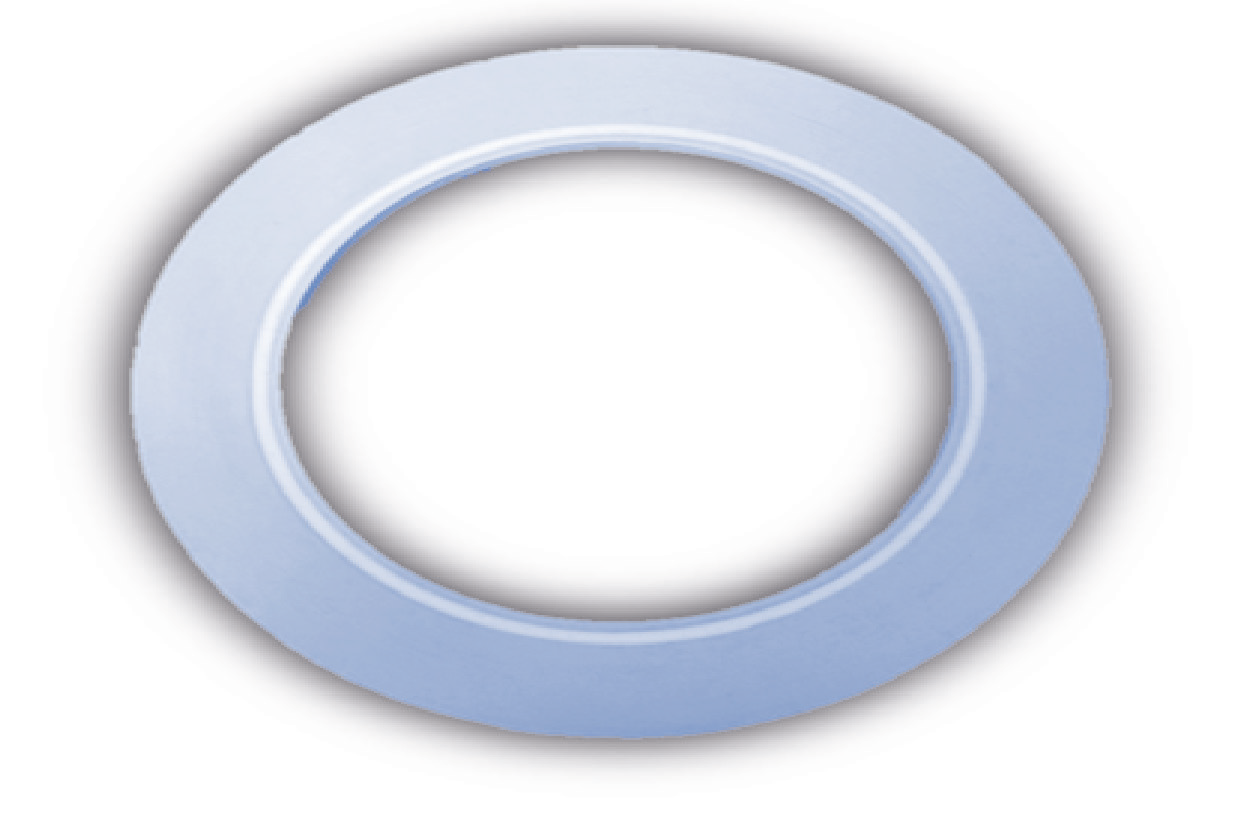
Origin® technology, on the other hand, exhibits excel- lent recovery characteristics. For example, the Origin® RC-510 railcar tank manway gasket was tested for over 40 open-close reuse cycles with no loss in sealing performance.
Another benefit of Origin® technology is that the gaskets can be manufactured in almost any thickness. Traditional gasket materials typically max out at ¼” thickness. In some cases, such as in high spots where the glass aligns, this could result in face-to-face contact with the mating surfaces and damage to the glass lining. If, on the other hand, large gaps exist, the ¼” thick material may not be enough to fill the gaps; traditional gasket materials are not able to be easily or effectively shimmed.
Soft and compressible materials are sometimes used to replace PTFE envelope gaskets on glass-lined equipment. However, ‘soft’ in the gasketing world of- ten indicates that a material is more porous and susceptible to wicking through the body of the gasket. Again, the option to include a pure PTFE barrier layer, like that which is used in the Origin® APF-510 gasket, has shown proven resistance to permeation.
Origin® technology gaskets are highly compressible and will easily conform to the conditions of the mating flanges in glass-lined equipment. It is designed to ensure a positive seal at low tightening loads on deformed surfaces. By filling any gaps and molding to the sealing surface, it creates a tighter and more reliable seal.
TEADIT AT A GLANCE
TEADIT Group is recognized worldwide as a leader in the development and manufacturing of innovative products for critical fluid sealing processes. The wide variety of sealing solutions developed by TEADIT have been important tools for many industries including Oil & Gas, Chemical Processing, and Power Generation. TEADIT has helped several industries achieve the goal of an emission-free environment within their facilities. TEADIT is constantly investing in research and development to keep up with the evolution of the industry’s needs.TEADIT North America is located in Houston, Texas with seven worldwide locations in South America, Europe, and Asia. The variety of sealing solutions developed by TEADIT is fundamental to achieving the leakage-free goal in the many industries served. The quality and effectiveness of these solutions are based on management and innovation, which are the basis for all products manufactured at any TEADIT plant. As a result of this continuous process of quality improvement, an ISO 9001 certification was obtained in Brazil, the United States, and Europe.
The 64-year history of TEADIT began in Rio de Janeiro and has led to more than twenty patents on products and processes. Their corporate values of Integrity, Reliability, Safety, and being Customer Focused and all culminate in their vision statement: Sealing For A Safer And Greener Tomorrow.
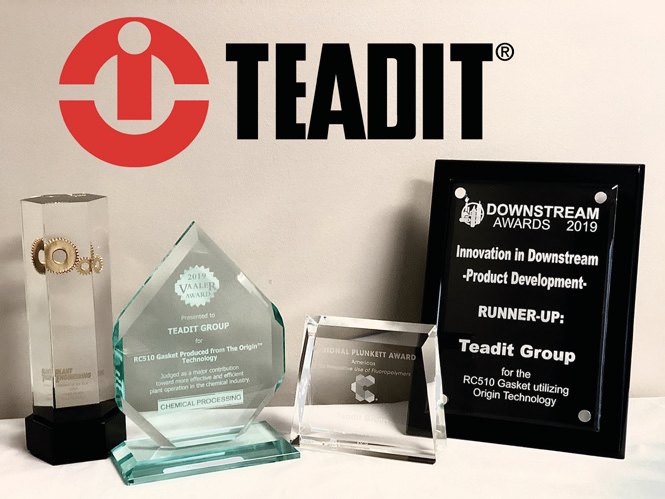
In Conclusion
The uses for Origin® technology are nearly as limitless as the possible configurations that it can be made to. MONDI™ piping, glass-lined equipment, and rail-car manways are just a few of the many successful uses TEADIT and its knowledgeable team of product experts and engineers have found thus far. In many ways, the company is just scratching the surface of what it can do with this innovative technology.Even in general services, as a replacement for traditional cut gaskets, Origin® technology offers several distinct advantages. EN13555 testing shows favorable results when compared to modern structured PTFE, like Teadit Tealon and similar competitor materials. Additionally, the manufacturing process allows for one-piece gaskets larger than the maximum outside diameter of sheet-cut gaskets which are limited by the commonly available square sheet size of around 60 inches.