Fabric expansion joints play a vital role in various industrial processes. These joints are essential for maintaining structural integrity, preventing leaks, and accommodating thermal expansion, contraction, and vibration. Compared to metallic expansion joints, fabric expansion joints offer distinct advantages in certain scenarios, making them a preferred choice for systems that involve the movement of hot gases and air. Understanding the key aspects of fabric expansion joints is crucial for ensuring efficient operation and longevity of industrial systems. The following are five important things to know about fabric expansion joints.
1 – Key considerations
There are several types of fabric expansion joints designed to meet specific application requirements. Users must select the style best suited to their application to mitigate the risk of asset leaks and failures. Each type of expansion joint offers distinct advantages depending on the system’s design, operating conditions, and movement requirements.There are therefore six primary factors to consider when choosing a fabric expansion joint.
- Operating temperature: Evaluate the temperature range of the system and choose materials that can maintain mechanical properties within the desired temperature range.
- Movement requirements (thermal, vibration, seismic): Assess the expected movement of the piping system and select an expansion joint capable of accommodating the required range of motions.
- Chemical and heat compatibility with process gases: Evaluate how corrosive the chemicals that will be in contact with the material are, as well as the temperature range of the system; choose materials that can maintain their mechanical integrity.
- Environmental conditions (e.g., exposure to corrosive elements).
- Installation: Determine the size and configuration of the ductwork/piping. Then assess whether the expansion joint needs to be assembled in the field or delivered as a single unit. It is important to consider factors such as labor costs and ease of installation.
- Compliance with industry standards and regulations.
2 – Importance of materials selection
Fabric expansion joints are typically constructed from specialized materials capable of withstanding high temperatures and corrosive environments. The construction of fabric expansion joints involves layers of fabric or insulation; it is a combination of multi-layers of inorganic fabric and flueoropolymer layers externally impregnated with silicon or PTFE on their composition.The use of these materials ensures flexibility while maintaining structural integrity under challenging operating conditions. For particularly severe applications, the use of reinforced fi berglass coated in PTFE is often the most optimal choice as it has a high resistance to both heat and corrosive chemicals. The use of custom-made materials is something end users should consider when trying to tailor solutions to meet specific application requirements. A careful analysis of the system is often required before the design phase, to determine the materials of construction needed and other required components.
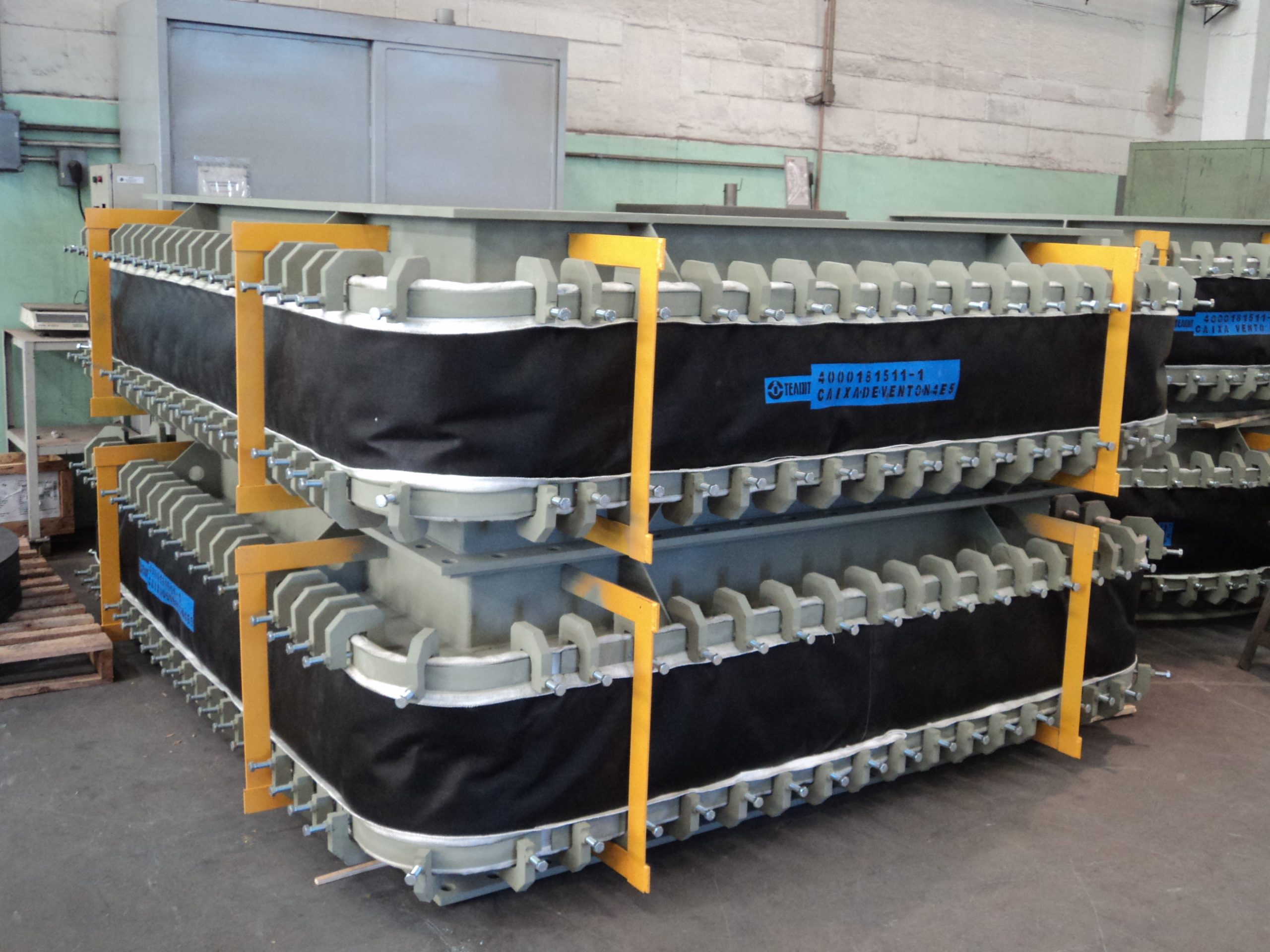
3 – Installation practices
As fabric expansion joints use different frame types depending on the application, understanding the design elements for each joint, as well as how to install it, is of vital importance. The two distinctive categories are flanged and belt types. In the flanged configuration, the belt has a ‘U’ shape which allows for a small overall length (OAL) and a simplified metallic structure. This design reduces the initial cost of the expansion joint but can sometimes increase the maintenance cost as the belt is more difficult to replace. The belt-type configuration allows for flanged or welded connections and has the advantage of a simple belt replacement. Regardless of the frame type, several variables should be considered when installing fabric expansion joints.Here are some of the key variables to consider:
External Duct Insulation: Typically seen in systems that have high temperatures, the external insulation must not overlap the belt. This could cause issues with the heat exchange between the bellows and the environment which can ultimately cause the fabric to deteriorate.
Flange Connection: If possible, the use of a welded connection is often recommended to mitigate the risk of connection failure.
Inner Sleeve: Designed to protect the bellows and insulation pillow from turbulent flow and control the accumulation of particulate materials in the frame cavity, Inner Sleeves are generally adopted when the flow velocity exceeds 10m/s.
Insulation Pillow: Used when the media being conveyed has solid particulates to prevent the materials from accumulating in the frame. If the material is able to accumulate the fabric joint will lose its flexibility or combust. They can also be used in exhaust turbine ducts and large draft fans to fill out any cavities to avoid pressure variations and flutters on the application start-up.
Cuff: Fabricated with fabrics with high thermal insulation properties, a cuff is used to protect the bellows from heat transfer through the metallic frame.
Back-up Bar: A back-up bar is placed on the external surface of a bellow and is used to connect bellows to the metallic frame. It is important to consider its width and thickness as it is designed to provide the system with additional sealing when in operation.
4 – Pipe to joint sealability
One often overlooked element of fabric expansion joints is the importance of their sealability. A tight seal ensures that harmful gases or particulate matter cannot leak into the surrounding environment, preventing air pollution and potential health hazards. Despite the bellows having their sealing surface, it is necessary in some situations to incorporate additional sealing to compensate for irregularities. Additionally, proper sealability helps maintain the optimal flow of gases through the ducts, ensuring efficient operation of industrial processes such as heating, ventilation, and air conditioning systems. By preventing leaks and maintaining airflow, sealability in fabric expansion joints contributes to overall system reliability, safety, and compliance with environmental regulations. Investing in high-quality seals and regularly inspecting and maintaining them is crucial for the effective functioning of flue duct systems.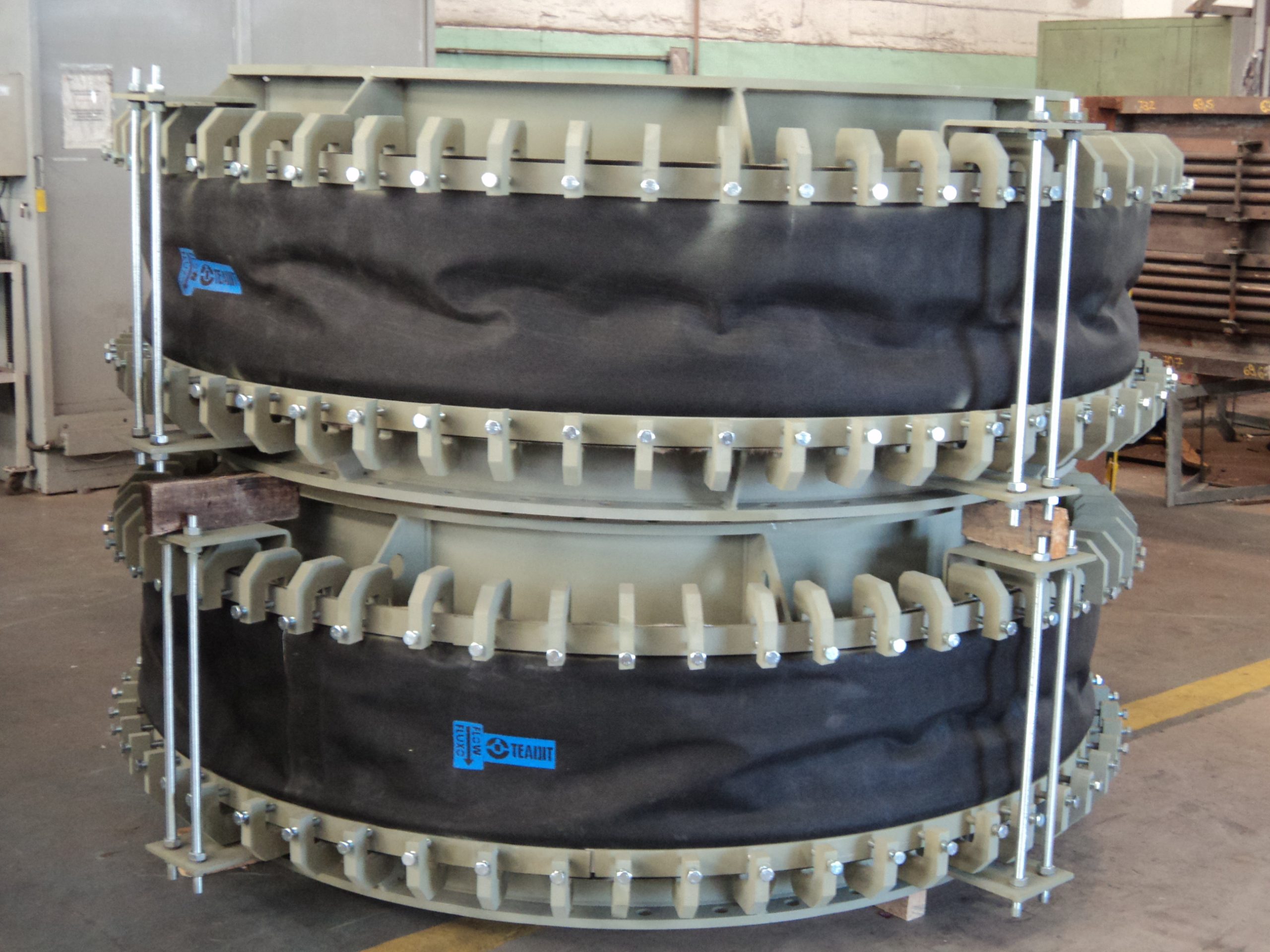
5 – Maintenance matters
Regular maintenance is essential for maximizing the performance and longevity of fabric expansion joints. Regular inspection and maintenance routines should include checking for signs of wear, corrosion, or damage, as well as verifying proper alignment and movement capability. Indications of damage such as discoloration, corrosion, or the presence of hot spots, must be met with immediate steps to replace the compromised assets. Timely replacement of worn or damaged expansion joints is necessary to prevent potential system failures and costly downtime.Overview
Fabric expansion joints are critical components in industrial ductwork systems, providing flexibility while maintaining system integrity and preventing leaks. Understanding the key aspects of these expansion joints, including their purpose, construction, types, installation, maintenance, and selection considerations, is essential for ensuring efficient operation and longevity of industrial processes. By prioritizing proper installation, regular maintenance, and appropriate selection, industrial facilities can optimize the performance and reliability of their flueduct systems, minimizing downtime and enhancing overall productivity.