As the world pivots towards sustainable energy solutions, hydrogen production through electrolysis has emerged as a vital component in the global energy transition. Electrolysers, which split water into hydrogen and oxygen using electricity, are at the heart of this process.1
The efficiency and longevity of these systems are critically dependent on the integrity of their sealing gaskets, which play an essential role in ensuring the overall effectiveness and reliability of the process.
Understanding Electrolyser Components
An electrolyser is a device that uses electricity to drive a chemical reaction, specifically the splitting of water (H₂O) into hydrogen (H₂) and oxygen (O₂). This process, known as electrolysis, is fundamental in producing green hydrogen, a clean energy source that comes from renewable energy sources like wind, solar, or hydropower and can be used in various industries, including transportation, power generation, and chemical manufacturing.There are two primary types of electrolysers: Alkaline Electrolysers (AEL) and Proton Exchange Membrane (PEM) electrolysers.
Alkaline Electrolysers (AEL) have been used for decades and operate using a liquid electrolyte, usually potassium hydroxide (KOH), to conduct electricity. They are known for their durability and lower capital costs but are typically larger and less responsive to fluctuations in power supply.
Proton Exchange Membrane (PEM) use a solid polymer electrolyte, are more compact, can achieve higher current densities, and produce hydrogen at higher purities. They are often preferred for applications that require rapid start-up and integration with intermittent renewable energy sources. The primary drawback of PEMs is their higher cost due to the use of precious metals like platinum and iridium in their construction.
The efficiency of the electrolyser depends on how effectively this process occurs. High-efficiency electrolysers minimize energy losses and reduce the operational costs of hydrogen production, making the overall process more economically viable. Factors such as the quality of the electrodes, the effectiveness of the membrane, the purity of the input water, and the sealing gaskets all contribute to the electrolysers’ efficiency and, ultimately, the cost-effectiveness and sustainability of hydrogen production.
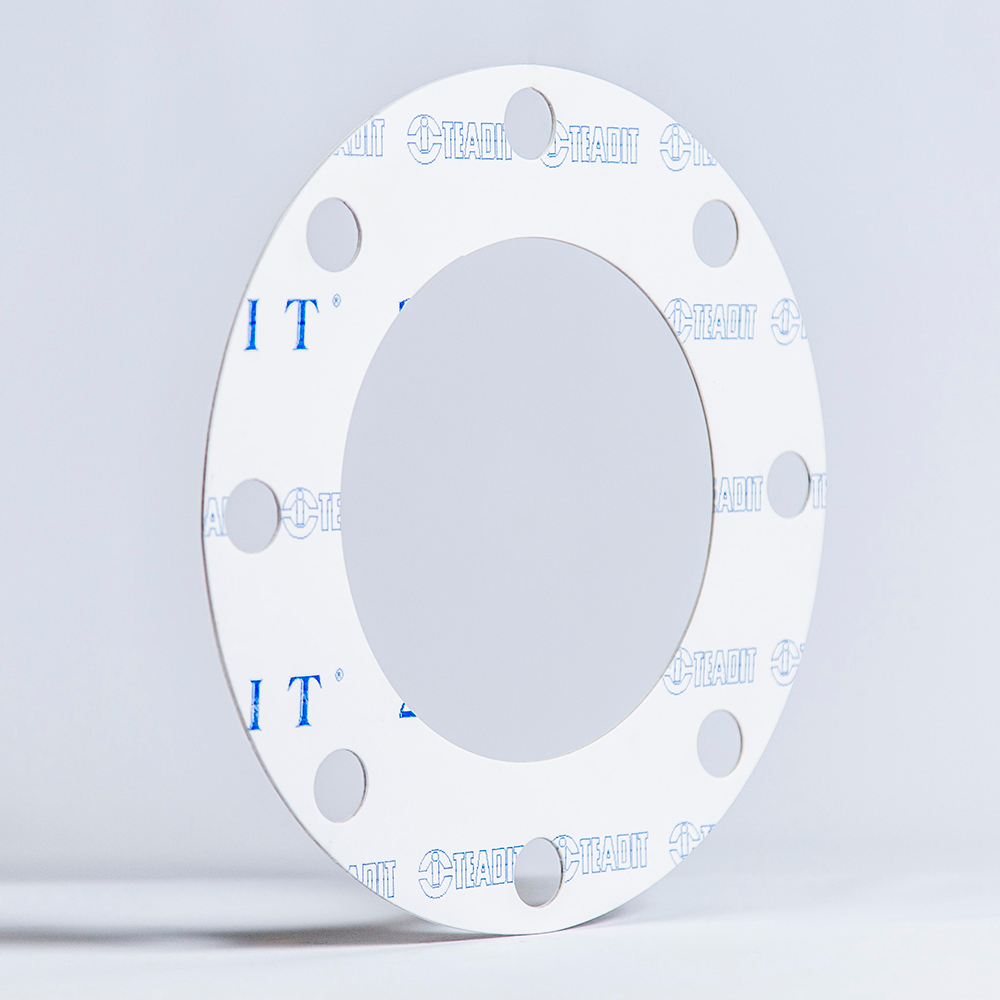
24SH ePTFE Gasket Sheet
The Importance of Gaskets
In an electrolyser, cell frames are used to separate the individual cells that house the unit’s anode and cathode. Positioned between each cell frame, gaskets prevent leaks, maintain system pressure, preserve the purity of the hydrogen produced, maintain electrical insulation, and ensure overall efficiency.In addition to preventing leaks, a well-functioning gasket must withstand the compression forces exerted by the plates and frames, ensuring that they do not deform or intrude into the flow channels. Any such intrusion could block the flow of gases or liquids, reducing the electrolysers’ efficiency.
Understanding which gasket materials and fabrication methods result in the most reliable seal can help safeguard against unnecessary risks and ensure that the gasket is compatible with the electrolysers’ operational environment.
Material Selection
When it comes to gaskets, Polytetrafluoroethylene (PTFE) is renowned for its exceptional chemical resistance, thermal stability, and insulative and low friction properties. It is virtually inert to almost all chemicals, making it an ideal material for the harsh environments within electrolysers. However, not all PTFE gaskets are created equal. The performance characteristics of PTFE gaskets can vary significantly based on their manufacturing processes and the quality of the raw materials used. PTFE gaskets can be broadly categorized into three types:• Skived PTFE
• Structured PTFE
• Expanded PTFE
Skived PTFE
Skived PTFE gaskets are produced by slicing thin layers from a solid PTFE billet in a process known as skiving. While skived PTFE retains the inherent chemical resistance of PTFE, it has a higher tendency for creep and cold flow under load due to its relatively low mechanical strength. Creep is the tendency of a solid material to slowly move or deform under mechanical stresses. In gasket applications, this means that over time, especially under sustained pressure and temperature, skived PTFE gaskets may flow, leading to a loss of sealing integrity.Structured PTFE
Structured PTFE gaskets are manufactured by introducing fillers—such as hollow glass microspheres, barium sulfate, or silica—into the PTFE matrix, followed by a calendering process. The combination of these two important steps not only enhances the mechanical properties of PTFE by reducing its tendency to creep but also orients the PTFE molecules, resulting in improved strength and stability. The fillers interlock with the PTFE molecules, creating a more robust structure and imparting different properties depending on the filler type used. Structured PTFE gaskets exhibit better load-bearing capabilities and reduced deformation under stress, making them reliable for long-term applications.Expanded PTFE
Expanded PTFE (ePTFE) gaskets are produced through a specialized process that expands the PTFE material, creating a microporous structure with multidirectional strength. This expansion results in a gasket material that combines excellent chemical resistance with superior mechanical properties, including high compressibility and resilience. The multidirectional fibrillation of PTFE molecules enhances its strength and reduces creep. ePTFE gaskets, such as Teadit 24 SH, have a lower tendency for creep and can maintain a reliable seal over extended periods, even under fluctuating temperatures and pressures. Additionally, ePTFE gaskets are very soft and conform easily to flange surfaces, effectively sealing even surfaces with minor imperfections or irregularities.Connecting Material Choice to Electrolyser Performance
Selecting skived PTFE gaskets in electrolyser applications poses risks due to their propensity for creep, which can lead to seal failure over time. This is particularly detrimental in electrolysers, where maintaining a consistent seal is vital for efficiency and safety. The loss of seal integrity can result in gas leaks, cross-contamination of the gas flow channels, and decreased system performance.In contrast, structured and expanded PTFE gaskets offer improved mechanical strength and reduced creep, making them more suitable for demanding environments within both PEM and alkaline electrolysers. Their enhanced properties ensure that the gaskets can withstand operational stresses over the long term, maintaining seal integrity and contributing to the overall efficiency and reliability of the hydrogen production process. Furthermore, PTFE fluoropolymers provide excellent electrical stability across various environmental conditions, setting them apart from other insulating materials. For reference, pure PTFE exhibits superior electrical properties, with a high dielectric strength of around 24 kV/mm.
For example, in PEM electrolysers, where gaskets must perform under limited bolt preload and very thin gasket thicknesses, structured PTFE gaskets like Tealon 1570 are particularly effective. The incorporation of fillers enables these gaskets to maintain a reliable seal even under the lower bolt loads typically found in PEM systems.
On the other hand, in alkaline electrolysers, expanded PTFE gaskets like Teadit 24 SH are widely used and can withstand harsh operating conditions without significant degradation. This resistance to chemical attack extends the service life of the gaskets, reducing the need for frequent maintenance and replacement.
Thanks to their chemical resistance, mechanical strength, and performance-enhancing fillers, both structured and expanded PTFE gaskets offer versatile solutions for different electrolyser types. While this article highlights a few examples, additional expanded and structured PTFE gaskets can also be specified or custom-selected to meet the unique requirements of each electrolyser. Even within PEM or alkaline electrolysers, variations in design, operating conditions, and performance requirements may necessitate different gasket solutions to ensure optimal sealing performance.
Challenges and Innovations
The development of gaskets for electrolysers is an ongoing process, with manufacturers continuously testing and refining their products to meet the specific needs of different electrolyser technologies. One of the key challenges in this field is ensuring that gaskets can withstand the operating temperatures and pressures typical of hydrogen production without losing their sealing capabilities.For instance, some materials initially considered suitable for alkaline electrolysers have been found to have chemical incompatibility issues. In highly alkaline environments, certain gasket materials may degrade or react chemically, leading to premature failure and potential safety hazards. This highlights the importance of selecting materials specifically suited to the chemical environment within the electrolyser.
Achieving Optimal Sealability
To achieve high sealability in electrolysers, it is essential to consider several factors:1. Material Compatibility: Ensure the gasket material is chemically compatible with the electrolysers’ fluids, gases, and electrolytes.
2. Sealability Performance: Choose a gasket that can provide an effective seal with the available bolt preload, ensuring reliable sealing with the given mechanical constraints.
3. Mechanical Properties: The gasket must have the appropriate compression and stress resistance to maintain a seal without deforming or intruding into flow channels.
4. Temperature and Pressure Resistance: The gasket material should withstand the operating temperatures and pressures without losing its sealing properties.
5. Durability: Long-term chemical and mechanical degradation resistance is crucial to reduce maintenance costs and ensure continuous operation.
Final Thoughts
The role of gaskets in electrolysers cannot be overstated. As the demand for hydrogen production grows, the need for reliable, high-performance sealing solutions will only increase. By focusing on material compatibility, mechanical resilience, and durability, manufacturers can ensure that their gaskets contribute to the efficient and safe operation of electrolysers. As research and development in this field continues, one can expect even more advanced gasket solutions tailored to the specific needs of this critical technology.Reference and Resource
1. https://www.mckinsey.com/industries/oil-and-gas/our-insights/global-energy-perspective-2023-hydrogen-outlook