Using the right seal is critical in maintaining safe and efficient operations.
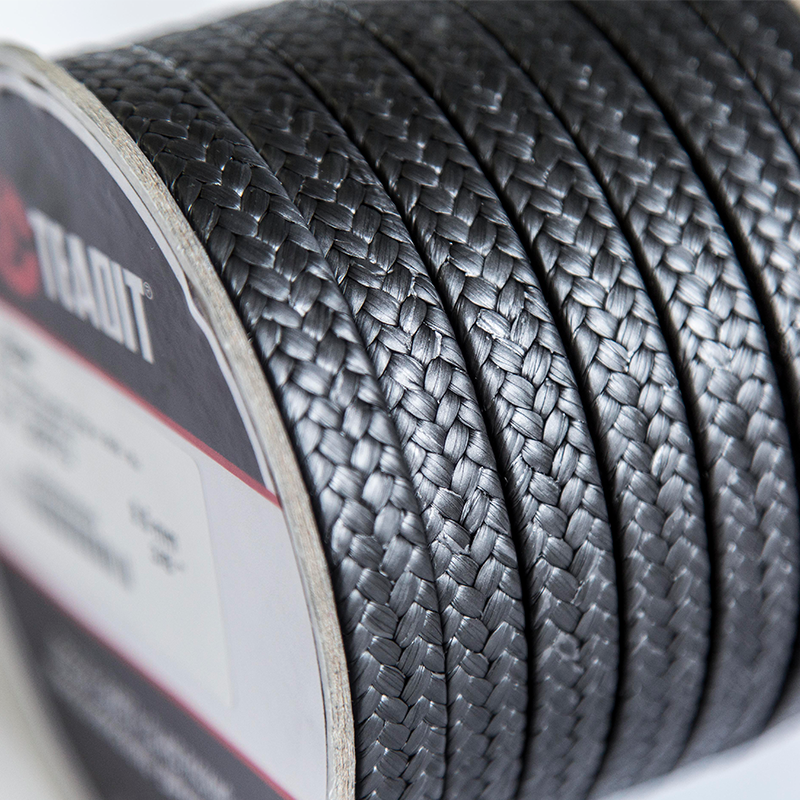
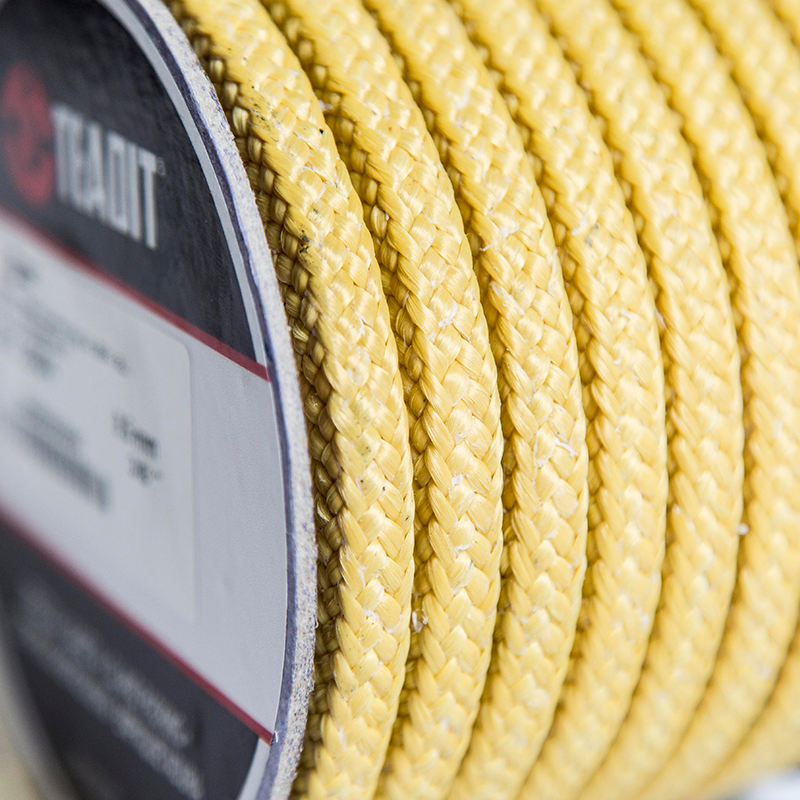
In the vast array of industrial processes, pumps serve as a vital asset, propelling fluids through pipelines, systems and machinery. The efficiency and reliability of these pumps are often contingent upon selecting the right seals.
Sealing products not only prevent leaks but also contribute significantly to the longevity and performance of pumps. However, with myriad sealing options available, choosing the appropriate one can be a daunting task. Understanding the sealing selection criteria is essential for ensuring optimal pump performance across various industrial sectors.
While some sealing issues can be mitigated through preventive maintenance, other sealing challenges occur unexpectedly and can severely compromise the reliability of the process. The consequences of a downed pump due to failing or condemned packing can have a significant impact on both a facility’s production and the asset itself.
Damaged pump shafts and improper installation are common causes of seal and packing failure that can lead to hazardous leakage, a lack of compliance with standard regulations, as well as economic impacts on a facility’s production. Therefore, operators must be aware of the key factors to consider before selecting a sealing solution to mitigate these risks.
Compression packing seals—consisting of braided or molded packing materials such as graphite, polytetrafluoroethylene (PTFE), aramid fibers or other synthetic fibers—often incorporate break-in lubricants to enhance their sealing performance and longevity. While packing seals are ideal for applications where minor leakage is permissible, like in wastewater and water treatment plants, pulp and paper mills and mining,1 the incorporation of lantern rings and water injection systems offers a solution for scenarios where even minimal leakage is not an option.
Mechanical seals typically use a rotating and stationary face to create a seal. The purpose of the mechanical seal is to control leakage from the stuffing box or seal chamber and prevent air from leaking back into the pump. The primary sealing elements include a rotating ring and a stationary ring. These are widely employed in applications where preventing leakage of hazardous or expensive fluids is critical, such as chemical processing.
Sealing products not only prevent leaks but also contribute significantly to the longevity and performance of pumps. However, with myriad sealing options available, choosing the appropriate one can be a daunting task. Understanding the sealing selection criteria is essential for ensuring optimal pump performance across various industrial sectors.
Ensuring Reliability
Failure in industrial pumps typically occurs due to issues in one of three major areas: the sealing system, the bearing system or hydraulic components. In particular, sealing and packing systems often require maintenance and experience downtime due to leaks or excessive wear.While some sealing issues can be mitigated through preventive maintenance, other sealing challenges occur unexpectedly and can severely compromise the reliability of the process. The consequences of a downed pump due to failing or condemned packing can have a significant impact on both a facility’s production and the asset itself.
Damaged pump shafts and improper installation are common causes of seal and packing failure that can lead to hazardous leakage, a lack of compliance with standard regulations, as well as economic impacts on a facility’s production. Therefore, operators must be aware of the key factors to consider before selecting a sealing solution to mitigate these risks.
Types of Pump Seals
Before considering the specific selection criteria for a pump’s seal, it is important to understand the types of sealing options available. There are three primary types of pump seals: compression packing seals, mechanical seals and radial shaft seals.Compression packing seals—consisting of braided or molded packing materials such as graphite, polytetrafluoroethylene (PTFE), aramid fibers or other synthetic fibers—often incorporate break-in lubricants to enhance their sealing performance and longevity. While packing seals are ideal for applications where minor leakage is permissible, like in wastewater and water treatment plants, pulp and paper mills and mining,1 the incorporation of lantern rings and water injection systems offers a solution for scenarios where even minimal leakage is not an option.
Mechanical seals typically use a rotating and stationary face to create a seal. The purpose of the mechanical seal is to control leakage from the stuffing box or seal chamber and prevent air from leaking back into the pump. The primary sealing elements include a rotating ring and a stationary ring. These are widely employed in applications where preventing leakage of hazardous or expensive fluids is critical, such as chemical processing.
Lip seals, also known as radial shaft seals, are primarily used for preventing the ingress of contaminants and retaining lubricants in rotating shaft applications. They are cost-effective options, commonly manufactured out of elastomers like nitrile butadiene rubber (NBR), and are available in spring-loaded and non-spring-loaded designs. These seals are located between rotating and stationary components. They have a cylindrical outer covering with an interference fit that seals statically against the housing bore and a sealing lip that seals dynamically and statically against the shaft. They are used extensively in industries like automotive manufacturing, the electric power generating industry, aerospace and food processing.
For pumps handling water or less hazardous fluids at lower pressures, packing remains the more practical and cost-effective choice. Thus, while mechanical seals are favored in certain scenarios, packing is typically the go-to sealing solution for the majority of pump applications.
Abrasive fluids may accelerate sealing wear, while viscous fluids may require specialized seal designs to prevent leakage. For toxic or hazardous fluids, containment and leak prevention are paramount, requiring seals with high reliability and tight tolerances.
This issue is particularly notable with pure PTFE packings, which have a thermal expansion coefficient roughly 12 times higher than steel. Research indicates that using engineered PTFE packings with fillers that more closely align to those of steel, such as barium sulphate and graphite, is a very effective way of combating this effect.3
Seals must also meet relevant standards and certifications to withstand operational demands and contribute to a safe working environment. Factors such as fire resistance, anti-explosive properties and compliance with environmental regulations should be considered.
As one navigates the complexities of industrial processes, the role of compression packing in ensuring smooth operations cannot be overstated. With proper attention and adherence to best practices, the reliability of pumps can be upheld, contributing to safer and more efficient industrial operations.
skf.com/ca/en/products/industrial-seals/power-transmission-seals/radial-shaft-seals
PVP2011-57751, The Influence on the Stuffing Box of the Forces Generated by Packing Thermal Expansion]
For pumps handling water or less hazardous fluids at lower pressures, packing remains the more practical and cost-effective choice. Thus, while mechanical seals are favored in certain scenarios, packing is typically the go-to sealing solution for the majority of pump applications.
Selection Criteria
Choosing the correct seal involves considering various factors to match the specific requirements of the application and the type of fluid being handled. To determine which type of seal is best for a particular application, it is important to consider the following selection criteria. Each factor influences the performance and longevity of the seal, guiding engineers in making informed decisions.Operating conditions
It is important to determine the temperature, pressure, shaft speed and specific gravity of the service as well as how it varies from one industry to the next. Each of these factors can influence the performance and longevity of pump seals. For instance, corrosive chemicals may require packing made from materials resistant to corrosion, while high temperatures might necessitate seals capable of withstanding thermal gradation.Fluid compatibility
As many materials are susceptible to the media they interact with, ensuring fluid compatibility is essential when selecting a sealing product. Contact with specific chemicals can lead to material degradation or cause adverse reactions, which can result in premature failure. Conducting a thorough assessment of fluid properties such as pH, viscosity and chemical composition is essential to choosing a seal material that offers optimal compatibility. Other factors to consider include corrosiveness, abrasiveness, toxicity, vapor pressure and boiling point.Abrasive fluids may accelerate sealing wear, while viscous fluids may require specialized seal designs to prevent leakage. For toxic or hazardous fluids, containment and leak prevention are paramount, requiring seals with high reliability and tight tolerances.
Seal material compatibility
Similar to fluid compatibility, it is important to consider how a material will react to the fluid it is exposed to. Seal materials will encounter process fluid and must therefore adhere to the service requirements of the media. Potable water service requires the use of a material certified to National Sanitation Foundation (NSF)-61, while other human consumption services might require products that comply with Food and Drug Administration (FDA), United States Department of Agriculture (USDA) or U.S. Pharmacopeia (USP) Class VI codes. Sealing materials that do not meet these strict guidelines might compromise the integrity of the media being processed.Seal material and thermal expansion
Friction between the packing material and the pump shaft generates heat during operation, causing the packing to thermally expand. If the thermal expansion coefficient of the packing substantially differs from that of the pump’s steel, it can initiate a cycle of escalating temperatures and internal stresses. This disparity can lead to increased shaft torque and the risk of scorching the packing. Conversely, during the cooldown phase, the material’s contraction can lessen gland stress, which may heighten leakage rates.This issue is particularly notable with pure PTFE packings, which have a thermal expansion coefficient roughly 12 times higher than steel. Research indicates that using engineered PTFE packings with fillers that more closely align to those of steel, such as barium sulphate and graphite, is a very effective way of combating this effect.3
Leakage tolerance
The acceptable level of leakage or fugitive emissions must be determined based on industry regulations, environmental considerations and safety standards. Seals with tighter leakage control mechanisms, such as mechanical seals or low-emission packing, may be necessary for applications where minimal leakage is imperative.Seals must also meet relevant standards and certifications to withstand operational demands and contribute to a safe working environment. Factors such as fire resistance, anti-explosive properties and compliance with environmental regulations should be considered.
Cost and life cycle considerations
Beyond initial installation, maintenance and life cycle costs are important considerations in seal selection. Seals that require frequent replacement or extensive maintenance can result in downtime and increased operational expenses. Opting for seals with longer service intervals or those that offer easy maintenance can contribute to overall cost savings over the life of the pump system. It is also important to consider the packing’s retrofitting possibilities, technical support availability, warranty, after-sales service and supplier reputation.Pump type
The intended function of the pump has a significant impact on which type of pump is used for any application. It is therefore important to consider the specific requirements of each pump type. The most common pump types include: rotodynamic, centrifugal, axial flow, mixed flow, plunger/piston, diaphragm, gear and screw.Look Out for Pitfalls
Avoiding common pitfalls in pump sealing involves a thorough upfront analysis of the application parameters. Proper maintenance practices, such as ensuring adequate lubrication and avoiding over-tightening packings, are essential for prolonging seal life and preventing failures. Additionally, attention to detail during installation and regular inspections can help mitigate potential issues before they escalate.Final Thoughts
Reliable seals are indispensable components of industrial pumps, impacting their efficiency, reliability and overall performance. By understanding the factors influencing seal selection and implementing best practices in maintenance and operation, industries can mitigate risks associated with seal failures and optimize the life span of their pumping systems.As one navigates the complexities of industrial processes, the role of compression packing in ensuring smooth operations cannot be overstated. With proper attention and adherence to best practices, the reliability of pumps can be upheld, contributing to safer and more efficient industrial operations.
References
pumpsandsystems.com/sites/default/files/webinars/2017/0606/Seals101-GrundfosWebinar.pdfskf.com/ca/en/products/industrial-seals/power-transmission-seals/radial-shaft-seals
PVP2011-57751, The Influence on the Stuffing Box of the Forces Generated by Packing Thermal Expansion]