On April 26, 1986, the worst nuclear accident in recorded history occurred at the Chernobyl nuclear plant in Ukraine, former Soviet Union. Poor reactor design and operator errors led to a steam explosion that left the reactor core on fire and exposed to the environment. The nuclear contamination was so severe that an exclusion zone covering over 1000 square miles was established and experts say the most contaminated areas will not be habitable again for 20,000 years.
Despite the fears that linger in the minds of those who remember Chernobyl, and Three Mile Island incident, many in the scientific community are looking to nuclear energy as an important component of global initiatives to reduce carbon emissions and greenhouse gases.
However, nuclear-generated electricity still plays a major role in the global power grid today. About 10% of all electricity worldwide comes from nuclear plants. In countries with advanced economies and infrastructure, that number is closer to 20%. The United States is home to 54 operating nuclear power stations with a combined 93 reactors over 28 states. These facilities produce over 770 billion kWh of electricity annually and an average reactor can produce 1 gigawatt (or 1 billion watts) of power. Additionally, a nuclear plant requires about 27 metric tons of enriched uranium annually to operate. Comparatively, a coal-fired plant requires about 2.5 million metric tons of coal to produce an equivalent amount of energy.
Even considering concerns related to the proper handling and storage of nuclear waste from spent fuel rods, and the fears that linger in the minds of those who remember Chernobyl and Three Mile Island, many in the scientific community are looking to nuclear energy as an important component of global initiatives to reduce carbon emissions and greenhouse gases. The bottom line is, even with modern technical advancements, burning carbon-rich fossil fuels like coal and natural gas generates massive amounts of CO2 emissions that in turn produce greenhouse gases that trap heat in the planet’s atmosphere and lead to global warming, that many agree threaten the future of the planet.
Result of boric acid corrosion.Image credit: https://www.nrc.gov/reactors/operati ng/ops-experience/vessel-head-degradation/vessel-head-degradation-files/looking-back-toward-nozzle3.html.
The chemical element Boron can absorb neutrons and slow the rate of the nuclear fission reaction. For this reason, Boron, in the form of boric acid is used as a control mechanism in nuclear reactors to adjust the reactor output. While boric acid plays an important role in both plant operation and safety, it also creates challenges of its own, as it is highly corrosive. In fact, it was a boric acid leak from the reactor coolant system that over time ate away at the reactor head at Davis Besse leading to the near-miss event.
Despite the fears that linger in the minds of those who remember Chernobyl, and Three Mile Island incident, many in the scientific community are looking to nuclear energy as an important component of global initiatives to reduce carbon emissions and greenhouse gases.
Renewed Perspective
The accident at Chernobyl had negative impacts that are still being felt around the world. Following the accident public distrust of nuclear energy ran rampant around the world. The Chernobyl accident occurred a mere seven years after another highly publicized incident, a partial meltdown of one of the reactors, occurred at the Three Mile Island nuclear plant in Middletown, Pennsylvania. The cry “Never another Chernobyl” became the mantra of nuclear opponents and the marching orders for anyone associated with overseeing the safe operation of nuclear facilities.However, nuclear-generated electricity still plays a major role in the global power grid today. About 10% of all electricity worldwide comes from nuclear plants. In countries with advanced economies and infrastructure, that number is closer to 20%. The United States is home to 54 operating nuclear power stations with a combined 93 reactors over 28 states. These facilities produce over 770 billion kWh of electricity annually and an average reactor can produce 1 gigawatt (or 1 billion watts) of power. Additionally, a nuclear plant requires about 27 metric tons of enriched uranium annually to operate. Comparatively, a coal-fired plant requires about 2.5 million metric tons of coal to produce an equivalent amount of energy.
Even considering concerns related to the proper handling and storage of nuclear waste from spent fuel rods, and the fears that linger in the minds of those who remember Chernobyl and Three Mile Island, many in the scientific community are looking to nuclear energy as an important component of global initiatives to reduce carbon emissions and greenhouse gases. The bottom line is, even with modern technical advancements, burning carbon-rich fossil fuels like coal and natural gas generates massive amounts of CO2 emissions that in turn produce greenhouse gases that trap heat in the planet’s atmosphere and lead to global warming, that many agree threaten the future of the planet.
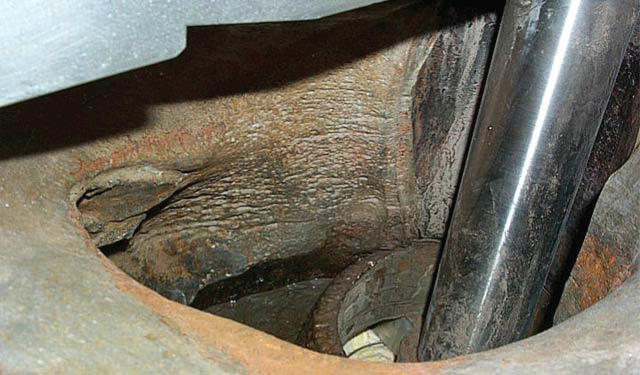
Taking Precautions
Improved reactor designs, advancements in fuel enrichment, increased oversight and regulation, and improved safety systems are some of the many reasons for an increased interest in nuclear power. Still, those working in and alongside the industry must remain vigilant as no industrial process is without risk and dangers. For example, the near miss at the Davis Besse plant in Ohio where maintenance workers discovered a football size void caused by boric acid corrosion in the reactor head in March of 2002.The chemical element Boron can absorb neutrons and slow the rate of the nuclear fission reaction. For this reason, Boron, in the form of boric acid is used as a control mechanism in nuclear reactors to adjust the reactor output. While boric acid plays an important role in both plant operation and safety, it also creates challenges of its own, as it is highly corrosive. In fact, it was a boric acid leak from the reactor coolant system that over time ate away at the reactor head at Davis Besse leading to the near-miss event.
One of the most critical sealing applications in nuclear facilities are the cooling system valves which can see up to 2000 ppm of boric acid within the water. In many industrial facilities, sealing of the water system is often a low priority. However, in a nuclear facility, if a valve leaks, over time the boric acid will crystalize around the stuffing box and destroy the packing. This can lead to serious leaks or failures, boric acid corrosion of critical equipment, and other related problems. Additionally, much of this system is within the containment region of the plant making replacement and repairs difficult, time consuming, and expensive due to radiation.
This is such a primary concern for nuclear power plants that most have a dedicated staff for monitoring and managing fluid leaks, and in particular boric acid-related maintenance issues. Many of these key plant personnel from plants and companies around the country come together annually at meetings of the Fluid Management Users Group (FLMUG) and the Boric Acid Users Group (BAUG) to share insights, information, and ideas. Additionally, the Electric Power Research Institute (EPRI) has worked with nuclear plants and key plant personnel to develop assessment guidelines and extensive technical reports to provide assistance and expertise to help drive improvement initiatives.
This is such a primary concern for nuclear power plants that most have a dedicated staff for monitoring and managing fluid leaks, and in particular boric acid-related maintenance issues. Many of these key plant personnel from plants and companies around the country come together annually at meetings of the Fluid Management Users Group (FLMUG) and the Boric Acid Users Group (BAUG) to share insights, information, and ideas. Additionally, the Electric Power Research Institute (EPRI) has worked with nuclear plants and key plant personnel to develop assessment guidelines and extensive technical reports to provide assistance and expertise to help drive improvement initiatives.
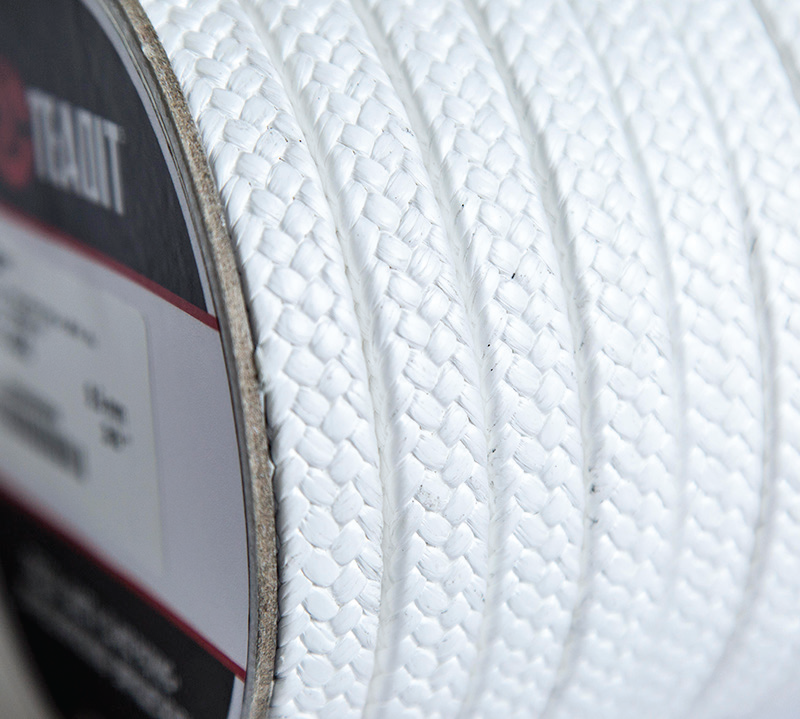
Valve Sealing in Reactors
Valve stem sealing is typically accomplished with mechanical packing material. The two most common packing materials in use today are polytetrafluoroethylene (commonly referred to as PTFE or by its trade name, Teflon) and graphite. PTFE offers advantages over graphite regarding sealability and stem friction or wear.PTFE is well known for its lubricity; long being a popular anti-stick coating on consumer goods like cookware. Additionally, PTFE, in its virgin form is inert to a wide variety of process media and is also an excellent dielectric insulator, helping to prevent galvanic corrosion. Most PTFE mechanical packing ‘yarns’ are made with an expanded form of the material which boasts exceptional tensile strength, making for a robust braided product. However, PTFE is not without its limitations. It has a limited temperature range making it unsuitable for applications above around 500F. Additionally, PTFE degrades in highly irradiated environments like those found near reactors in nuclear power plants.
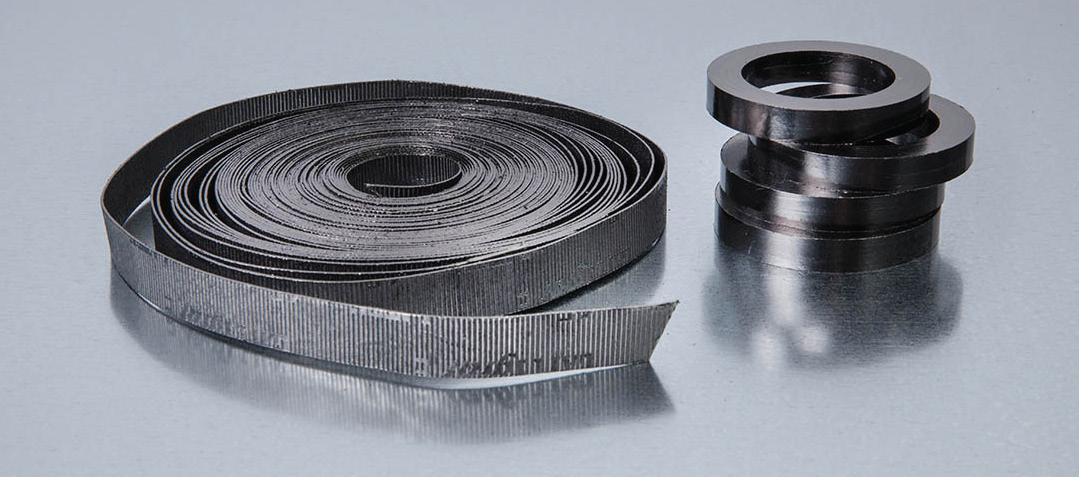
Flexible graphite packing has superior temperature resistance and can also withstand high levels of radiation, making it a popular choice for nuclear plants. Like PTFE, graphite is self-lubricating and boasts very good resistance to many process media. However, flexible graphite packing generates significantly more stem friction than PTFE and has poor dielectric properties allowing for galvanic corrosion of the stem and/or bonnet metals. Additionally, flexible graphite has low tensile strength making it significantly weaker than PTFE packing; it is highly susceptible to oxidation.
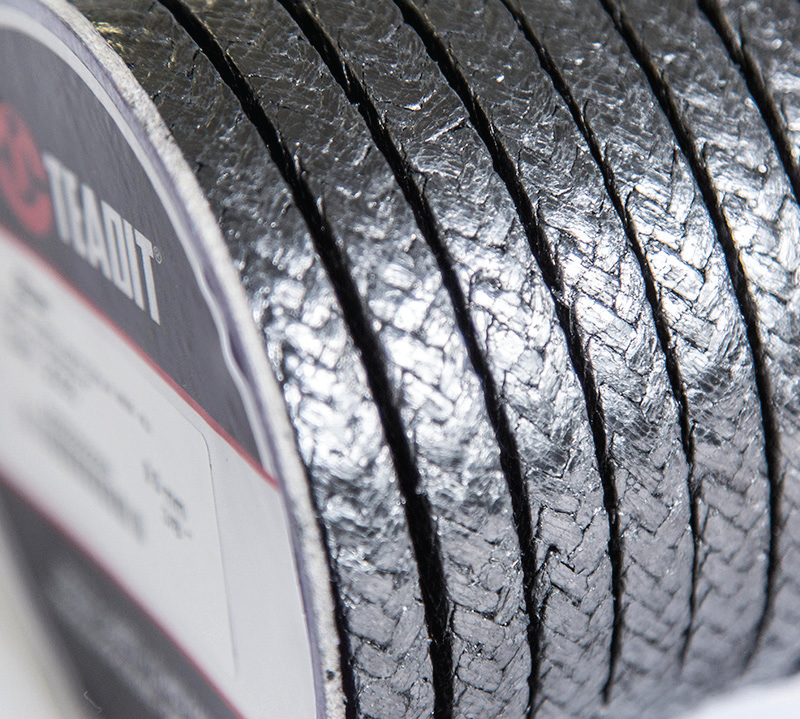
A popular form of packing for valve stems, especially in nuclear applications, is die-formed graphite. Rather than forming a braid using graphite ‘yarns’, this style of packing is made from thin layers of graphite ribbon that is wound around a mandrel to form a ring. The ring is then compression-molded in a die to mechanically bond the graphite layers together into an essentially solid ring of a prescribed density. Similar processes can be used to form other shapes as well, like chevron-shaped ‘cup and cone’ ring sets. Die-formed graphite ring sets often incorporate end rings of braided packing to help distribute the gland load and prevent extrusion.
It is worth noting, as it specifically applies to nuclear applications, any graphite material must be ultra-high purity, to ensure that it is free of neutron-absorbing materials that could impact the nuclear fission reaction (particularly boron). This high-purity graphite is commonly referred to as ‘nuclear grade.’
It is worth noting, as it specifically applies to nuclear applications, any graphite material must be ultra-high purity, to ensure that it is free of neutron-absorbing materials that could impact the nuclear fission reaction (particularly boron). This high-purity graphite is commonly referred to as ‘nuclear grade.’
Looking Forward
Time will tell if there is a renewed interest and investment in nuclear power here in the United States, though many experts believe it is inevitable as the demand for more and cleaner energy continues to rise. What is known for sure though is that, for nuclear plant operators, leak management, particularly as it relates to boric acid, is a primary focus. The stakes are high and high-profile incidents like the Davis Besse near-miss highlight the need to remain diligent.