By KCI Editorial
Flexible graphite has earned its reputation as a go-to sealing material across refineries and chemical plants. Its ability to withstand aggressive chemicals and extreme temperatures while conforming tightly to flange and stuffing box surfaces makes it ideal for low-emission valve packing applications.
As emission standards tighten and operating temperatures rise, this trusted material faces new challenges. TEADIT® investigates the performance boundaries of graphite in high demand valve packing applications, with particular attention to the effects of PTFE addition, to determine the requirements for reliable sealing under extreme operating conditions.
With industry standards evolving toward higher operating temperatures and more stringent emissions regulations, graphite is being pushed closer to its performance limits. Although renowned for its thermal resistance, graphite has a notable vulnerability: high-temperature oxidation.
At elevated temperatures, particularly in the presence of air, graphite begins to degrade, leading to a loss of both mass and sealing integrity. This becomes even more critical when polytetrafluoroethylene (PTFE) is introduced, a common practice for achieving low-emission certification. While graphite performs reliably at 260°C (500°F), its stability at higher temperatures, including 400°C (752°F) and 593°C (1100°F), is now under increased examination.
Why This Matters Now
In 2022, API 622¹ was updated to introduce high-temperature fugitive emission testing at 400°C (752°F) and included a new 24-hour step at 593°C (1100°F) in its weight loss test protocol. These updates reflect the industry’s growing demand to understand fugitive emissions at the upper range of service temperatures, where graphite’s oxidation behavior becomes a significant concern.
At TEADIT®, we set out to examine this issue head-on, testing multiple graphite grades and configurations. What we found confirms what many plant engineers have long suspected: not all graphite is created equal, and when PTFE enters the picture, the stakes climb quickly.
Testing Graphite in Isolation
To meet low-emissions standards, valve packing commonly combines flexible graphite tapes with Inconel ® reinforcement and PTFE impregnation. However, understanding graphite’s behavior in isolation is the first step in understanding how the full system will perform.
TEADIT® evaluated three commercially available, oxidation-inhibited graphite tapes, each tested using thermogravimetric analysis (TGA) from 400°C (752°F) to 700°C (1292°F). The procedure was based on Hantz, B. F. 3 , FSA Test Method B 4 , and IOGP S-601 Annex E 2 , all of which include a high-temperature hold to expel moisture, mirroring API 622¹ methodology.
Figure 1: The three graphite types tested under high-temperature TGA conditions.
In practical terms, a graphite material is considered oxidation-inhibited if its oxidation rate stays below 4%/h when subjected to a 4-hour isotherm stage at 670°C (1238°F). While all three tapes in this study met this benchmark, the differences in performance were significant.
Graphite I and II, both high-quality inhibited materials, demonstrated excellent thermal stability, with oxidation rates consistently under 1%/h. Graphite III, on the other hand, approached the upper limit of acceptable performance, reaching 3.35%/h at 670°C (1238°F). These differences become even more pronounced at 700°C (1292°F).
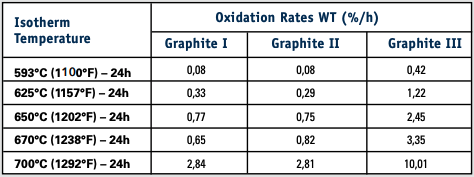
Table 1: Weight Loss Rate for the different graphite tapes.
The takeaway is clear: although all materials tested qualify as oxidation-inhibited, their oxidation rates varied under high-temperature oxidative conditions. These differences become relevant depending on service environment, especially in applications where oxygen exposure is significant.
Form Factor Matters
After characterization of the graphite tapes, TEADIT® asked a practical question: Do these results still hold when graphite is combined with other components, like Inconel ® or PTFE?
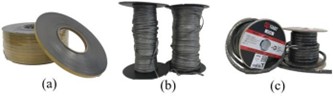
Figure 2: Comparison of the flexible graphite tape (a), the yarn (b), and the packing (c).
To find out, TEADIT® tested flexible graphite in three different forms:
• The tape: The base flexible graphite tape;
• The yarn: Knitted yarn made of graphite tape reinforced with Inconel ® ;
• The packing: PTFE impregnated packing, the final product used in valves.
As thermogravimetric analysis (TGA) is limited to small sample sizes (typically under 10 mg), TEADIT® conducted these tests in an open-air muffle furnace, following the guidelines of FSA Test Method A⁴ and IOGP S-601 Annex E.² No forced air supply or atmospheric control was applied, replicating real-world oxidative environments more accurately.
The results were confirmed: the complete packing systems exhibited significantly higher weight loss rates when compared to both the tape and yarn forms. However, the type of graphite still played a critical role in performance.
While the packing made with all three graphite types showed increased oxidation compared to isolated graphite types, the trend held; materials made with Graphite III degraded at more than twice the rate of those using Graphite I or II. PTFE impregnation, frequently used to enhance emissions control, was shown to accelerate oxidation at high temperatures across all tested graphite types. The effect was more pronounced when combined with graphite grades that already exhibited higher oxidation rates in tape form.
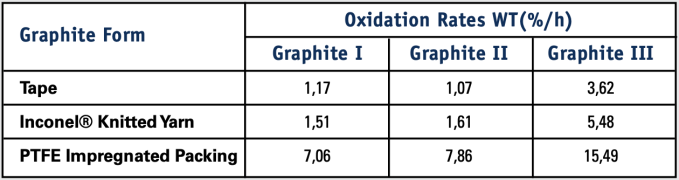
Table 2: Weight Loss Rate comparison for different forms of graphite – muffle oven(4h @ 670°C/1238°F).
The results confirmed that although the oxidation grade of graphite has a critical role, the material’s form factor and the presence of additives, such as PTFE, also have a significant impact on its longterm thermal resistance.
In real-world valve packing applications, testing individual materials in isolation is insufficient; it is essential to evaluate how composite materials perform under actual operating conditions.
Simulating Real Conditions
While lab-based material and form factor tests provide critical insight into oxidation behavior, they cannot fully replicate the operating conditions inside a valve. To close that gap, TEADIT® developed a custom stuffing box test rig designed to simulate the real-world environment a packing set experiences under sustained thermal load.
Our goal was to assess how a fugitive emission packing would behave in a critical thermal exposition situation. Two packing styles were prepared using Type III graphite and the following combination of materials:
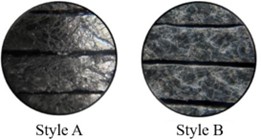
Figure 3: Packing Styles A (No PTFE impregnation) and B (with PTFE impregnation).
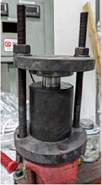
Figure 4: Stuffing Box Testing Rig used for oxidation simulations.
• Style IIIA: Knitted yarn with Inconel®, no PTFE impregnation • Style IIIB: Identical to Style IIIA, but with PTFE impregnation
The packings were cut into rings and installed into the test rig at a controlled compressive stress of 73 MPa, simulating actual packing installation. The entire assembly underwent thermal cycling: one hour at 150°C (302°F) to simulate valve startup and remove residual moisture, followed by a sustained 24-hour exposure at 593°C (1100°F) to assess oxidation behavior.
The results of the stuffing box test rig showed that packing degradation is significantly lower when confined inside a stuffing box than when exposed in open air. The reduction of oxygen availability within the confined geometry likely slowed down the oxidation reaction.
While the confined environment reduced overall degradation, graphite grade and formulation still influenced performance. Style IIIB (Graphite III + PTFE) showed higher weight loss, consistent with earlier observations, though all tested configurations exhibited oxidation progression under sustained thermal exposure.
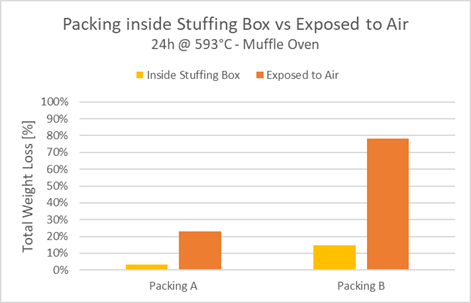
Figure 5: Comparison of Weight Loss for Packings in Muffle vs. Stuffing Box.
To better understand oxidation progression under moderate temperatures, Style IIIB was tested across a range of isothermals, ranging from 400°C (752°F) to 593°C (1100°F). Results showed a steep increase in weight loss as temperatures approached API 622¹ highest temperature step.
Even within a sealed environment, packing degradation becomes severe as temperature rises, especially with PTFE present. However, the difference between 14% and 78% weight loss at 593°C (1100°F) demonstrates the significant impact of testing in a muffle versus in a confined environment.
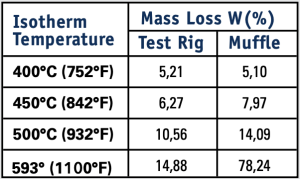
Table 3: Weight Loss results for packing IIIB from 400°C (752°F) to 593°C (1100°F).
Key Takeaways
All tested graphite grades met the criteria for oxidation-inhibited materials, with weight loss rates below 4%/h at 670°C (1238°F). While some variation in oxidation behavior was observed, this remained within acceptable industry thresholds.
TGA and muffle oven testing produced consistent results, reinforcing that both methods are valid for evaluating oxidation resistance. Muffle testing can be a reliable alternative when TGA sample limitations exist.
PTFE impregnation, while critical for meeting low-emission requirements, significantly increased oxidation rates under elevated temperatures in the presence of oxygen. This trend was consistent across all graphite types.
Simulating real-world conditions using a stuffing box test rig resulted in remarkably lower oxidation rates compared to open-air testing.
Confinement reduces oxygen exposure, thereby slowing degradation. This highlights the importance of considering installation geometry when evaluating long-term packing performance.
Looking Ahead
With fugitive emissions regulations tightening and service temperatures climbing, it is no longer enough to rely on assumptions or basic certifications. We must understand how materials behave across all configurations and conditions.
The good news? TEADIT® now has the tools and data to make more informed decisions. At TEADIT®, we are committed to helping engineers, technicians, and operators make informed choices for the most demanding applications.
In sealing, confidence comes from chemistry and engineering processes. The test outlined in this work highlights that chemistry can be unforgiving at high temperatures.
REFERENCES:
1. API STANDARD 622. Type Testing of Process Valve Packing for Fugitive Emissions. Third Edition, 2018. Addendum 1, 2022.
2. IOGP S-611. Supplementary Requirements to API 600 Steel Gate Valves and to API 603 CRA Gate Valves. International Association of Oil & Gas Producers. 2019.
3. Hantz, B. F. Oxidation Inhibited Graphite: What is it? ASME Pressure Vessels and Piping Conference. 2017.
4. FSA-G-604-07. Oxidation Test Standard for Flexible Graphite Gasket Materials. Fluid Sealing Association. 2007.