Expansion joints play a critical role in managing pipe stress in various industrial applications across several industries. In Fluid Catalytic Cracking (FCC) units, high temperatures and pressures generate significant force on piping and connected equipment. Performing movement tests, after manufacturing and during testing phases validates the expansion joints design and confirms the limit forces, without damaging critical equipment. Plant operators and maintenance engineers should, therefore, be aware of the key steps, tools, and considerations for testing the expansion joints used in these applications.
Through pipe stress analysis, simulations loads and deflections can be determined to a reasonable level of certainty. Those loads and deflection can be applied to the expansion joints in a laboratory setting through in what is called a ‘movement test.’ During this test, joints are subjected to controlled angular and lateral movements while the applied load is measured at each degree of motion. These tests reveal the spring rate (the force required to move the joint) and help verify that the joint can accommodate expected movement due to thermal expansion in FCC pipelines. This test essentially bridges the gap between theoretical calculations and real-world performance, enhancing the overall dependability of the installation.
More specifically, movement testing is particularly essential for:
An in-line pressure balanced expansion joint with a heating system to maintain the bellows temperature in a specific range
Movement testing of expansion joints follows a structured procedure to simulate the mechanical and thermal loads expected in real-world operation.
For accurate testing, the following key equipment is typically used:
It is important to note that movement tests on expansion joints installed in FCC units should be performed under pressure to account for operational loads.
A universal pantographic cold wall expansion joint.
accommodate angular movements. These joints often feature a series of pins that must handle high loads while maintaining fl exibility. Movement testing under pressure allows engineers to observe the effects of high-pressure friction on the hinge pins, an important factor since frictional forces can increase with pressure and potentially lead to binding or higher load requirements.
In addition to testing, careful selection of materials and design enhancements is crucial. For hightemperature applications, materials like Alloy 625 may replace standard 321 stainless steel for improved corrosion resistance. Movement testing validates these design choices by confirming that materials can handle the operational stresses without degradation.
Expansion joints, though often viewed as simple components, are essential in maintaining the integrity of complex FCC operations. By following the outlined steps, operators gain the assurance that these components will deliver the required flexibility, durability, and performance under real-world conditions.
Step 1: Understand the purpose of movement tests
Expansion joints allow fl exibility within piping systems by accommodating extreme thermal loads and minimizing stress on equipment, thus preventing excessive force on surrounding structures and connections. FCC units are an integral part of refi ning processes that makes low octane gasoline which is blended with a higheroctane gasoline or get upgraded to a higher octane. As they operate at high temperatures (approximately 700°C (1300°F)) to break down heavy hydrocarbons, expansion joints are needed to prevent load transfer to sensitive equipment, such as turbo expanders.Through pipe stress analysis, simulations loads and deflections can be determined to a reasonable level of certainty. Those loads and deflection can be applied to the expansion joints in a laboratory setting through in what is called a ‘movement test.’ During this test, joints are subjected to controlled angular and lateral movements while the applied load is measured at each degree of motion. These tests reveal the spring rate (the force required to move the joint) and help verify that the joint can accommodate expected movement due to thermal expansion in FCC pipelines. This test essentially bridges the gap between theoretical calculations and real-world performance, enhancing the overall dependability of the installation.
More specifically, movement testing is particularly essential for:
- Thermal expansion: High temperatures in systems like FCC units cause signifi cant thermal expansion. Movement testing ensures that the joints compensate for this expansion without imposing undue stress on nearby components.
- Pressure resistance: Movement tests under pressure reveal how pressure infl uences the expansion joint’s internal pins, rings, and friction, which can increase due to operational loads.
- High-temperature insulation and seals:Movement testing identifi es if high-temperature insulation and seal materials within the expansion joint, like braided seals or metallic sleeves, impact the reaction loads under movement.
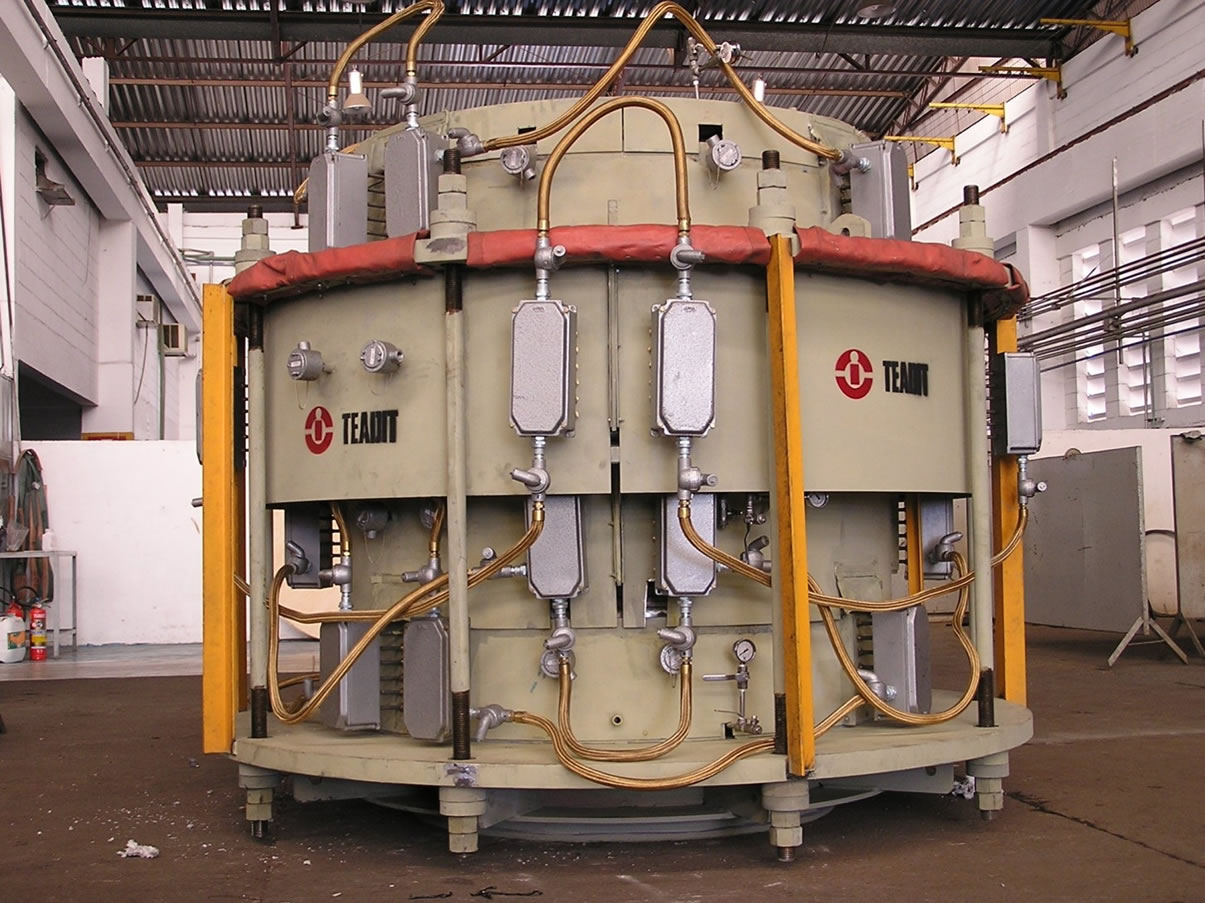
Movement testing of expansion joints follows a structured procedure to simulate the mechanical and thermal loads expected in real-world operation.
Step 2: Assemble testing equipment and tools
The ‘setup’ of a movement test involves attaching a dynamometer to a device system that exerts force on the expansion joint. During the test, the expansion joint’s movement and load at specifi c movement or angles are recorded. This setup allows for precise measurement of movement, ensuring alignment with design calculations.For accurate testing, the following key equipment is typically used:
- Dynamometer: Also referred to as an electronic scale, this measures the applied force on the expansion joint.
- Pulley system: Used to apply a controlled load.
- Angle/Movement gauge: This helps measure the movement of the expansion joint.
- Pressure source: A means of pressurizing the joint (if testing under simulated operating pressure).
Step 3: Conduct the movement test
- Apply controlled load / Inside pressure:
- Begin by applying a small amount of force to the joint and slowly increase it.
- Measure the force at each degree of linear or angular displacement (e.g., 1°, 2°, 3°) to record the response of the joint.
- Technicians compare these results with calculated spring rates to ensure that the joint’s performance aligns with design expectations. Testing may also include recording frictional load changes due to pressure, offering insight into the durability and performance of the joint under pressurized conditions.
- Measure angular displacement:
- Using the gauge or scale, the displacement of the expansion joint is measured and recorded. This data helps verify if the joint meets the design’s movement specifications.
- Check for consistency:
- With some expansion joint manufacturers, such as Teadit, the test results are compared with historical data and theoretical calculations. Customers receive a comprehensive report detailing each joint’s performance, ensuring the components meet the required specifications. This test confirms that the joint’s spring rate is within acceptable parameters and aligns with design specifications.
It is important to note that movement tests on expansion joints installed in FCC units should be performed under pressure to account for operational loads.
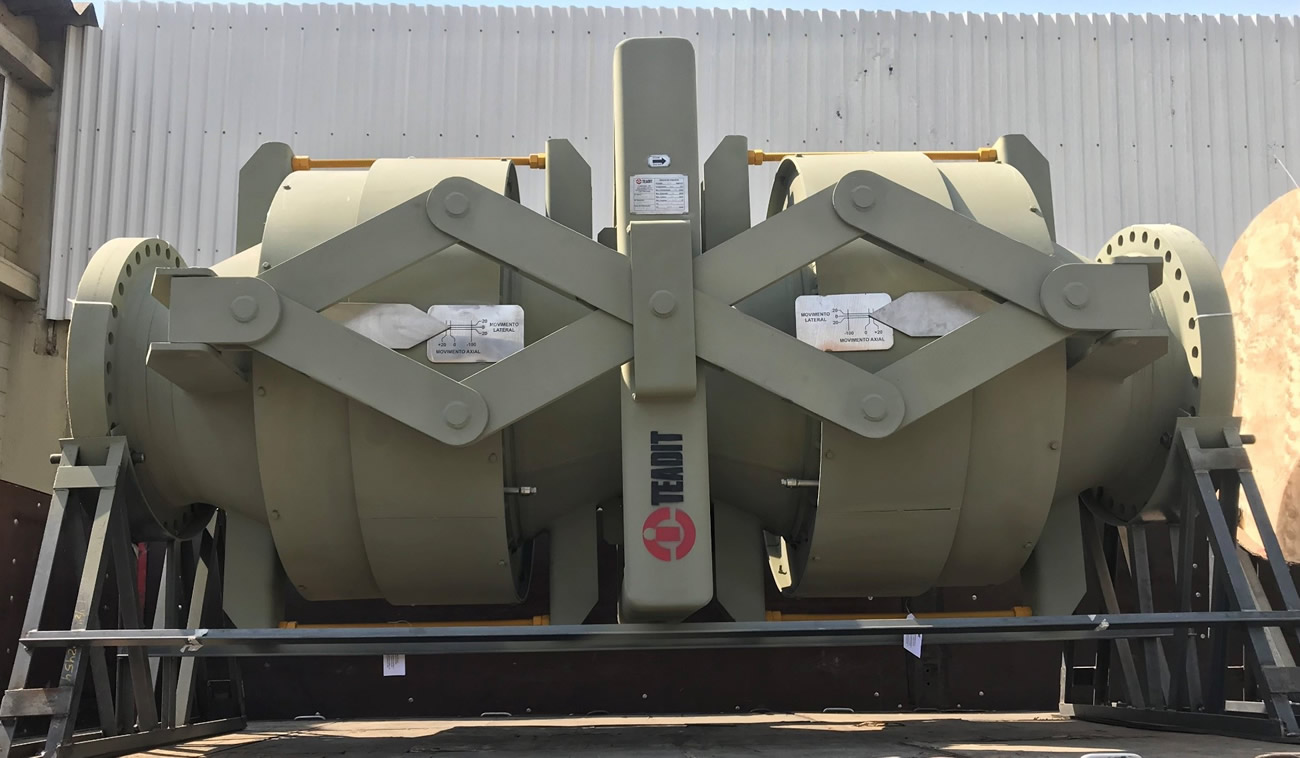
Step 4: Record and analyze data
Data collected during the movement test—including force, applied movement, and pressure readings provide essential insights. It is always advised to follow prescribed best practices. For example, Teadit follows the outlined process:- Verify against design calculations: Confirm that the measured spring rate and load capacities align with design calculations
- Identify potential modifications: If discrepancies are detected, adjustments may be required to optimize performance. This can include another pipe stress analysis.
- Provide documentation: Prepare a report detailing the test process, findings, and whether the joint meets performance expectations.
Design considerations: hinged and gimbal expansion joints
In FCC systems, hinged and gimbal expansion joints are commonly used due to their ability toaccommodate angular movements. These joints often feature a series of pins that must handle high loads while maintaining fl exibility. Movement testing under pressure allows engineers to observe the effects of high-pressure friction on the hinge pins, an important factor since frictional forces can increase with pressure and potentially lead to binding or higher load requirements.
In addition to testing, careful selection of materials and design enhancements is crucial. For hightemperature applications, materials like Alloy 625 may replace standard 321 stainless steel for improved corrosion resistance. Movement testing validates these design choices by confirming that materials can handle the operational stresses without degradation.
Conclusion
Movement testing plays an invaluable role in FCC installations, ensuring that expansion joints will perform as designed under intense conditions. By validating theoretical calculations, identifying potential stress points, and improving component reliability, movement testing helps refi nery operators avoid costly downtime and enhances overall system safety.Expansion joints, though often viewed as simple components, are essential in maintaining the integrity of complex FCC operations. By following the outlined steps, operators gain the assurance that these components will deliver the required flexibility, durability, and performance under real-world conditions.