Polytetrafluoroethylene (or PTFE) is an integral material in the world of fluid sealing due to its excellent chemical resistance characteristics. However, one of the disadvantages, especially with virgin PTFE products, has been their generally poor mechanical properties, particularly their high relaxation, and tendency to creep (or cold flow) under load.
Over the past several decades, manufacturers have worked to find ways to improve on these shortcomings, leading to advancements in PTFE gasket and sealing technology. In the world of fluid sealing, not all PTFE products and materials are the same, and it is worth comparing the most common PTFE flat gaskets when determining which is best suited for a given application. The primary classifications of PTFE gasket materials within the industry are skived, structured, and expanded.
It is important to note that differences between PTFE products extend beyond just the three general categories. The statement about differences between PTFE products and materials holds true even for the raw materials/resins utilized in manufacturing. Structured and expanded PTFE require a much higher quality PTFE resin than simple skived PTFE. With its longer molecules, the higher-quality PTFE has considerably greater potential for higher strength. This strength is paramount in reducing creep and relaxation.
Virgin and Skived PTFE Sheet Manufacturing Process
Due to the molecular weight, PTFE cannot be processed like other thermoplastics through melting. Instead, it can only be processed through compressive and sintering techniques. The polymer is compressed into a preform, typically a cylindrical form (commonly referred to as a billet), at room temperature. The PTFE resin mixture is compressed with a specific pressure during this process. Additionally, sometimes different fillers, such as glass or silica, as well as color pigments, are added during mixing.After pressing, the preform undergoes a defined heating and sintering process at 370°C to 380°C. This solidifies the preform into a homogeneous structure. Once the pressed parts have completely cooled down, they are often subjected to additional machining processes such as skiving to obtain sheets, as well as turning, drilling, and milling for direct sealing production.
This process comes with inherent challenges, as it is difficult to maintain consistent physical properties throughout the structure of the preform. Sheets skived off the same billet will often exhibit different densities and other characteristics depending on where on the billet it was cut from.
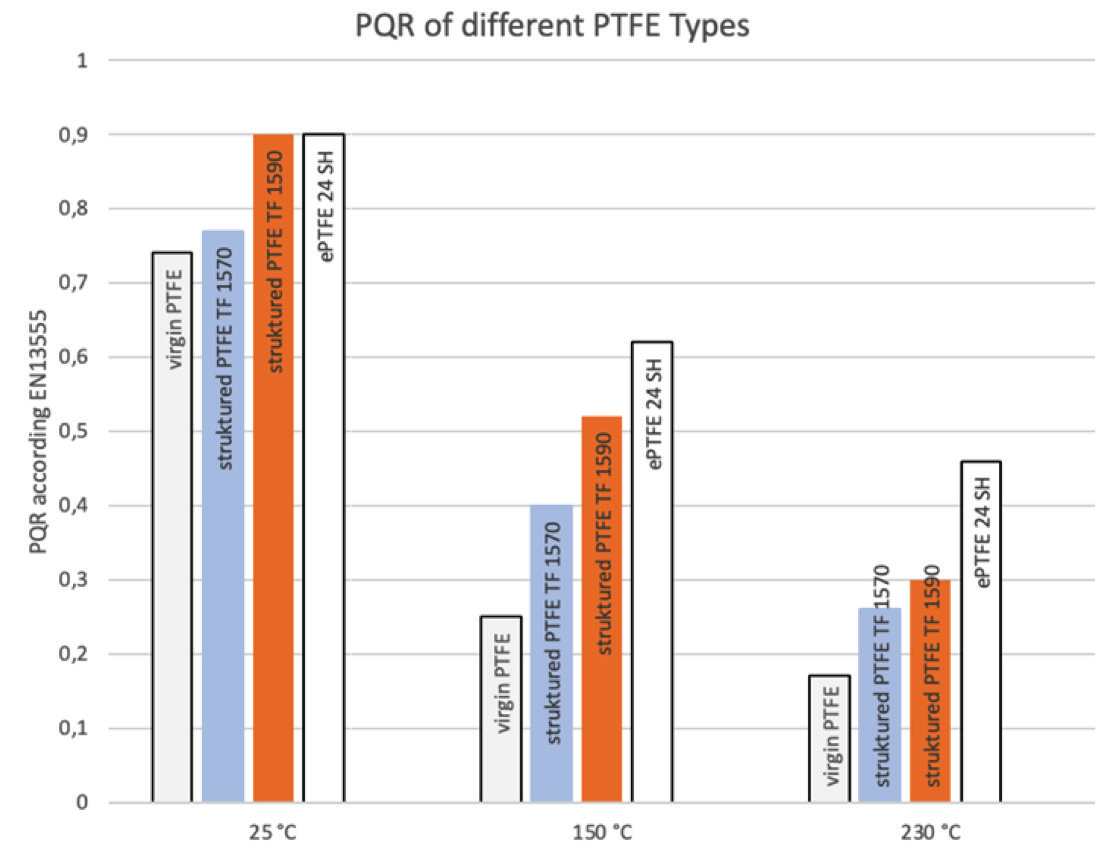
Structured PTFE Manufacturing Process
Paste PTFE resin is highly sensitive to shear and is therefore mixed with a lubricant before processing. This lubricant diffuses into all cavities and acts as a spacer during subsequent shear stress in extrusion or calendering; this affects the level of shear energy applied. In addition to the lubricant, application specific fillers, and specific color pigments are typically added to the paste PTFE resin. Typical fillers include hollow glass spheres, silica, and barium sulfate. These fillers help provide additional strength to the raw PTFE. Using a specialized calendering process to evenly disperse these fillers throughout the PTFE sheet structure can help to maximize the added benefit they provide.The most well-known calendering process is called HS10; it was originally developed by DuPont. In this process, PTFE is sheared and oriented in different directions. The applied shear energy results in fibrillation; the long-chain PTFE molecules intertwine with each other and with the fillers. This structure significantly improves creep behavior and consequently extends the sealing service life. A final sintering process, as described earlier, is mandatory. As this process seeks to provide added structure to the material, it is commonly referred to as ‘structured PTFE’.
The quality of the finished sheets, and ultimately the gaskets manufactured from them, depends on the degree of fibrillation and the type and proportion of the filler used. A higher filler content is desired for better mechanical properties. However, the proportion must be precisely balanced, as the amount of PTFE itself significantly impacts the seal’s tightness. Without careful control of both the material makeup and the structuring process, the desired result (a high degree of fibrillation) is not fully achieved, and the resultant material properties suffer accordingly.
Expanded PTFE Manufacturing Process
Similar to the structured process, in expanded PTFE (or ePTFE for short), PTFE is mixed with a lubricant. Subsequently, the PTFE is compressed into a preform. The purpose of pressing is to remove the present air from the mixture. The preform is then pushed through an extrusion die in an extruder to obtain the desired shape. The extrusion die must be designed to ensure a high degree of fibrillation (interweaving of the long-chain PTFE molecules) in the PTFE occurs. A two-roll calender is then used for calendering the profiles. The calendering process from the profile to the foil is usually carried out in a single operation. The foil is then dried at temperatures between 150°C to 200°C, which completely removes the lubricant.Next, the foil undergoes a longitudinal stretching process by at least two rotating roller systems operating at different speeds, at a temperature of 250°C to 350°C. Depending on the quality of the paste PTFE resin utilized, the foil can be stretched with a ratio of over 1:10 without the formation of defects. The stretched material becomes highly porous, resulting in a monoaxial alignment.
An additional stretching process in the transverse direction allows the foil layers to acquire a biaxial or multidirectional alignment, forming expanded PTFE membranes. A multidirectional PTFE exhibits uniform fibrillation in all directions, significantly improving its mechanical properties. For multidirectional expanded PTFE sheets, multiple membranes are stacked on top of each other and sintered together at higher temperatures before being further processed.
The thickness of the membrane, homogeneity of stretching, and degree of fibrillation significantly influence the mechanical properties and the tightness of the material. Monoaxially stretched PTFE can be used as sealing tape or sealant. Biaxially or multi-directionally stretched PTFE is available as sealing tape and as sheets.
Comparing Different Models
Comparative studies of different PTFE gaskets can be used to measure the creep re- laxation behavior. The following investigations refer to tests according to EN 13555.EN 13555, is a popular European test standard that provides several important sealing parameters that assist with the comparison of different materials. The four parameters for meeting the leak tightness requirement are:
• The maximum surface pressure strength of the gasket (above this, the gasket or the flange is destroyed),
• The required minimum surface pressure to achieve the desired tightness (below this, leakage increases),
• The applied surface pressure when installing the gasket,
• The Leakage rates.
These detailed gasket parameters as well as the creep and relaxation properties of the gasket, are key selection criteria for a gasket and are uniformly defined in EN 13555. The determined parameters are subsequently used for torque calculations according to EN 1591-1 and for the classification of PTFE types.
PQR Value (Creep Relation Value)
An important resultant value from EN 13555 testing is the creep-relaxation (PQR) value. The PQR value is determined by assessing the ratio of residual surface pressure to initial surface pressure after a relaxation test conducted in a press using a displacement-controlled load sensor at a specific stiffness. The resultant PQR value can range from 0 to 1.A PQR value of 1 defines no loss of surface pressure, indicating an extremely high level of creep resistance. If the gasket loses all surface pressure during the test, a PQR value of 0 is obtained. Therefore, a high PQR value is desirable.
PQR Test Results
Image 1 shows the different PQR values of the various PTFE types. The tests were conducted with an initial surface pressure of 30 MPa and temperatures ranging from 25°C to 230°C. The results of the test indicate that the special manufacturing processes of structured PTFE and expanded PTFE consistently result in higher PQR values. The significant advantages of high- quality PTFE become Particularly relevant at temperatures elevated above 100 °C.Calculation Results According to EN- 1591-1
The EN 1591-1 standard is used to determine the strength, tightness, and compliance of bolted joint connections based on the TA Luft (European air pollution control regulations) requirements. The calculation results are based on a DN50/PN10 flange connection with 3 mm gaskets made of sintered PTFE (virgin), structured PTFE (TF1570 and TF1590), and expanded PTFE (24SH). The EN 1591- 1 calculations result in two main torque values: a theoretically maximum torque limited by the weakest component, and a minimum required torque to achieve the desired tightness class. Applying the maximum torque increases safety and improves the tightness of the connection.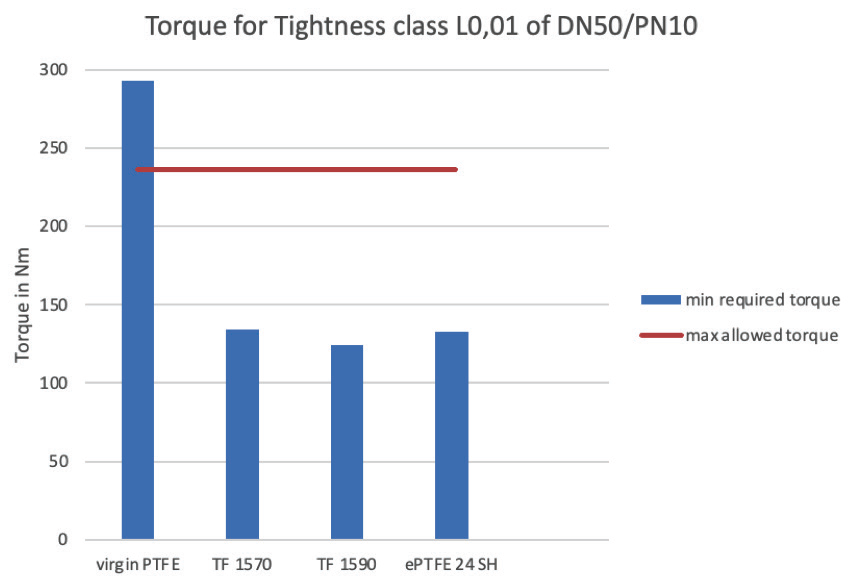
Calculations under the same conditions but with differently manufactured PTFE gaskets will result in minimum torque values as shown in Image 2. These minimum torque values are necessary to achieve a tightness class of L0.01 under the given conditions. Applying torque above the maximum torque will damage one of the components (flange, bolt, or gasket).
Typically, for small dimensions, the bolts are the weakest component, while for larger dimensions, the flanges are the weakest. Due to the low PQR value of virgin PTFE, extremely high minimum torque values are required to achieve a consistently tight connection. However, with structured or expanded PTFE, a wider torque range can be obtained. High-quality ePTFE, due to its higher PQR value, offers advantages over structured PTFE, particularly at temperatures above 100 °C.
Conclusion and Practical Tips
These investigations demonstrate the diverse range of PTFE as a material in sealing technology. Raw material quality and manufacturing processes are decisive factors in producing high-quality gasket materials. When combined with appropriate manufacturing expertise, the fundamental material properties of PTFE can be significantly improved. The test results and calculations provide a good assessment of the different materials and confirm practical user experiences:- Virgin PTFE exhibits significant creep/ cold flow behavior, resulting in a high loss of surface pressure and increased leakage, ultimately leading to joint failure. The range of application conditions for this material is typically limited to mild temperature and pressure.
- To reduce the creep behavior of typical PTFE, structured PTFE incorporates not only fillers but also generates fibrillation through calendaring. This modification raises the safe operating temperature and pressure significantly.
- Insufficient fibrillation, inadequate filler selection, and improper PTFE content are often present in low-cost and poorly made PTFE materials.
- 100% multidirectional ePTFE, particularly for the chemical and pharmaceutical industries, holds the highest value as a gasket made of pure PTFE. The highly- fibrillated material allows for meeting the most demanding requirements in terms of creep stability, maximum surface pressure, and temperature.
- The production of expanded PTFE sheets is by far the most complex process in manufacturing PTFE sheets, requiring a high level of expertise. This explains the significant quality differences between market leaders and other suppliers.
Considerations for designers/engineers:
- There are significant qualitative differences in PTFE that must be considered when selecting a gasket. When in doubt, it is advisable to seek the advice of experts
Considerations for procurement professionals:
- High-quality PTFE resins and other raw materials in the manufacturing process, as well as the cost of manufacturing high-quality, high-performance PTFE sealing materials is not generally cheap. It is important to consider the hidden costs of material purchase price savings.
Considerations for maintenance management:
- PTFE gaskets can significantly increase the service life and quality of equipment and products if the correct project-specific PTFE is chosen.