Every day engineers scour the internet and marketing brochures looking for gasket material test data. Perhaps they are working to design a new heat exchanger and require the crucial gasket design factors. Or maybe they are working to solve a challenging application issue at their plant. They might be trying to decide if they should add a new material or manufacturer to their company’s list of approved gaskets or manufacturers. Whatever the reason might be, there is, in general, a great deal of interest in gasket performance, primarily for the purpose of comparing different gasket materials and technologies.
The answer to the question of gasket performance might seem intuitive. Line up the datasheets side by side and compare the numbers, right? It might be surprising to learn, however, that the solution is much more complex.
A TEMES ”all-in-one” test rig can perform many standard gasket property and performance tests.
The answer to the question of gasket performance might seem intuitive. Line up the datasheets side by side and compare the numbers, right? It might be surprising to learn, however, that the solution is much more complex.
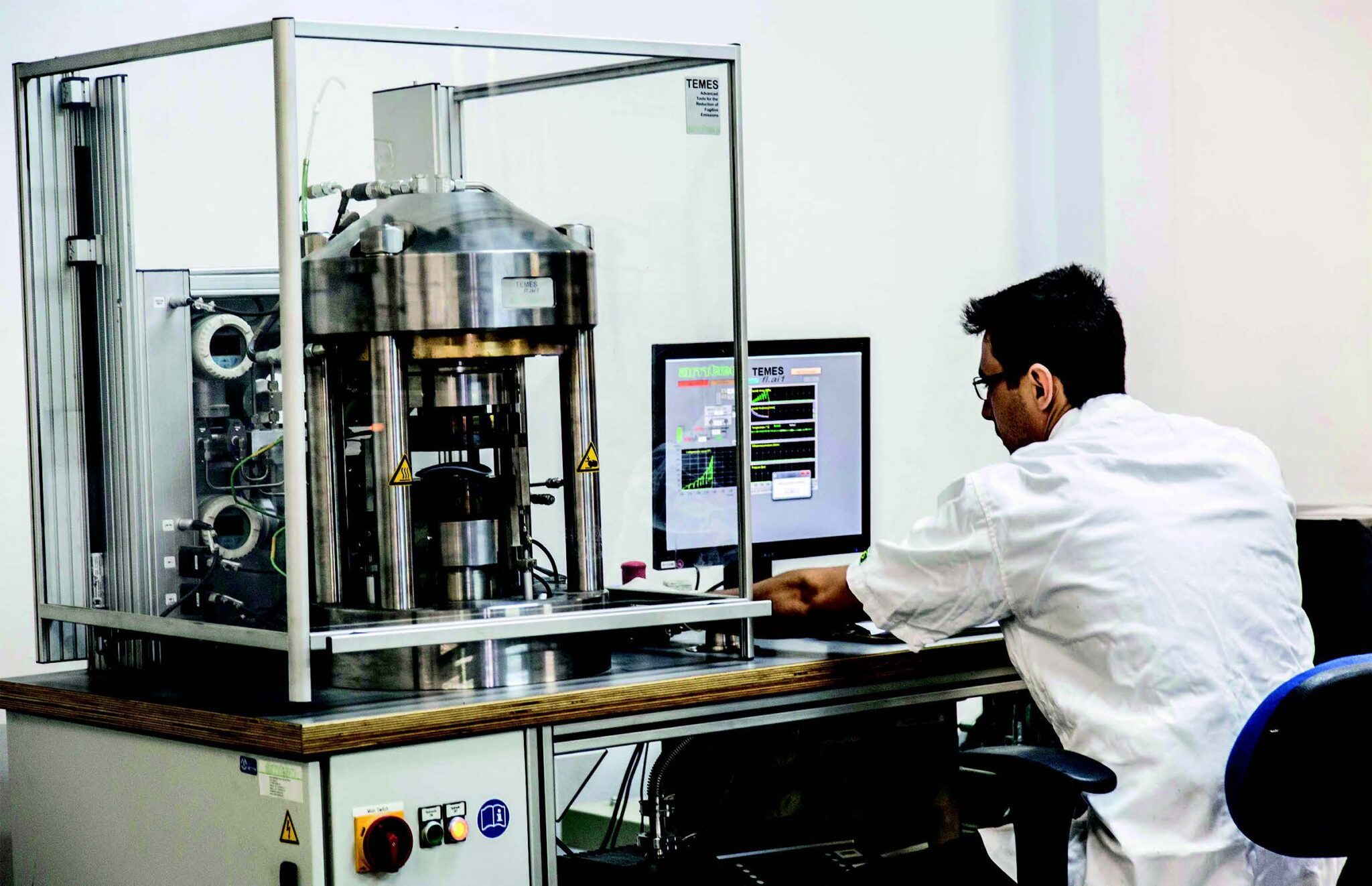
ASTM Tests
As one might expect, there are numerous standard tests to determine the gasket properties that appear on product datasheets. For ‘soft gaskets’ (that is gaskets that are typically cut from sheets or rolls of material), tests like ASTM F36 (compressibility and recovery), ASTM F37 (sealability), ASTM F38 (creep relaxation), ASTM F152 (tensile strength), and others provide data-points for comparison. The problem with these tests is not that they do not provide accurate physical properties, but that they are poor indicators for real world gasket performance. There are a few reasons for this.First, these tests are performed on pieces of testing equipment that do not simulate how the gasket will actually be used in service. Second, they are limited to the parameters of the test. For example, the ASTM F36 compressibility and recovery test is performed on a sample material that is 1/16” thick and subjected to 5,000 psi gasket stress at ambient temperature. Therefore, the results of that test only provide a data-point for 1/16” thick material at 5,000 psi gasket stress at ambient temperature.
What if the material is thicker or thinner? What if it is has more or less gasket stress applied than 5,000 psi? What if the temperature is above room temperature? What type of compressibility and recovery should be expected under that variety of conditions? The standard ASTM datasheet test does not provide that information. Additionally, these tests do not apply to other non-soft gasket technologies like spiral wound gaskets, serrated and faced camprofile gaskets, or metal jacketed gaskets.
Datasheet information can help technicians compare different materials, but beyond that, it really will not give much of an indication if that material will work in a particular application, or even what the pros and cons of utilizing a particular material in that application might be. Moreover, some tests, like ASTM F3149 (formerly F586) which is used to establish the commonly referenced gasket design factors m & Y do not standardize all the test requirements. This eliminates using m & Y as reliable metrics for making a true ‘apples to apples’ comparison. This unfortunately can incentivize manufacturers of gasket material to produce values that favor marketing and producing a competitive advantage over objective engineering.
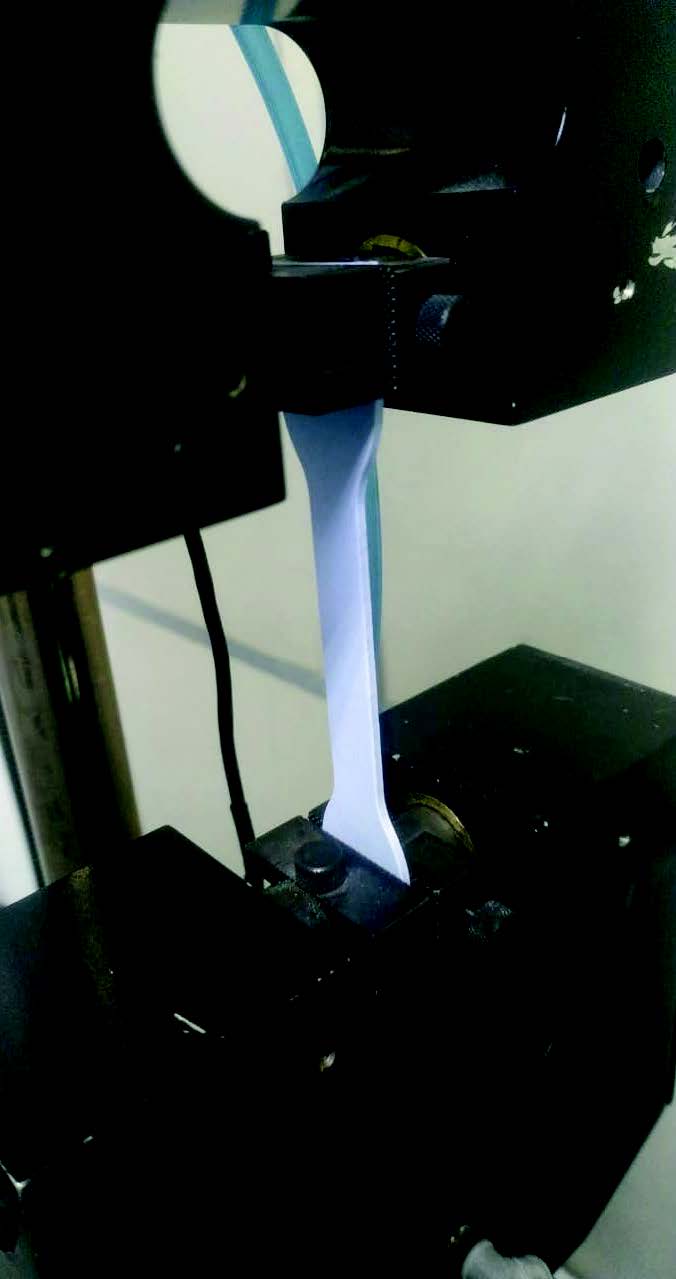
ROTT to the Rescue?
If datasheets are insufficient at supplying the information required for proper analysis, where can one turn to truly evaluate gasket performance? For design purposes, ASTM adopted standard F2836, the Room Temperature Tightness (or ROTT) test for determining tightness-based design factors to supplant m & Y values. This was considered by many to be a significant step in the right direction, but it is not without its flaws. Opponents of ROTT argue that the test results are not repeatable, and designers have been slow to adopt it.Additionally, some of the same issues that plague other tests apply to ROTT testing as well; primarily the usefulness of a test that is performed at ambient temperature, when most gasketing applications do not operate at ambient conditions, is in question.
Additionally, some of the same issues that plague other tests apply to ROTT testing as well; primarily the usefulness of a test that is performed at ambient temperature, when most gasketing applications do not operate at ambient conditions, is in question.
The Best Available Performance Testing: EN13555 and B16.20
When it comes to developing testing that can be used to better evaluate gasket performance, some overseas countries have perhaps been responsible for some of the most valuable recent contributions. Tests like DIN EN13555, which provides data-points related to a gasket’s ability to create and maintain a seal when exposed to numerous cycles of compressive loading at fluctuating temperatures and pressures, can provide empirically determined quantifiable data that can serve as performance indicators. While not a perfect representation of real-world conditions, this type of testing methodology does a better job simulating conditions in-service gaskets are likely to experience. It is important to mention that any test conducted in a lab on a specialized testing equipment and under controlled conditions is inherently flawed when it comes to mimicking the myriad of variables that are present in any bolted flange joint.The industry itself has been responsible for a wealth of valuable information. The annual ASME Pressure Vessel and Piping (PVP) conference which features technical research papers and presentations has been fertile soil for the development of innovative ideas. Back in November of 2021, Valve World Americas published an article that highlighted the advancements of ASME B16.20 spiral wound gasket technology. The genesis for the sealing performance requirements of the standard was within two PVP papers developed by a team led by Mr. Jose Veiga, the recently retired Global Technical Director of TEADIT.
Veiga’s team proved that spiral wound gasket performance is a result of the optimization of the winding density and construction. Then, they developed a testing procedure and requirements to help ensure that standard B16.20 spiral wound gaskets would meet industry fugitive emissions requirements that paralleled those found in API emissions standards. However, currently, ASME B16.20 spiral wound gaskets are the only gaskets that boast such requirements and testing. It is up to the current generation of engineers to build upon the work of industry statesmen like Veiga, David Reeves, Warren Brown, and John Bickford, among others, to push sealing technology to the next level. With the goal of a net-zero carbon footprint on the horizon, there will continue to be a need to develop reliable ways to evaluate gasket sealing performance and identify the best available products and technologies.